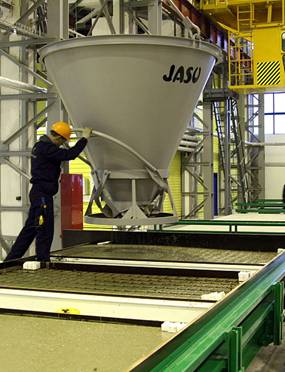
В связи с этим, цель данного сообщения заключается в обсуждении вариантов перевооружения цементной промышленности России, направленных на экономию топливноэнергетических ресурсов, повышение единичной мощности агрегата и автоматизацию производства. В современной мировой практике распространены технологические схемы, приведенные на рис. 1 (варианты I…IV). Рассмотрим преимущества и недостатки каждого варианта на основании анализа теплотехнических показателей различных тепловых систем (табл. 1, 2). 2. Мокрый способ производства В настоящее время мокрый способ реализован в двух вариантах: 1) с длинными вращающимися печами и цепными теплообменниками; 2) с короткими вращающимися печами и молотковой мельницей-сушилкой (дробилкой-сушилкой***). Сравним показатели работы этих технологических схем. 2.1. Длинные вращающиеся печи мокрого способа (вариант I) Основное преимущество этого варианта заключается в простоте технологической схемы и некотором улучшении качества клинкера и экологии. По всем остальным параметрам она явно неконкурентоспособна по сравнению с другими схемами (табл. 1). Основной недостаток – это высокий расход топлива и пониженная производительность печи. Как показано на рис. 2, для данного способа расчетные размеры печи производительностью 5 тыс.т/сутки выходят за разумные пределы, и поэтому рациональная мощность составляет только 1750 т/сутки, т. е. в 3…4 раз ниже, чем для остальных способов. Естественно, это приводит к низкой выработке цемента на одного рабочего, которая ориентировочно в 5 раз ниже, чем для других вариантов. Расход огнеупоров по зоне спекания выше в 10 раз. В связи с Киотским соглашением важное значение имеет также повышенный выброс СО2 в атмосферу. 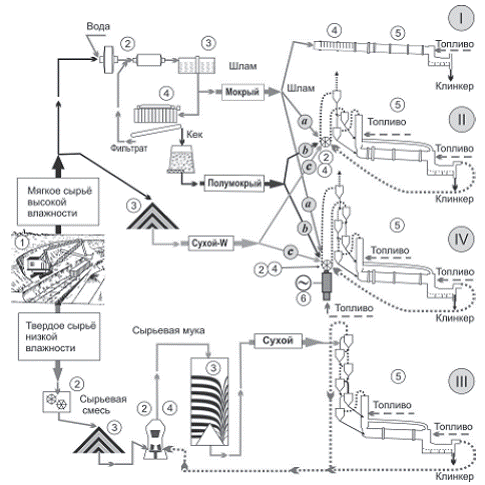
Рис. 1. Принципиальные технологические схемы различных способов производства клинкера (I…IV): 1-добыча сырья, 2-измельчение, 3-смешение, 4-обезвоживание, 5-обжиг, 6-электрогазотурбинная установка (топка) Таблица 1. Достигнутые показатели различных способов производства цемента 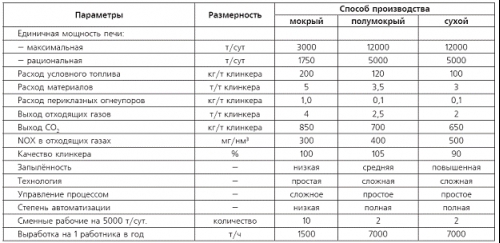
Помимо этих недостатков следует еще особо подчеркнуть несовершенство тепло- технического характера, связанное с тем, что в наименее теплопотребляемую зону спекания подается все топливо (рис. 3). Так, затраты тепла в подготовительных зонах I и II равны 90%, тогда как в зоне горения топлива – всего 10%. Этот теплотехнический «парадокс» приводит к следующим серьезным технологическим затруднениям: 1) пониженной стойкости футеровки в зоне спекания; 2) сложности управления печью; 3) отсутствию надежной системы автоматизации. 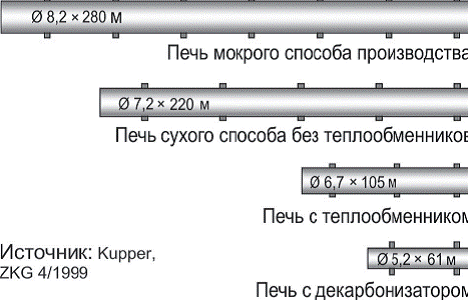
|