Технологически достигаемое в вариантах I – III различие приводит к заметному изменению свойств портландитового камня контактно-конденсационного твердения: при средней плотности искусственного портландитового камня 1300–1400 кг/м3 предел прочности при сжатии может лежать в пределах от 4 до 28 МПа, величина водопоглощения через 72 часа составлять 28–31 % и оставаться практически без изменения в течение 28 суток нахождения в воде; коэффициент размягчения (отношение прочности материала в водонасыщенном состоянии к прочности в высушенном до постоянной массы состоянии) при этом может быть от 0,51 до 0,83 (табл. 1). Портландитовый камень, сформированный из монокристаллов Са(ОН)2, имеет по данным электронно-микроскопических исследований плотную упаковку, микропоры оказываются меньше размера частиц. При получении портландитового монолита прессованием наблюдается измельчение кристаллов – размер частиц уменьшается примерно в 1,5–2 раза. Прочный камень формируется не только за счет контактов примыкания, но и контактов срастания кристаллов (рис. 1). 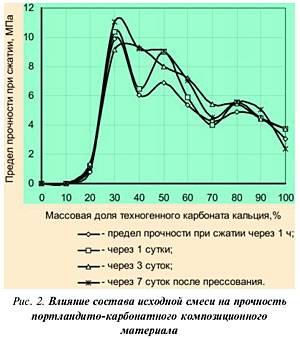
Как определено, материал обладает достаточно высокой водостойкостью. В течение 100 суток нахождения в воде образцы сохраняли прочность и целостность. Это доказывает, что формирование прочного портландитового камня контактно-конденсационного твердения определяется не силами капиллярного стяжения, а силами физико-химической природы. В образцах, хранившихся в течение 5 лет на воздухе, основными в структуре являются кристаллы Са(ОН)2 в виде гексагональных пластин и призм, а также кристаллы вторичного карбоната кальция в виде ромбоэдров. В образцах наряду с контактами примыкания и срастания при электронномикроскопическом исследовании обнаруживаются контакты прорастания. Отмечается повышение средней плотности портландитового камня примерно на 20 % и рост прочности с 25–30 до 45 МПа, то есть в полтора раза. Проведенные исследования и достигнутые результаты позволяют говорить о том, что получаемый по технологии контактно-конденсационного твердения портландитовый камень может рассматриваться в качестве одной из перспективных матричных субстанций для бесклинкерных малоэнергоемких композиционных материалов. Обсуждая возможности использования портландитового камня в качестве матричной субстанции, в первую очередь следует обратиться к портландито-карбонатным системам, в которых наполняющим матрицу материалом могут выступать частицы карбонаткальциевых природных или техногенных продуктов. Основанием для этого являются положения о том, что структурообразующая роль карбонатной составляющей многопланова и затрагивает не только «грубые» физические, но и «тонкие» кристаллохимические механизмы. Известной является роль тонкодисперсных частиц карбонатного материала в качестве возможного микронаполнителя известковых, цементных и силикатных связующих, битумных и полимерных систем. Обладая определенными размерами, твердостью, химическим и минералогическим составом, частицы выступают как микрозаполнитель, образуют пространственный зернистый каркас и создают микробетонную структуру композита. В этом реализуется «физическая» составляющая структурообразующей роли карбонатного компонента. Но одновременно может проявляться и физико-химическая его роль, поскольку частицы могут служить центрами кристаллизации, создавая условия для «зонирования» новообразований при кристаллизации и соответствующей модификации микроструктуры. Наиболее существенным в физико-химической составляющей структурообразующей роли является и действие СаСО3 как «подложки» для ориентированной кристаллизации новообразований на поверхности карбонатных частиц с формированием контактов по механизму эпитаксии. Возможность этого определяется кристаллохимическим сродством