МДФ плиты МДФ – это плитный материал, изготовленный из высушенных древесных волокон, обработанных синтетическими связующими веществами и сформированных в виде ковра с последующим горячим прессованием (плотностью 700-870 кг/м3) и шлифовкой. МДФ возникли как дальнейшее развитие сухого способа производства ДВП с учетом совершенствовавшихся при изготовлении ДВП технологий. Аббревиатура МДФ представляет собой кальку с английского MDF – Medium Density Fiberboard, что в переводе с английского означает «среднеплотное волокнистое покрытие» (СпВП). В среднеплотных волокнистых плитах развитая поверхность древесных волокон и сокращенный цикл прессования эффективно сочетаются с прочностью за счет участия связующих веществ в межволоконном взаимодействии. В России отсутствует ГОСТ на производство ДВП плит сухого способа прессования. Существующие производители либо производят его по собственно разработанным ТУ, либо по европейским стандартам. В последнем случае Стандарт EN 622-5 регламентирует требования к плитам MDF и различает в этой продукции следующие марки: • MDF – общего назначения; • MDF.H – общего назначения влагостойкие; • MDF.LA – конструкционные; • MDF.HLS – конструкционные влагостойкие. При изготовлении столешниц чаще других используются плиты МДФ толщиной 24 мм и 32 мм. Фанера Фанера, являясь универсальной продукцией с высокими техническими характеристиками, производится из разнообразной древесины как твердых (береза, бук, осина) так и мягких пород (ель, сосна и пихта), многие из которых имеют привлекательный внешний вид поверхности. Фанера имеет высокую стабильность размеров и прочность в продольном и поперечном направлениях. Фанера в основном производится из лущенного шпона. Cлои шпона соединяются вместе при помощи связующего (клея), который соответствует конечному назначению фанеры. Клей твердеет при прессовании фанеры под воздействием повышенной температуры. Направление волокон в прилегающих слоях шпона расположено перпендикулярно друг другу. Внешние и внутренние слоя располагаются симметрично с каждой стороны относительно центрального слоя шпона. В то же время, если внутренние слои шпона соединяются параллельно направлению волокон наружного слоя, фанера имеет более высокие прочностные характеристики в этом направлении. Клей, применяемый для изготовления фанеры, классифицируется в зависимости от конечного использования фанеры (для наружного и внутреннего применения): карбамидно-формальдегидный (UF) - подходит только для внутреннего применения); меламино-карбамидно-формальдегидный (MUF) - подходит для влажных условий и ограничено для наружного применения; фенольно-формальдегтдный (PF) - подходит для влажных условий и для наружного применения. Плотность панели и соответственно, ее масса, различаются в зависимости от используемой древесины. Большая часть конструкционной фанеры имеет плотность в пределах от 400 до 700 кг/м3. Некоторые виды прессованной под высоким давлением специальной (пуленепробиваемой) фанеры могут иметь плотность больше чем 1000 кг/м3. Долговечность фанеры зависит от качества связующего, породы древесины и качества шпона. Специальное покрытия поверхности или пропитка также увеличивают ее долговечность. Шлифованная и многослойная фанера широко применяется при строительно-монтажных и отделочных работах. Так, строительная фанера применяется для возведения сооружений, опалубок, перегородок, основы под кровлю, полы, облицовывания стен зданий, транспорта, судов, для производства мебели, подоконников, дверей, тары и др. Тамбурат 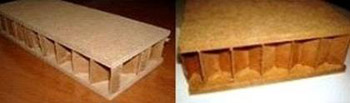
Тамбурат – современный вид плиты, состоящий из двух листов древесного материала (фанера, ХДФ), между которыми находится слой гофробумаги (гофрокартона), напоминающий по своей структуре соты. В отличие от ДСП тамбурат обладает необычайной легкостью, поэтому не подвергается деформации под тяжестью собственного веса, отлично сохраняя первоначальную (прямолинейную) форму. При изготовлении столешницы из тамбурата необходимо учитывать, что для упрощения работы сборщиков мебели и возможности применения традиционной фурнитуры и крепежа толщина наружных слоев сотовой панели не должна быть меньше 6 мм. При кромлении такой плиты сложности могут возникнуть при толщине свыше 40 мм, в обратном случае, также можно использовать традиционные способы. Среди важнейших параметров: настройка давления прижима в процессе механизированного раскроя и отделки кромок, температура и давление, необходимые для облицовывания плит бумажно-слоистым пластиком. Классическая схема нагружения сотовых панелей 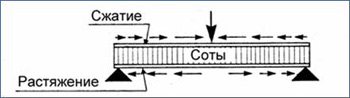
* верхняя обшивка работает на сжатие; нижняя обшивка работает на растяжение; сотовый заполнитель работает на сдвиг. |