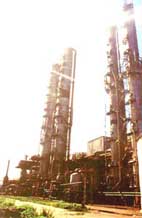
Историческая справка Впервые метанол был найден в древесном спирте в 1661 г., но лишь в 1834 г. был выделен из продуктов сухой перегонки древесины Думасом и Пелиготом. В это же время была установлена его химическая формула. До промышленного освоения каталитического способа метанол получали в основном сухой перегонкой древесины. Метанол, полученный этим способом, был загрязнен ацетоном и другими трудноотделимыми примесями. В настоящее время этот метод получения метанола практически не имеет промышленного значения. Способ, основанный на сухой перегонке древесины, до 1913 года оставался единственным освоенным процессом получения метанола, а в 1913 г. был разработан синтетический способ получения метанола из окиси углерода и водорода на цинк-хромовом катализаторе при давлении 250—350 кГс/см2. Позднее, в 1923 г. этот процесс был осуществлен в Германии в промышленном масштабе и в дальнейшем интенсивно развивался и совершенствовался. История развития отечественного промышленного синтеза метанола началась в 1934 г. на двух небольших агрегатах Новомосковского химического комбината совокупной мощностью около 30 тонн в сутки при давлении 25 МПа на Zn-Cr катализаторе. В соответствии с Директивами XXIV съезда КПСС об ускоренном развитии химической промышленности и расширении ассортимента химической продукции производство метанола росло бурными темпами. Выпуск метанола за указанный период значительно превышал темпы роста производства многих продуктов химической промышленности. Увеличение выпуска метанола проводилось путем интенсификации процесса, за счет расширения существующих и строительства новых производств. Каталитический синтез метанола из оксида углерода и водорода в настоящее время является практически единственным промышленным методом получения метанола, а все используемые в настоящее время процессы отличаются друг от друга вариантами технологических схем, целью которых является достижения максимальной эффективности использования ресурсов. Поиски других способов синтеза метанола продолжаются до сих пор, однако, ощутимых результатов они пока не дали. Одним из таким направлений можно назвать прямое окисление метана, однако, для экономической целесообразности этого процесса, доля метана, превращающегося в метанол, должна превышать по крайней мере 77%. Этот показатель достигался далеко не всегда, и сколь бы то ни было значимого промышленного применения он пока не нашел. Современные технологические тенденции
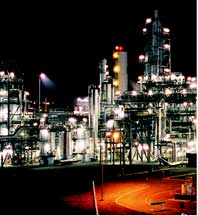 Каталитический синтез метанола из оксида углерода и водорода является единственным промышленно значимым способом получения метанола. В качестве сырья в настоящее время во всех (или почти во всех) случаях выступает природный газ, однако, могли бы использоваться и другие виды водородосодержащего сырья – это коксующийся уголь, отходы нефтепереработки, газы производства ацетилена пиролизом природного газа и др.
Сам процесс производства метанола можно разделить на три этапа. 1. На первом этапе проводится очистка газа от серы. Этот процесс называют гидродесульфуризацией. За ним следует поглощение выделившегося при гидродесульфуризации сероводорода цинковыми поглотителями. Очистка от серы необходима, т.к. сера является ядом для никелевых катализаторов конверсии природного газа. 2. На втором этапе осуществляется конверсия природного газа в синтез-газ (в основном паровая или пароуглекислотная). После охлаждения и конденсации водяных паров газ компримируют. 