В зависимости от условий получения и свойств гипсовые вяжущие подразделяются на обжиговые и автоклавные. Обжиговые (низкотемпературные) гипсовые вяжущие получают тепловой обработкой сырья преимущественно при 110—170 °С и атмосферном давлении с отщеплением кристаллизационной воды в парообразном состоянии. Автоклавные гипсовые вяжущие изготовляют тепловой обработкой сырья при 120—150 °С под избыточным давлением 0,13—0,4 МПа. Отщепление кристаллизационной воды из гипса проходит в жидкой фазе. Автоклавная переработка фосфогипса не требует испарения содержащейся в исходном фосфогипсе свободной и кристаллизационной воды. Испарять необходимо только воду, остающуюся после фильтрации продукта автоклавной обработки, т. е. значительно меньше, чем при обжиговых способах переработки фосфогипса. Одним из путей расширения объемов применения гипсовых вяжущих и соответственно объемов утилизации фосфогипса является получение вяжущих, пригодных для изготовления материалов и изделий, продолжительное время стойких во влажных условиях эксплуатации, в т. ч. и при переменном замораживании и оттаивании. К таким изделиям относятся стеновые изделия, смеси для устройства монолитных оснований полов, материалы для тампонирования нефтяных и газовых скважин и др. Использование отходов фосфогипса в производстве изделий строительной индустрии и для получения гипса строительного является одним из перспективных направлений в утилизации наиболее массового вида отходов предприятия. Однако ряд требований к гипсу для строительных материалов ограничивает возможности применения подобного вида отходов. В УкрНИИЭП разработана принципиальная технологическая схема узла кондиционирования фосфогипса (рисунок). 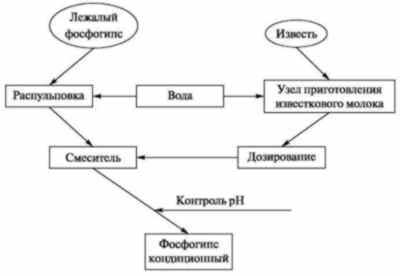 Схема узла кондиционирования фосфогипса
Для кондиционирования отходов лежалого фосфогипса следует применять известковое молоко с концентрацией извести в пересчете на СаО 100 г/дм3, приготовленное из извести строительной (по ГОСТ 9179-77, содержание (на сумму CaO + MgO) — не менее 80%). Количество извести, необходимой для кондиционирования лежалого фосфогипса, невелико — в среднем, исходя из анализов исходного фосфогипса, оно не превышает 0,05 мас. %. Поэтому наиболее перспективным представляется кондиционирование фосфогипса не в виде отдельной стадии, а непосредственно вслед за его образованием, в конце технологической цепочки основного производства. Возможно также осуществление двух параллельных путей кондиционирования — при образовании отхода и для переработки лежалого фосфогипса. При нейтрализации или дополнительной обработке этот крупнотоннажный отход может быть применен в различных отраслях народного хозяйства, что позволит уменьшить количество данного отхода, а также снизить его негативное влияние на окружающую среду. В УкрНИИЭП разработано несколько технологических схем переработки лежалого фосфогипса для производства стеновых панелей, сухих гипсовых строительных смесей, гипсовых вяжущих. Проектная мощность производства разработанных процессов составляет 10—20 тыс. м3/год, срок окупаемости — 2—3 года. Изученные физико-химические свойства фосфогипса и разработанные аппаратурно-технологические схемы позволили оценить возможность применения этого отхода производства для получения строительных изделий, что, в свою очередь, поможет решить проблему крупнотоннажных отходов на предприятиях. Как видно из приведенных данных, свойства фосфогипса не позволяют непосредственно использовать его для изготовления строительных смесей без дополнительной обработки. Касимов А. М., Леонова О. Е., Украинский научно-исследовательский институт экологических проблем, Харьков, Украина Кононов Ю. А., Государственное управление экологии и природных ресурсов в Луганской обл., Луганск, Украина
|