Описание процесса Процесс Snamprogetti производства карбамида известен во всем мире. Процесс разделяется на шесть частей: • синтез и восстановление при высоком давлении (ВД) • очистка и восстановление при среднем давлении (СД) • очистка и восстановление при низком давлении (НД) • вакуумная концентрация • процесс очистки конденсата • завершающий этап: приллирование Диаграмма процесса 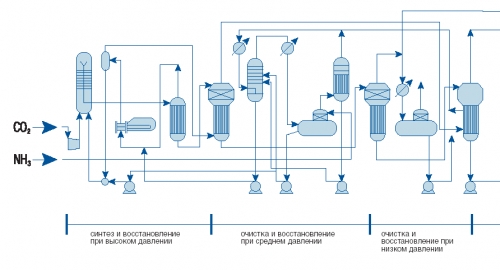
Синтез и восстановление при высоком давлении (ВД) В дополнение к оборудованию высокого давления, которое требуется для подачи аммиака и двуокиси углерода и рециркуляции аммиачно-карбаматного раствора, эта часть включает в себя: 1. реактор, где образуется карбамид отпарную колонну, необходимую для отделения в виде паров из раствора карбамида, выходящего из реактора, большого количества аммиака и двуокиси углерода, не превратившихся в реакторе в карбамид; 2. карбаматный конденсатор, в котором происходит конденсация этих паров; 3. эжектор, с помощью которого аммиачно- карбаматный раствор рециркулируется в реактор. В этом оборудовании давление поддерживается на сходном уровне, 150 бар, а температуры растворов на выходе составляют 188, 205 и 155° С для реактора, регенератора и карбаматного конденсатора, соответственно. В технологии Snamprogetti для реактора, где образуется карбамид, характерна высокая пропорция аммиака/двуокиси углерода (NH3/CO2 =3.2-3.4 грамм-молекул) и низкая пропорция воды/двуокиси углерода (0.4- 0.6 грамм-молекул). Внутри реактора установлено соответствующее количество поддонов очень простой конструкции для улучшения процесса синтеза. В этих условиях (синтеза) 62-64% общего количества CO2, поступающего в реактор, превращается в карбамид. Всего же на этапе синтеза при высоком давлении (или замкнутого цикла) процент превращения двуокиси углерода составляет 85-90%. Все оборудование в этой части, самое тяжелое из оборудования предприятия по производству карбамида, устанавливается на нулевом уровне, что обеспечивает его горизонтальное расположение со всеми соответствующими выгодами. Пар среднего давления потребляется лишь в двух единицах заводского оборудования: регенераторе и гидролизаторе отделения сточных вод. Количество пара, потребляемое в регенераторе, практически полностью восполняется в карбаматном конденсаторе: в нем давление ниже, но все же достаточное для использования на самом заводе по производству карбамида. Даже в условиях жесткой эксплуатации оборудованию этой части гарантируется безопасное использование в течение более 20 лет. Количество кислорода, потребляемое на заводе из воздуха, составляет 0,25% от объема подаваемой двуокиси углерода. Такое минимальное количество одновременно гарантирует отличное пассивирование оборудования и отсутствие взрывчатых смесей, когда «инертные компоненты» выбрасываются заводом в атмосферу после практически полного очищения от содержащегося в них аммиака. Благодаря правильному выбору материалов, контактирующих с перерабатываемыми жидкостями, и наличию избыточного количества аммиака есть возможность в периоды внеплановых остановок производства всего на несколько дней, используя несколько клапанов, пускать процесс синтеза при высоком давлении по замкнутому циклу, сохраняя, соответственно, все применяемые в процессе растворы внутри цикла. Таким образом, проблемы, связанные с загрязнением и возобновлением (пуском вновь) производства полностью исключаются. Все типы оборудования (поршневое и центрифуги) используются в соответствии с местными условиями или просьбами клиентов. 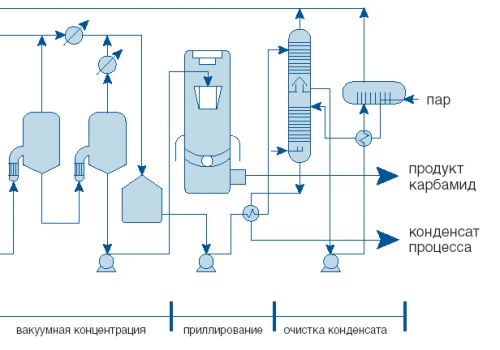
Очистка и восстановление при среднем давлении (СД) Целью этой части процесса является частичное отделение реагентов, аммиака и двуокиси углерода от раствора карбамида и после их конденсации в воде рециркуляция полученного раствора в реактор вместе с водным раствором аммиака и двуокиси углерода, полученным на более поздних стадиях заводской переработки. Избыток аммиака отделяется в этой части процесса и отдельно направляется в реактор. Для этого имеется колонна-дистиллятор. Рабочее давление составляет 17 бар. В этой части процесса имеется одна конструктивная особенность. Аммиак и двуокись углерода частично концентрируются в оболочке устройства предварительного нагрева в вакуумном отсеке, и таким образом часть энергии утилизируется в виде 200 кг пара на каждую тонну карбамида, что обеспечивает окупаемость вложенных средств, даже на уже действующих заводах, менее чем за два года. Другой особенностью части процесса при среднем давлении является очистка т.н. «инертных компонентов» (СО, Н2 и СР4 содержащихся, главным образом, в двуокиси углерода и пассивирующем воздухе). Как уже подчеркивалось, количество пассивирующего воздуха в технологии Snamprogetti весьма невелико (одна треть в сравнении с другими технологиями). Поэтому легко утилизировать аммиак из «инертных компонентов», не подвергаясь при этом риску взрыва главным образом из-за наличия смесей Н2/О2. Из двуокиси углерода не требуется удаления водорода. По специальным запросам Snamprogetti разработаны и уже установлены на промышленных предприятиях другие системы очистки. Для полного удаления аммиака, содержащегося в «инертных компонентах», в абсолютно безопасных с точки зрения взрывов условиях Snamprogetti запатентован метод очистки, который уже применяется на некоторых заводах. Он состоит в очистке «инертных компонентов» водой после добавления некоторого количества горючего газа, например природного газа, в таком объеме, что после удаления аммиака состав «инертных компонентов» не представляет опасности взрыва из-за избытка горючего газа. Очищенные «инертные компоненты» сжигаются в топке вместе с горючим газом. Следует подчеркнуть, что наличие части процесса при среднем давлении обеспечивает большую гибкость установке, которой можно управлять при самых разнообразных соотношениях NH3/CO2, при том, что избыток аммиака в потоке карбамида из регенератора утилизируется и конденсируется на стадии среднего давления. Кроме того, хотя в принципе контроль за пропорцией NH3/CO2 в процессе замкнутого синтеза и важен, но на практике, благодаря наличию стадии среднего давления допустимы некоторые отклонения, и в процессе Snamprogetti нет необходимости осуществлять строгий контроль за соотношением NH3/CO2.
|