3. На третьем этапе осуществляется каталитический синтез метанола. Газ на выходе из реактора содержит 3-5% CH3OH, затем газ охлаждают и конденсируют продукты реакции, а оставшийся газ смешивают с исходным газом и направляют снова в реактор. Получаемый метанол-сырец содержит также воду (не более 9% по ТУ 113-05-323-77), этанол, пропанол, бутиловые и амиловые спирты, диметиловый эфир и др. 4. Если метанол-сырец не является товарным продуктом, то его подвергают ректификации, на первом этапе отделяя легколетучие фракции, на втором – от воды и высококипящих элементов. Обычно содержание воды в товарном метаноле не превышает 0,08%. Перечисленные стадии применимы ко всем (почти ко всем) типам производств, и общая схема процесса верна вне зависимости от технологических решений. На рисунке ниже представлена классическая схема производства метанола. Рис. 1. Классическая схема производства метанола 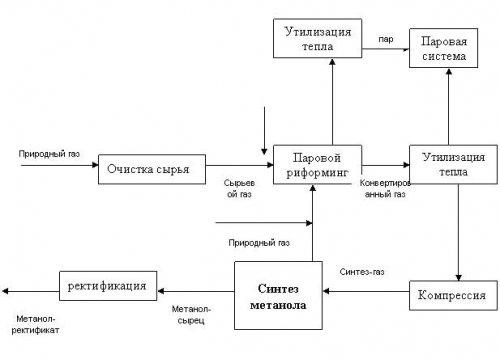
Представленная схема является классической. Рассмотрим технологические решения, предлагаемые основными мировыми лицензиаторами метанольных производств. Одной из главных мировых тенденций в производстве метанола является переход на мега-установки, которые в большом количестве стали строится в период 1990-2006 гг. За это время на Ближнем Востоке и в Латинской Америке появились 22 новых завода, суммарной мощностью почти 20 млн. тонн метанола в год. Мощность установок увеличилась с 1500 тонн в сутки до 5000 тонн. Одним из примеров такого рода производств служит завод в Тринидаде, построенный One Synergy Alliance (Johnson Matthey Catalysts and Davy Process Technology). На заводе действует установка М5000 и используется традиционный паровой риформинг метана. Метод повышения производительности установки парового риформинга без увеличения ее размеров заключается в использовании установки пред-риформинга. Это хорошо отработанная технология, впервые примененная компанией British Gas под названием процесса «Каталитического обогащения газа» при производстве бытового газа из лигроина в 1960-х гг. В компании Toyo Engineering создали схему «TAS –R», позволяющую увеличить силу реакции парового риформинга в адиабатических условиях с помощью разделения пред-риформера на два реактора и возврата технологического газа в конвекционную зону установки для промежуточного дополнительного нагревания (Рис.2). Рис. 2. Схема синтеза метанола «TAS –R», разработанная Toyo Engineering 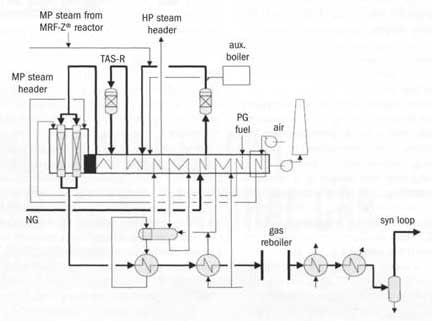
Из-за очень большого размера традиционных установок парового риформинга, на мега-заводах были предприняты попытки найти им альтернативу. Компания One Synergy предложила альтернативную установку, известную как «Compact Reformer» («Компактный Риформер»), в которой теплота сгорания подается к каталитической трубе конвекцией, а не излучением. Она представляет собой вертикальный теплообменник, установленный на верху камеры сгорания. Некоторые лицензиаторы предлагают автотермический риформинг, в котором теплота обеспечивается за счет сгорания части технологического газа в адиабатическом реакторе вместо внешнего сжигания. АТР может действовать при более высоком давлении, чем обычная печь, что позволяет экономить на необходимости компрессии на следующих этапах процесса. Рис. 3. Схема синтеза метанола на основе автотермического риформинга, разработанная Topsøe 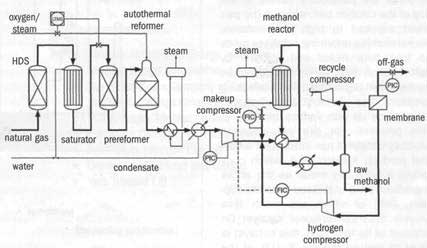 На рис.3 показан процесс производства метанола по Haldor Topsøe на основе АТР. В этой технологической схеме также используется пред-риформер. Процесс включает в себя следующие основные этапы: поступающий природный газ десульфурируется и насыщается паром. Затем технологический газ подвергается пред-риформингу и повторному нагреванию до 650ºС в печи прямого нагрева. Эта температура имеет большое значение, т.к. если подать технологический газ в установку АТР при более низкой температуре, потребление кислорода (около 0,6 т на 1 т метанола) увеличится. В установке АТР газ вступает в реакцию с паром и кислородом, в результате чего образуется крайне реактивный синтез-газ. На рис. 4 представлена схема комбинированного риформинга, предложенный Lurgi.
