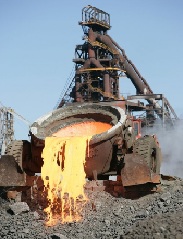
Твердые отходы, которые образуются при использовании металлургических технологий обогащения и рафинирования, называются «шлаком». Они состоят преимущественно из оксидов и силикатов магния, кальция, алюминия, железа и т. д. Шлаки, которые образуются при реализации технологий производства железа и стали, могут, в самом общем виде, подразделяться на три категории: • Доменный шлак (BFS), образующийся при производстве чугуна или доменного чугуна в доменной печи. • Стальной шлак, получаемый из кислородных конвертеров (BOF) и электродуговых печей (EAF). • Ковшовый рафинировочный шлак, образующийся при использовании технологий рафинирования стали в ковшах. Доменный шлак после гранулирования и размалывания широко используется при производстве цемента и бетона. Стальному шлаку, напротив, еще предстоит найти применение с добавленной стоимостью помимо его нерегулярного использования в качестве цементирующего вяжущего вещества. Чаще всего он используется как материал для захоронения отходов. В этой связи предшествующая работа была, по большей части, сконцентрирована на поиске и использовании потенциальных преимуществ стального шлака как материала с ресурсным потенциалом.1 Производство готовой стали увеличилось в Индии с 15.2 метрической тонны в 1993-94 гг. до 36.9 метрической тонны в 2003-2004 гг., то есть был зафиксирован рост на 9%. Объем производства нерафинированной стали за первые восемь месяцев 2006 г. составлял 28 метрических тонн. Индия теперь занимает седьмое место в мире среди крупнейших производителей стали, она несколько опережает Украину и догоняет Южную Корею.2 Примерно 41% готовой стальной продукции приходится на долю интегрированных сталелитейных предприятий, а 59% производства приходится на сталь ограниченного применения. На долю BOF и EAF приходится 55% и 39% от общего объема производства нерафинированной стали соответственно, а оставшиеся 6% приходятся на долю устаревшей технологии обработки в мартеновской печи (OHF).3 В центре внимания в данной работе находится использование стального шлака для применений помимо материала-заполнителя. Здесь предпринимается попытка характеристики физико-химических и минералогических свойств шлака до и после тепловой обработки с тем, чтобы оценить его потенциал для использования в качестве цементирующего вяжущего вещества, а также в качестве заменителя песка в строительных цементных растворах. Материалы и методы Стальной шлак поступал с электродуговой печи компании M/S. Ispat Industries Ltd, которая расположена в окрестностях Мумбаи (Бомбея) в Западной Индии. Интегрированное сталелитейное предприятие производительностью в три метрических тонны производит как доменный, так и стальной шлак. Доменный шлак после гранулирования потребляется находящимся поблизости предприятием Indorama Cement Ltd для производства портлендского шлакового цемента и GGBFS, соответствующего BS-6699. Стальной шлак после измельчения частично перерабатывается агломерационной установкой. Хотя эта установка работает на основе управления отходами с нулевым остатком, для остающегося количества стального шлака все еще предстоит найти какое-либо полезное применение. Методы Для создания характеристики шлака использовались следующие аналитические инструменты: • Рентгеновская флюоресценция (XRF) и рентгеновская дифракция (XRD) для элементного и фазового состава. • Сканирующая электронная микроскопия (SEM), энергодисперсионный рентгеновский анализ (EDXA) и оптическая микроскопия для морфологического и микроструктурного анализа. Испытание на размалываемость проводилось на размоле связывающего вещества. Небольшое количество образца, который в крупнозернистой фракции обычно обогащается, собрали и исследовали с точки зрения фазового состава. Удельный вес образцов определялся с помощью пикнометра с использованием керосиновой среды и гелиевого пикнометра. Одной из называемых причин плохой способности шлака из электродуговых печей к затвердеванию под воздействием воды или к пуццолановой реакции, является отсутствие стеклянного компонента. Для того чтобы повысить содержание стеклянного армирующего материала, шлаки из EAF разминались до размера компонентов в 10 мм и подергались плавлению при температуре 1500°C в индукционной электрической печи с внутренней углеродной футеровкой. После гомогенизации расплав быстро охлаждали в воде. Образцы шлака из EAF до и после обработки размалывали в лабораторной шаровой мельнице до получения размера частиц 390 м2кг-1 – 400 м2кг-1 и оценивали их гидравлическое поведение в составе на основе портлендского шлакового цемента для использования в качестве частичного заменителя GGBS. Для того чтобы оценить пригодность шлака из EAF для использования в качестве заменителя песка в рецептурах растворов для кладки стен, шлак разламывали в роторной дробилке с вертикальным валом (VSI) для получения нужных размеров фракций песка. Измельченный материал отливали в форме призм с размерами 25 мм x 25 мм x 282 мм, которые состояли из одной части цемента и трех частей раздробленного песка EAF. После отверждения призмы испытывали на автоклавное расширение и расширение Ле Шателье в соответствии с нормативами Индийского бюро стандартов (BIS).4 Предел прочности при сжатии раствора был испытан на 50-мм кубах в соответствии со стандартной практикой.5 В качестве контрольного