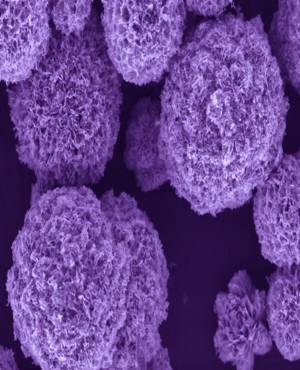
Измельчение, как технологическая операция, - фундамент, на котором базируется всё современное материальное производство. От качества и свойств порошковых материалов зависят сложность, материалоемкость и энергоёмкость процессов производства изделий. На процессы дробления и измельчения материалов расходуется более 20% всей производимой в мире электроэнергии. В мире зарегистрировано 110тыс. месторождений минералов. На каждое из них построено предприятие, где используются в среднем по 5-10 шаровых мельниц, период замены этих мельниц составляет 8-12 лет. На шаровые мельницы приходится до 95% мирового объёма переработки (включая и тонкое измельчение) сырьевых материалов. Остальные 5% рынка, в основном, для сверхтонкого измельчения, занимают другие типы измельчительного оборудования, такие как струйные, планетарные, валковые, вихревые, бисерные мельницы, дезинтеграторы и так называемые электро-импульсные, кавитационные, плазмо-кавитационные, магнито-импульсные способы получения порошковых материалов. Эти мельницы и способы измельчения не получили широкого распространения из-за низких КПД и производительности, ограниченного ресурса и сложности организации выпуска порошков в промышленных масштабах. Огромные энергетические затраты на операции сверхтонкого и нанопомола, обусловили многочисленные исследования, направленные на повышение рентабельности помольного оборудования и разработку новых устройств и способов получения нанопорошков. При огромных финансовых вложениях, научно - техническом потенциале ведущих мировых компаний, проблема создания оборудования и эффективного способа получения нанопорошков до сих пор не решена. Основной упор делается на повышение эффективности существующих типов помольного оборудования, в основном это шаровые и струйные мельницы. Проще усовершенствовать сложнейший процессор, поднять производительность в 2-3 раза, чем повысить эффективность мельниц на 2-3%. При режимах сверхтонкого и нанопомола, КПД мельниц снижается до 0,1-0,001%. Получается, что при некоторых режимах помола, более 99,99% от подводимой к материалу энергии идет не на уменьшение размеров частиц, а на тепло, которое выделяется при измельчении материалов. Это тепло создает огромные, практически непреодолимые проблемы для производства качественных порошковых материалов с высокими технологическими свойствами. Поэтому современные микро и особенно нанопорошки имеют высокую с/стоимость, низкое качество и свойства, что ограничивает масштабы производства, спроса и их применение. Как известно, кроме механических способов производства микро и нанопорошков, существуют химические и плазмохимические, которым присущи общие проблемы, помимо размеров частиц, определяющих свойства продукта. Более важным является сохранение химического состава и поверхностной активности порошков. Известные типы оборудования, технологии и способы принципиально не способны решить эти проблемы, так как относятся к высокотемпературным технологиям. Это классическое механическое измельчение, испарение и конденсация, химическое осаждение и другие способы, протекающие в интервале температур 310-10 000оК. При таких температурах сохранить высокую активность микро и нанопорошков невозможно. Компания "НИнга-Технология" решила проблему создания эффективного промышленного помольного оборудования для производства сверхактивных, высокотехнологичных микро и нанопорошков в любом агрегатном состоянии! "НИнга-Технология" разработано и изготовлено технологическое оборудование для реализацией проекта: "производство 40тыс.т/год микроталька М05N и М03". Были изготовлены две мельницы МН7, которые должны были обеспечить компании "Декор" (г. Москва), дочерняя компания "АKZO NOBEL " (мировой лидер на рынке лакокрасочных и строительных материалов). Из сравнительного анализа, произведенный на мельнице МН7 микротальк превосходит по своим характеристикам, и особенно по технологическим свойствам лучшие мировые образцы. Ниже представлены сравнительные данные и комментарий на микро и нанотальк МН7 и ведущих мировых производителей микроталька. Хотелось бы особо отметить, что в мире нет официальных производителей, к которым можно обратиться и заказать нанотальк. Есть производители при университетах и небольшие опытные производства при компаниях, которые производят до 1-2кг в день и все эти технологии, очень затратные, дорогие и поэтому не востребованы. Потенциальный оборот продукта может составить до $35-45млн. и получать чистую прибыль $15-25млн. Решения инвестором по прекращению финансирования проекта было принято 10.02.2004г на основании представленный молодыми и неопытными сотрудниками компании инвестора, некомпетентной оценки реальных перспектив рынка микро и наноталька, как бизнеса и состояние дел в компании. Несмотря на сложную ситуацию, работы продолжались до июня 2004г и 10.05.2004г нами были получены образцы микроталька(нано) МН. Микро - нанотальк МН тестировался в лаборатории ЗАО "Акзо Нобель Декор" (г. Москва), дочерняя компания "АKZO NOBEL" (мировой лидер на рынке лакокрасочных и строительных материалов). В октябре 2009г к нам обратилась компания "ЭТН" о возможности производства на оборудовании и по технологии МН (мельница МН7 рис.2) микроталька D50(2мкм) и D95(2мкм) для поставок на рынок западной Европы в количестве 24тыс.т/год=2,8т/час. С аналогичным предложением по поставкам микроталька с дисперсией D95(2мкм) на рынок западной Европы в количестве от 10тыс.т/год до 60тыс.т/год=6,9т/час, к нам обратился крупнейший тальковый производитель России. У этой компании имеются собственный карьер и мощности для добычи и обогащения тальковой руды 200тыс./год и более. Согласно таблице2 D50(2мкм) и D95(2мкм) соответствуют маркам FINTALK М05N и М01. Компания "ЭТН" обратилась к немецкой компании "NETZSCH-CONDUX", мирового лидера в производстве струйных мельниц типа CGS (рис.3), для приобретения мельниц модели CGS120 стоимостью 700тыс.€=1,04млн.$ (только помольное оборудование, компрессорная установка 625кВт и сепаратора 55кВт). По данным "N-C" при производстве микроталька М05N на мельницах CGS120, затраты энергии составляют 680кВт/час/т., выход продукта М05N до 1т/час и не более 50-60% из сырья, остальные 40-50% тальк низких марок М15, М30 и отходы. При производстве талька М01 на CGS120, согласно данным "N-C" затраты энергии достигают 2200кВт/час/т, а производительность 0,32т/час. С 2004-2009гг было более 350 обращений по вопросам приобретения мельниц МН для производства микро и нанопорошков из различных материалов. К сожалению это в основном компании, желающие купить готовое технологическое оборудование и они готовы ждать выполнение заказа. Несмотря на очевидные достижения и реальные перспективы технологии МН нам пока не удалось окончательно убедить и привлечь инвесторов, чтобы финансировать наш проект. Причин несколько, основная - это сомнения в реализуемости в технических и технологических характеристик оборудования и технологии МН. Россия импортировала в 2008г 12тыс.т микроталька М01($55млн.). Мировой рынок микроталька М01 достигает 1,5млн./т, потребление талька $7-8млрд.(2008г). Спрос на такой микротальк растет и особенно на те марки, где высокое содержание наночастиц. Согласно закону эластичности спроса, если снизить цены до 3000-3500$/т, можно увеличить спрос до 2,5-3,0млн.т ($7,5-10млрд), при средней стоимости тальковой руды в 80-120$/т. |