параметров элементарной ячейки портландита и кальцита. У портландита параметр элементарной ячейки «с» = 4,909 A близок параметру «а» гексагональной ячейки кальцита (а = 4,969 A), поэтому формирование эпитаксиального контакта срастания возможно здесь при сопряжении плоскости (1120) портландита с плоскостью (100) кальцита. При определенных условиях между частицами дисперсной системы стабильной и метастабильной кристаллической структуры соответственно СаСО3 и Са(ОН)2 возможно формирование контактно-конденсационных связей физико-химического типа. В результате, например, механического сближения частицы СаСО3 могут в принципе срастаться с кристаллами портландита и давать прочный искусственный камень. Рассмотренные положения и явились исходными при организации исследований технологии получения портландито-карбонатных систем твердения контактно-конденсационного типа. Технология предусматривала прессование сырьевой смеси с различными массовыми долями карбонаткальциевого материала и специально полученных индивидуальных кристаллов портландита. В смесь вводилось минимальное количество воды, обеспечивающее необходимые условия прессования бездефектных образцов. 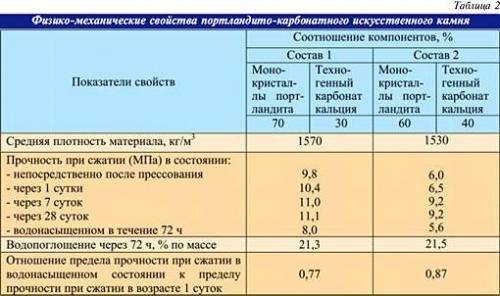
Условия формирования портландито-карбонатной системы твердения рассмотрены на примере техногенного карбоната кальция, образуемого при производстве сложного минерального удобрения нитроаммофоски на Россошанском АО «Минудобрения». По данным наших исследований этот продукт представляет собой дисперсный материал (удельная площадь поверхности 900–1100 см2/г), частицы которой имеют кальцитовую структуру с плотнейшей гексагональной упаковкой; элементарная ячейка имеет форму ромбоэдра, сингония кристаллов кальцита тригональная. Исследованиями установлено, что при реализации технологии прессования принятой смеси возможно достижение твердого состояния непосредственно после формования без какой-либо тепловой обработки (табл. 2). Зависимость прочности искусственного камня от соотношения компонентов в сырьевой смеси имеет максимум прочности при доле СаСО3 в составе смеси 30–35 % (рис. 2). Такая доля частиц карбонатного компонента отвечает условию появления жесткого зернистого каркаса в композите. Методом электронной микроскопии определено, что портландито-карбонатный композит слагается, в основном, из частиц размером около 0,3 мкм; встречаются кристаллические сростки – массивы в виде «друз» с совместными плоскостями кристаллизации портландита и ромбоэдров кальцита. Портландито-карбонатный искусственный камень имеет плотность 1530–1570 кг/м3, влажность по массе 11–12 %; при этом значения предела прочности при сжатии композита достигают 8–12 МПа, что достаточно для определенной номенклатуры и «ниши» штучных строительных изделий – кирпича, перегородочных плит, отделочных плиток и др.
Исследуемые портландитовые и портландито-карбонатные бесцементные системы твердения можно с полным основанием отнести к композициям нового поколения, обеспечивающим определенный прорыв по критериям ресурсосбережения. При оценке достигнутых результатов следует учитывать, что они отвечают только начальной стадии разработки направления. Дальнейшие исследования могут дать более впечатляющие результаты на фоне потенциально эффективных решений мгновенного получения прочного камня без тепловой обработки бесклинкерных составов из доступного и дешевого сырья. C текущей ситуацией и прогнозом развития российского рынка цемента можно познакомиться в отчетах Академии Конъюнктуры Промышленных Рынков «Рынок цемента в России». Е.М. Чернышов, д-р техн. наук, проф., чл.-корр. РААСН; Н.Д. Потамошнева, канд. техн. наук, ст. науч. сотр.; О.Б. Кукина, инженер-химик, аспирант Воронежский государственный архитектурно-строительный университет
|