образца использовался обыкновенный песок вместо шлака из EAF для всех испытаний. Результаты и обсуждение Химический анализ Химический анализ шлака из EAF дан в таблице 1. Шлак демонстрирует увеличение массы, превышающее значение, которое можно объяснить присутствием серы, что указывает на наличие самородного железа. Железо присутствует и при двух-, и при трехвалентном насыщении окислением. По сравнению с некоторыми европейскими стальными шлаками, о которых сообщалось в более ранних работах6-8, шлак из EAF, рассмотренный а данной работе, содержит больше алюминия и количество свободной извести, которым можно пренебречь. таблица 1 – Химический состав шлака из EAF Оксиды | Масса (%) | SiO2 | 18.2 | Al2O3 | 9.80 | Fe2O3 | 29.7 | CaO | 30.8 | MgO | 8.50 | TiO2 | 0.85 | MnO | 0.60 | P2O5 | 0.67 | S | 0.05 | Увеличение при возгорании | 2.10 | таблица 2 – Классификация стального шлака на основе щелочности и минералогии Способность к затвердеванию под воздействием воды | Группа | Щёлочность | | | CaO SiO2 | CaO (SiO2 + P2O5) | Низкая | оливин | 0.9 - 1.5 | 0.9 - 1.4 | | мервинит | 1.5 - 2.7 | 1.4 - 1.6 | Средняя | двухкальциевый силикат | | 1.6 - 2.4 | Высокая | трехкальциевый силикат | >2.7 | >2.4 | Показатель щелочности шлака, рассчитанный на основе CaO/SiO2 и CaO/(SiO2+P2О5) составляет 1.85 и 1.78 соответственно. Взаимоотношения между щелочностью, фазовым составом и гидравлической активностью стального шлака по данным источников, представлены в таблице 2. Соответственно шлак из EAF, рассмотренный в данном исследовании, относится либо к группе мервинита с низкой реактивностью, либо к области между группой мервинита – двухкальциевого силиката с активностью от низкой до средней. Минералогический анализ Минералогический состав композитного шлака из EAF (а также более трудно поддающейся перемалыванию фракции, полученной при размоле связующего вещества) был проанализирован с помощью XRD (Рисунок 1). Анализ шлака показал присутствие вюстита (FeO), за которым следуют магнезиоферрит (MgFe2O4), геленит (Ca2Al(AlSi)2O7), монтичеллит (CaMgSiO4) и ларнит (Ca2SiO4). Более трудно поддающаяся размалыванию фракция шлака из EAF содержит больше вюстита, но мало ларнита и геленита. Рисунок 1 - XRD шлакового композита из EAF 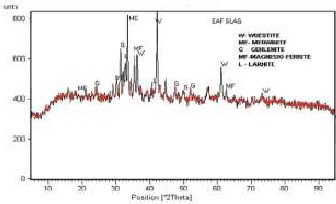 Физические параметры Удельный вес шлака, который определяется с помощью гелиевого пикнометра, составляет 3.72 по сравнению со значением 3.65, определенным методом пикрометрии с использованием керосина. Индекс связывания шлака составляет 27 кТу-1, т. е. несколько менее значений 29-30 кТу-1, имеющихся у стальных шлаков LD индийского происхождения.10 Свойства шлака из EAF с быстрым охлаждением расплава Изменение концентрации неорганических оксидов до и после обработки показано на Рисунке 2. Фазовый состав по результатам XRD показан на Рисунке 3. Из результата XRD видно, что обработка образца быстрым охлаждением расплава в печи с графитовой футеровкой не дает никакого увеличения стеклянной фазы. Сообщается, что при аналогичной обработке золы-уноса получается концентрация стекла более 95% с сильно улучшенными зольно-пыльными свойствами.11 Тем не менее, исследуемый в настоящей статье шлак из EAF имеет более высокую степень кристалличности по сравнению с необработанным шлаком. Имеется заметное снижение содержания оксида железа а образцах обработанного шлака с сопутствующим повышением содержания CaO и SiO2. Такое снижение может объясняться тем, что в ходе плавления часть железа выделяется в виде ячеистой массы, и, как правило, оседает на дне и боковых стенках футерованной графитом печи. Эту часть физически отделяют от остального материала перед проведением анализа. Фазовый состав показывает увеличение содержания мервинита и ларнита и уменьшение вюститовой фазы. Рисунок 2 – Изменение основных оксидов шлака из EAF до и после обработки с быстрым охлаждением расплава. Рисунок 3 - XRD шлака из EAF после обработки с быстрым охлаждением расплава.  Удельная масса шлака составляет 3.5, что незначительно превышает значение для соответствующего необработанного шлака из EAF. Шлак пористый, и легко поддается размолу. В условиях таких же концентраций при размоле на лабораторной шаровой мельнице для получения на обработанном шлаке тонкости измельчения 400 м2кг-1 требуется в два раза меньше времени, чем при работе с необработанным шлаком из EAF. Микроструктура Микроструктура шлака из EAF до и после обработки дана на Рисунке 4. В шлаке из EAF обнаруживается преобладающее присутствие вюстита с высокой отражающей способностью, а также магнезиоферрита и силикатов. Образца расплава с быстрым охлаждением имеют типичную древовидную структуру с более мелкими кристаллами мервинита и ларнита с прекрасной ориентацией. Вюстит содержится в меньшем количестве, зачастую, в виде фазы внедрения в матрице. Аналогичное исследование, проведенное на индийским стальных шлаках, в которых участвовал автор данной статьи, не обнаружило такого уменьшения содержания железа или какого-либо иного изменения фазового состава10. В этом исследовании эксперимент с быстрым охлаждением расплава производился в лабораторном масштабе с использованием платинового тигеля и оксидной керамической футеровки. В микроструктурах, тем не менее, были выявлены существенные отличия, аналогичные тем, о которых уже говорилось в настоящей статье (Рисунок 5). |