2. ТЕХНИКО-ТЕХНОЛОГИЧЕСКИЕ ПОКАЗАТЕЛИ ЛИНИИ СОВМЕСТНОЙ УТИЛИЗАЦИИ АП 2.1. Мощность линии и режим работы Технологическая линия функционирует 315 дней в году при трехсменной работе. Фонд рабочего времени оборудования – 7500 часов в год. Мощность технологической линии по переработке АП: 5000 т/год; 16,7 т/сутки; 0,7 т/ч. Мощность технологической линии по переработке шлама ЦБК: 15500 м3/год; 51 м3/сутки; 2,1 м3/ч. Производительность технологической линии по выпуску растворителя: 300 т/год; 0,96 т/сутки; 0,04 т/ч. Производительность технологической линии по выпуску холодных гидроизоляционных мастик: 1500 т/год; 4,8 т/сутки; 0,2 т/ч. Производительность по дизельному топливу: 420 т/год; 1,34 т/сутки; 0,056 т/ч. 2.2. Технологическая схема АП со склада первоначально разрезают на куски с размерами, не превышающими 300 мм по большей стороне, после чего подают в газогенератор. В газогенераторе происходит образование генераторного газа, а оставшийся твердый остаток – шлак, выбрасывается наружу. Газообразная часть продуктов газификации направляется в холодильник, где остывает с выделением смолистого вещества и неконденсирующегося газа. Смола отводится в разгонную колонку, где при Т = 180 0С из нее отбирается, примерно, 18% легкой фракции, которая по составу и свойствам соответствует растворителю «Уайт-спириту». Далее при температуре 340 0С отбирается, около 25% средней фракции, пригодной для использования в качестве дизельного топлива. Тяжелая фракция смолы (приблизительно 57%) направляется в эмульгатор, где смешивается и диспергируется с водно-зольной суспензией. В результате получается эмульсия, которая по составу и свойствам соответствует холодным гидроизоляционным битумным мастикам. Неконденсирующиеся газы из холодильника поступают в камеру сгорания, где сжигаются. Продукты сгорания направляются в сушильную камеру. Отходы бумаги первоначально измельчаются, затем замачиваются на 1 сутки, после чего подвергаются варки в течение 3 … 5 ч. Полученная масса пропускается через голлендеры для распушки. Шлам ЦБК отбирается на шламовом поле и насосом перекачивается на виброобезвоживание, где происходит частичное удаление воды. Далее шлам распределяется по формам, которые направляются в сушильную камеру. В результате сушки получают теплоизоляционный материал в виде плит и скорлуп. 2.3. Материальный баланс 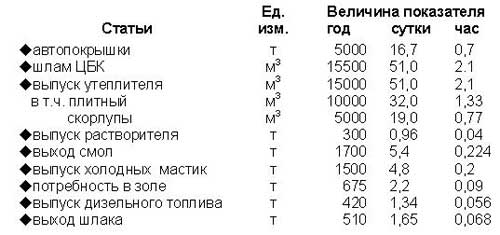
|