Рис. 4. Схема комбинированного риформинга (Lurgi) 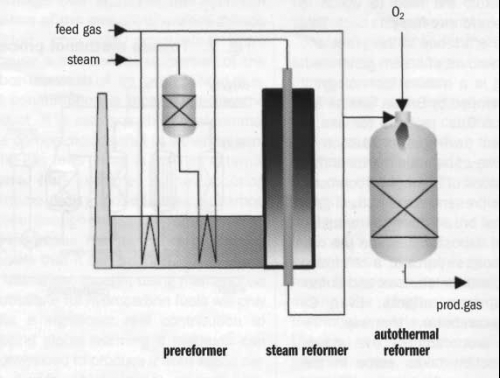 Модернизация реакторного блока также позволяет существенно увеличить производительность завода. В 1970-х гг. были популярны осевые реакторы. Современные реакторы, такие как ARC, разработанный Casale в сотрудничестве с ICI (ныне Johnson Matthey), а также реактор CMD, разработанный Haldor Topsøe, являются оптимизированными многослойными охлаждающими осевыми моделями, созданными для модернизации реакторами первых поколений. Существуют различные варианты реакторов такого типа. На рис. 5 представлен реактор MRF-Z (Toyo). В данном случае синтез-газ проникает через верхнюю часть реактора и проходит сквозь решетки вертикальных байонетных водных труб к центральной коллекторной трубе, выходя из сосуда через нижнее отверстие. Как и у всех центробежных реакторов, перепад давления очень низок. Использование байонетных труб позволяет избежать проблем, вызываемых тепловым напряжением, а также делает возможным свободный сток. Осмотр труб в процессе эксплуатации также несложен, поскольку внутренняя труба может выниматься из реактора. Мощность преобразователя MRF-Z можно увеличивать до очень больших величин (до 10 000 т/день) простым увеличением его высоты. Правда, естественная циркуляция питающей котел воды невозможна при таких масштабах, поэтому придется использовать циркуляционные насосы.
Рис. 5. Реактор синтеза метанола MRF-Z, разработанный Toyo 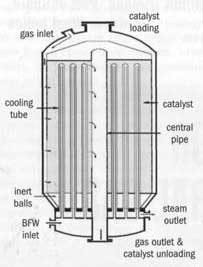 В реакторе Lurgi с водяным охлаждением катализатор находится внутри труб, а вода – в межтрубном пространстве. Температура процесса контролируется регулировкой давления пара. Для очень крупных заводов компания Lurgi предусмотрела последовательное соединение реактора с водяным охлаждением и газоохлаждаемого реактора (Рис.1.5). Газ подогревается в газоохлаждаемом реакторе, а затем проходит в реактор с водяным охлаждением, где и происходит реакция. Нагретый технологический газ возвращается затем в реактор, охлаждаемый газом, где реакция заканчивается при менее интенсивных условиях.
Рис. 6. Каскадная система реакторов для мега-установок (Lurgi) 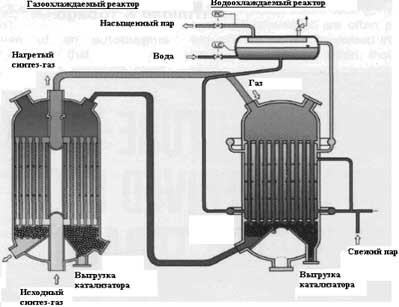
Компания Methanol Casale, заключившая альянс с известной компанией по конструированию печей для риформинга Foster Wheeler, в начале нынешнего десятилетия представила свой реактор с водяным охлаждением. Коммерческий выпуск идет с 2002 г. Данный реактор отличается от других расположенными по радиусу вместо труб вертикальными пластинами – элементами теплообменника, призванных обеспечивать охлаждение (Рис.6). Сообщается, что такое устройство более эффективно и компактно, чем трубное охлаждение, сокращает количество катализатора и, следовательно, размер реактора, необходимого для достижения заданной производительности. Casale продолжили работу над данным типом реактора и недавно выпустили еще два изотермических реактора, доклад о которых будет зачитан на конференции Nitrogen & Syngas 2007 в Бахрейне в конце февраля. Разработчики технологических схем синтеза метанола, применяемых в СНГ Институт «Химтехнология», г. Северодонецк, Украина Государственный научно-исследовательский и проектный институт химических технологий («Химтехнология») является комплексной организацией, включающей научно-исследовательское, проектное подразделения и опытный завод. Свою деятельность институт начал в 1950 г. как филиал Государственного научно-исследовательского и проектного института азотной промышленности (ГИАП). После принятия в 1958 г. постановления правительства о необходимости ускоренного развития химической промышленности и широкого внедрения химической продукции в народное хозяйство страны к 1967 г. он стал крупной комплексной организацией, работающей в области азотных удобрений и производств органического синтеза. В 1981 году институт стал самостоятельной организацией, а в настоящее время входит в холдинг «АЛВИГО». По проектам Института «Химтехнология» построены производства метанола: - на цинк-хромовых катализаторах под давлением синтеза 32 МПа г.Северодонецк (Украина), г.Новочеркасск (Россия), г.Новгород (Россия), г.Ионава (Литва) - на медьсодержащих катализаторах под давлением синтеза 5 МПа мощностью 100 тыс. тонн в год г.