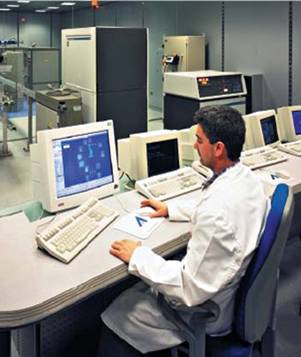
Это происходит не только благодаря хорошо известным поточным анализаторам, установленным поперечно над лентой и на ленте конвейера, но и рентгено-луоресцентным спектрометрам (XRF) и приборам для дифракционного рентгеновского анализа (XRD), объединенным с системой автоматической подготовки образцов. Приборы для оnline и inline анализа не конкурируют друг с другом, поскольку они применяются для исследований на разных стадиях процесса изготовления цемента, когда необходимо анализировать и систематизировать не только химические свойства материала, но и, например, размеры частиц. Некоторые из этих исследований не предполагают отбор материала, а для других это совершенно необходимо. До сих пор исследование материалов в системе управления процессом применялось только при отсыпке усреднительных штабелей сырьевых материалов, на сырьевых и цементных мельницах. Печные системы управления с использованием данных анализа материала используются реже. Введение Методы исследования, которые выполняются в режиме реального времени оnline незаменимы для процессов управления производством на цементных заводах. Однако если измерения температуры, давления, уровней заполнения, величины расхода, мощности моторов и анализ параметров газа проводятся давно, то онлайновые исследования параметров материала для целей управления процессом применяются пока далеко не так часто. Вероятно, это связано с тем фактом, что анализ материала до сих пор считался неотъемлемым компонентом систем обеспечения качества. К тому же исследование материала, которое проводится не в реальном масштабе времени, без сомнения, достаточно сложная процедура, и маршрут, начиная от отбора образцов и их транспортировки по пневматической транспортной системе до устройств по их подготовке и анализу, вплоть до систем приготовления контрольной смеси, очень длинный. Однако существуют многочисленные измерительные inline-методы элементного и фазового анализа входных материалов (сырье и топливо), полупродуктов (сырьевая мука, горячая смесь и цементный клинкер) и различных цементов как конечных продуктов, которые применимы и для контроля производственного процесса. Требования, предъявляемые к результатам такого анализа с точки зрения качества и рентабельности, могут быть удовлетворены только при равномерной и безаварийной работе оборудования с одновременным сбережением ресурсов. Но ресурсосбережение часто вступает в противоречие с задачей повышения качества, поскольку требует применения более дешевых и менее качественных сырьевых материалов и более сложных в обработке вторичных сырьевых материалов. Кроме того, дополнительные требования предъявляет тенденция к расширению производственного ряда различных марок цемента. С другой стороны, анализ материалов в системах управления процессами цементных заводов используется уже более тридцати лет, а начало исследований, проводимых. В режиме реального времени, можно отнести к 1960-м гг. Одним из пионеров в этой области была компания Whitehall Cement, являющаяся сейчас членом группы Lafarge North America, которая использовала рентгеновскую трубку для постоянного мониторинга содержания кальцитов и железа на выходе сырьевой мельницы [1]. Однако своего рассвета аналитические системы достигли в эпоху компьютеров с мощными вычислительными процессорами и развитым программным обеспечением. Стало возможным, например, снизить время проведения классического элементного и фазового анализа с нескольких часов всего до нескольких минут, что дает возможность в лабораторных условиях получить необходимые для системы управления процессом данные. Факт заключается в том, что не существует другой такой темы в цементной промышленности, которой было бы посвящено столько литературы, как анализ материалов в процессе управления и контроля качества. Частично это можно объяснить тем, что существует большое количество поставщиков, но, ни один из них не может обеспечить поставку оборудования для всей технологической цепочки. К тому же создается впечатление, что многие собственники цементных предприятий неадекватно понимают взаимосвязь между анализом материалов, технологическим оборудованием и системой управления предприятием; так, на заводах все еще используются индивидуальные, а во многих случаях и устаревшие решения. Более того, к сожалению, до сих пор нет устоявшихся определений терминов «online», «inline», «atline» и «offline». Следующий далее обзор имеет целью внести некоторую ясность в этот вопрос. Наиболее важные области применения Рис. 1 иллюстрирует комплекс проблем, касающийся подготовки сырьевого материала и связанный с производственным контролем, использующим анализ материалов. Первым шагом является отсыпка усреднительного штабеля для выравнивания отклонений по качеству сырьевого материала, поступившего с карьера. Затем компоненты обычно подаются в сырьевую мельницу, чтобы добиться постоянства цементных модулей с определенными пропорциями извести, диоксида кремния, оксидов алюминия и железа, которые требуются для процесса обжига. Окончательная гомогенизация достигается в силосах для хранения сырьевой муки. 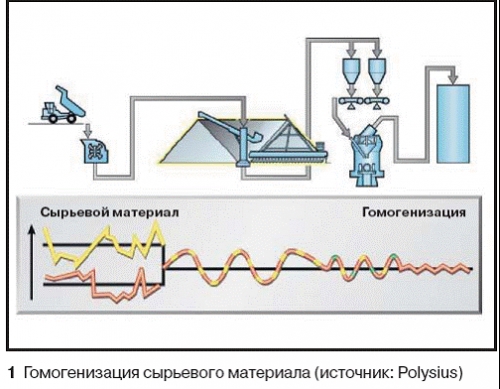
Ясно, что на этапе подготовки сырья уже существует множество различных точек для отбора образцов и замеров, которые могут быть использованы для анализа материала. Более того, и материал в этих предположительных точках отбора образцов отличается не только по сочетанию компонентов, но и по другим параметрам, в частности, по размерам частиц. Нужно также не забывать, что значительные различия в свойствах материала могут быть обусловлены географическим расположением цементного завода. Но, несмотря на эти факты, к анализу материалов в рамках процесса управления выработан адекватный подход. Очередная проблема, которую следует решить, заключается в нахождении оптимальной взаимосвязи анализа материалов и механического оборудования и в выяснении, до какой степени можно использовать анализ материалов в целях минимизации габаритов оборудования, например, усреднительного штабеля и гомогенизационного силоса. На современном цементном заводе обычно задействованы четыре основные цепи управления (рис. 2). Наряду с ними существуют и другие схемы, ведущие к более сложным причинно-следственным связям и таким образом интегрирующиеся в так называемые экспертные системы. Анализы вторичных видов топлива и заменителей клинкера практически никогда не интегрировались в систему управления процессом, но использовались исключительно в целях контроля качества. Таким образом, остаются четыре цепи управления анализом материала, в одной из которых исследуется тонкость помола цемента:
|