Причем вариант полного отказа от форм позволяет свести к минимуму и механическую обработку готовых изделий. Действительно, использование вяжущих свойств порошка стекла [13] допускает изготовление заготовок требуемой конфигурации, которые при термообработке увеличиваются в размерах, но сохраняют форму (рис. 4). Потребителем такой продукции может быть гражданское строительство, химическая промышленность и строительство продуктопроводов. Другим результатом развития этого направления мог бы стать выход на рынок облицовочных материалов. На рис. 4 видно, что изделия имеют чистый белый цвет, а при существующем спектре колеровочных добавок можно получать практически любые цвета и оттенки непосредственно в процессе термообработки. Отдельно следует обратить внимание на структуру поверхности получаемого материала. Если срез пеностекла может со временем загрязниться вследствие ячеистой структуры, то поверхность облицовочного материала легко чистится и моется. Перспективным направлением является расширение эксплуатационной ниши пеностекла при увеличении его плотности. В журнале «Строительные материалы» уже сравнивался поризованный кирпич с пустотелым [14]. Было убедительно показано, что с точки зрения строительного материаловедения стеновой штучный материал с кажущейся плотностью ниже 1000 кг/м3 востребован современными строительными технологиями, но занимающий эту нишу пустотелый кирпич экструзионного типа не удовлетворяет строителей по ряду требований. В качестве возможной альтернативы пустотелому кирпичу предлагается поризованный кирпич. Ту же нишу занимают в настоящее время пенобетон различной плотности и природные материалы типа армянского туфа (там, где они есть в наличии). Между тем пеностекло плотностью выше 400 кг/м3 уже достигает требуемых характеристик по прочности и значительно превосходит тот же пустотелый кирпич по теплоизоляционным свойствам. Вопрос стоимости материала и технологии изготовления тоже решаем. Если смотреть на материал и его производство с понимания технологии пеностекла пятидесятилетней давности, то производить такой материал сложно – необходима распиловка каждого блока. А при прочности материала выше 5 МПа и твердости стекла это представляется утопией. Однако использование описанного выше варианта обжига сформованных блоков позволяет отказаться от распиловки. Такая технология позволяет выпускать блоки требуемых размеров без дополнительной механической обработки, а отсутствие форм при обжиге допускает создание высокопроизводительных автоматизированных производств. При этом штучные блоки заданной формы и размеров плотностью 250–1200 кг/м3 уже получены промышленно. Таким образом, можно заключить, что потенциальные возможности использования пеностекла гораздо шире, чем кажутся. В ближайшее время можно ожидать выход пеностеклянных материалов на новые рынки сбыта как территориально, так и функционально. 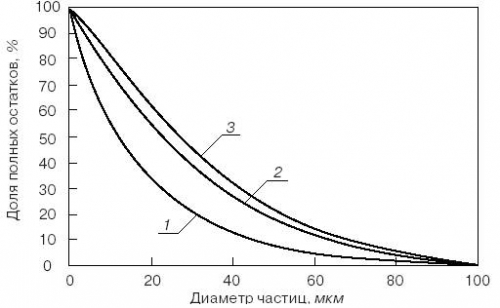
Рис. 3. Дисперсный состав силикатного сырья: 1 – цеолитная порода УстьИлимского месторождения; 2 – кирпичная красная глина Карагайского месторождения; 3 – сырьевое стекло промышленного производства ЗАО «Пеноситал» 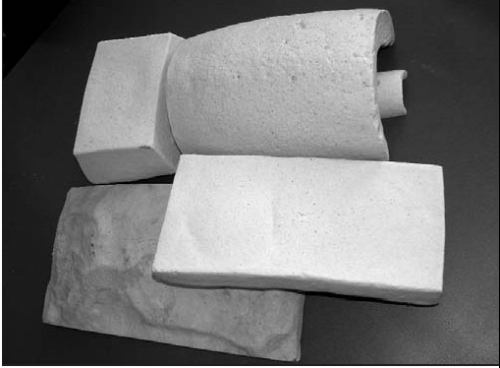
Рис. 4. Фотография блоков пеностекла, полученных без использования жаропрочных форм и без дополнительной механической обработки С анализом российского рынка теплоизоляции Вы можете познакомиться в отчете Академии Конъюнктуры Промышленных Рынков «Рынок теплоизоляционных материалов в России». www.newchemistry.ru |