Северодонецк (Украина), г.Щекино (Россия), г.Новомосковск (Россия), г.Невинномысск (Россия) и 40 тыс тонн в год г.Харбин (Китай). Институт «Химтехнология» выполнял базовый и детальный проект на строительные работы, надзор за строительством и монтажом агрегатов мощностью 750 тыс. тонн в год в городах Томск и Губаха (Россия) по проекту ICI. Институт «Химтехнология» Выполняет разработку проектов реконструкции действующих производств метанола с целью снижения энергопотребления г.Ионава (Литва), г.Щекино (Россия), г.Новочеркасск (Россия). Также разработаны проекты производства метанола: - М-400 – мощностью 400 тыс. тонн в год. - КТЛМ-2500 – мощностью 825 тыс. тонн в год. Также разработана технология двустадийного синтеза метанола, которая при реконструкции действующих производств позволяет увеличить мощность производства почти в 1,5 раза и снижает энергопотребление на 15-20%. Кроме того, разработана совместная технология получения диметилового эфира (ДМЭ) с метанолом. В настоящее время она проходит опытную проверку. Такая технология сейчас особенно актуальна, так как ДМЭ сейчас всерьез рассматривается как альтернатива дизельному топливу. Более того, принятая Правительством Москвы программа предусматривает внедрение ДМЭ для автотранспорта Москвы к 2010 году, подразумевающая строительство производств ДМЭ. Однако на начальном этапе ДМЭ целесообразно получать на реконструированных установках синтеза метанола. Адрес: Украина, Луганская обл., г. Северодонецк, ул. Дзержинского, дом 1, тел.: (06452) 23357, 23168, 34220, факс: (06452) 25367 Johnson Matthey (ICI) Процессы синтеза метанола, разработанные в свое время компанией Synetix, одним из подразделений компании ICI, которое в 2002 году приобрела компания Johnson Matthey, в мире являются наиболее распространенными. Их технология синтеза метанола при низком давлении (Low Pressure Methanol) используется более чем на 60% мировых производств (По данным компании Johnson Matthey Catalysts). По ее проектам было осуществлено строительство производств в Томске (1983 год) и Губахе (1984 год), где сейчас используются катализаторы этой компании. География размещения производств, где используются процессы синтеза компании ICI (в 1998 году) представлены на нижеследующем схематическом рисунке (по данным самой компании) 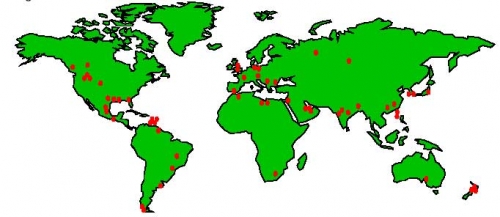
Помимо разработки технологических процессов компания Johnson Matthey Catalysts производит катализаторы для всех типов синтеза. Представительство в Москве: 109012, ул. Ильинка, дом 3/8, стр. 5, оф. 301, тел.: (495) 101 2100, факс: (495) 101 2113
Methanol Casale 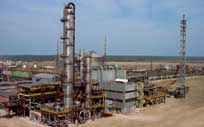 Компания образована в 1994 году и входит в группу компаний Casale. Штаб-квартира группы расположена в Швейцарии, а представительства компании расположены в 14 странах мира, в том числе и в России. Основная специализация компании – повышение эффективности (увеличение мощности и снижение потребления синтез-газа) имеющихся реакторов синтеза метанола и строительство новых. В сотрудничестве со специалистами компании ICI, таким образом, была проведена модернизация нескольких производств, в т.ч. на ОАО «Тольяттиазот». Также в сотрудничестве с Methanol Casale была проведена реконструкция цеха метанола на Невинномысском Азоте. Одним из последних достижений компании является разработка технологии конверсии производств аммиака для производства метанола или одновременного выпуска аммиака и метанола.
Адрес представительства в Москве: 107031, Звонарский пер., дом 1, стр. 5, тел.: (495) 928 8353, факс: (495) 209 6409. C текущей ситуацией и прогнозом развития российского рынка метанола можно познакомиться в отчете Академии Конъюнктуры Промышленных Рынков «Рынок метанола в России».
Об авторе: Академия Конъюнктуры Промышленных Рынков оказывает три вида услуг, связанных с анализом рынков, технологий и проектов в промышленных отраслях - проведение маркетинговых исследований, разработка ТЭО и бизнес-планов инвестиционных проектов. • Маркетинговые исследования • Технико-экономическое обоснование • Бизнес-планирование
Академия Конъюнктуры Промышленных Рынков Тел.: (495) 918-13-12, (495) 911-58-70 E-mail: mail@akpr.ru WWW: www.akpr.ru |