Процессы теплопереноса, потери давления, профили скорости, замеры скорости частиц, поведение потока и процессы испарения изучаются при помощи CFD-моделирования. Программы моделирования CFD развились в мощный инструмент анализа и оптимизации работы технологических компонентов промышленного предприятия.
Сегодня процессы развития должны быть эффективными и экономичными. Эффективное компьютерное моделирование является альтернативой дорогостоящему традиционному процессу, включающему фазу конструкторской разработки, изготовление прототипа и экспериментальную оценку (проводимую в несколько циклов). Моделирование CFD основано на методах цифровой гидромеханики, суть которых – в решении задач гидромеханики приближенным применением цифровых методик. Используемые модели строились на основе уравнений Навье-Стокса, Эйлера и уравнения потенциалов. В компании Intensiv-Filter, оптимизация работы рукавных фильтров и других компонентов завода была проведена при помощи сетевой 3D CAD системы (SolidWorks) и местной программы CFD- моделирования (CFX). В данном случае достигли максимального синергизма на всех этапах процесса. После завершения подготовительного этапа реальный расчет потока выполнялся ночью на высокопроизводительных ПК. В компании Intensiv-Filter типичный процесс оптимизации работы оборудования с использованием CFD- метода выглядит следующим образом: – формирование 3D геометрии (программа SolidWorks), – подготовительный этап. Подготовительный этап: – импорт 3D геометрии, – генерация твердых частиц, проносимых насквозь, оптимизация острых углов и краев, – генерация сетки, – ввод оперативных параметров и свойств материала, – определение потока, – определение граничных условий, – запуск программы, моделирующей поток. Этап, следующий за вычислением: оценка и визуальное представление результатов. Далее следует пример, демонстрирующий интеграцию моделирования потока в процесс инжиниринга и конструкторской разработки, основанный на реальном обеспыливающем оборудовании. 2 Изучение конкретного примера: компания Deuna Zement GmbH, Германия Для удаления пыли из вращающейся печи завода компании Deuna Zement GmbH существующий электрофильтр был переоборудован в рукавный фильтр. Вместе с дальнейшим использованием корпуса старого электростатического пылеуловителя фильтрующая способность была увеличена до 60 м3/м2/ч. Для этого в отличие от обычной модернизации электростатических пылесборников все пространство, наполняемое газом, было заполнено рукавами. Из-за пространственных ограничений можно было ожидать неблагоприятных входных параметров газа, паразитного потока в пылесборную камеру и восходящего потока в пакеты рукавов. Моделирование потока должно было дать информацию о том, какие изменения следует произвести во входной зоне. Преследовалась цель создать равномерный поток, входящий в рукава, путем комбинирования поперечного потока и минимизированного (но не исключенного полностью) восходящего потока. Для этой цели были рассмотрены различные варианты конструкции дефлекторов и радиаторов (рис. 1). 1 Переоборудование электрофильтра в рукавный фильтр: параметры оптимизации конструкции 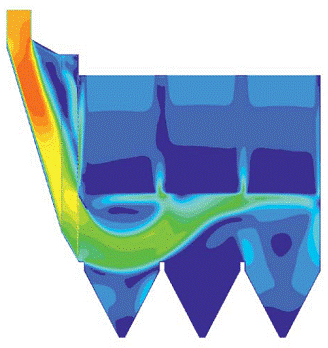
2 Моделирование потока – основной вариант 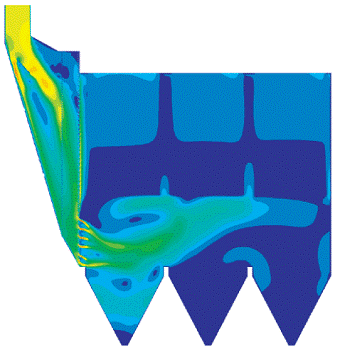
3 Моделирование потока – оптимизированный вариант 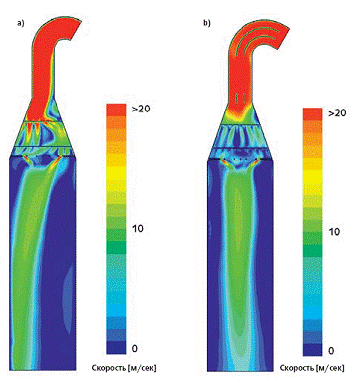
2.1 Результаты Первые результаты моделирования показали (рис. 2), что скорость потока в первом пылесборном бункере достигала приблизительно 10 м/с. После этого установили дефлекторы для достижения более равномерного распределения и снижения максимальной скорости потока. На следующем этапе были оптимизированы входные потоки в фильтрующие элементы с целью снижения скорости во входной и мертвой зонах, где возникали турбулентности и обратные потоки. Соответственно, снижался и уровень повреждений, наносимых рукавам абразивной пылью. Была применена специальная система направляющих радиаторных пластин, разработанных компанией Intensiv-Filter, что привело к желаемой оптимизации поведения входного потока. На завершающем этапе проверили равномерность распределения объемного расхода под пакетами фильтрующих рукавов. Было получено резкое снижение восходящих потоков, циркулирующих вокруг фильтровальных рукавов, а также значительно улучшена ситуация с поперечными потоками. Таким образом, решили задачу оптимальной утилизации фильтровальной поверхности и достигли наилучшей эффективности системы очистки (рис. 3)
|