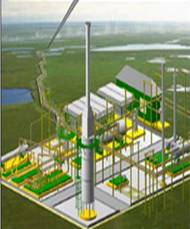
Классические процессы получения синтез-газа, метанола и синтетических моторных топлив каталитическим методом паровой или пароуглекислотной конверсии углеводородных газов за последние 100 лет доведены до высокой степени совершенства. Но технико-экономические расчёты показывают, что создание таких производств экономически обосновано только при производительности 400-500 тысяч тонн метанола в год. При сегодняшних ценах на сырьё, оборудование и энергоносители, а также учитывая тенденцию к непрерывному росту потребности в товарной продукции , граница эта может сместиться к 250-300 тысячам тонн в год. 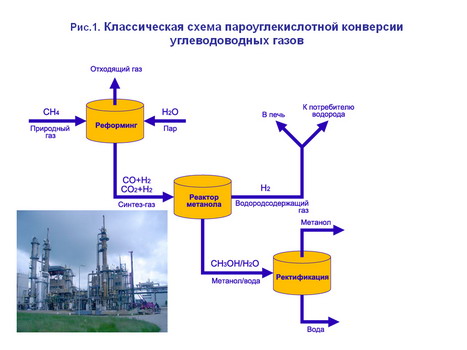
Назвать такое производство "малотоннажным" вряд ли уместно, представить такое производство на нефтепромысле - тем более. Запроектировать, изготовить и построить такую установку в России под силу только крупным компаниям. Учитывая, что сегодня экономическая ситуация в Европе и в США вынуждает нефтехимические компании продавать заводы по производству метанола из природного газа, появляется возможность приобрести часть установок этих заводов, провести их реконструкцию и, адаптировав к условиям конкретного региона России, построить их вблизи магистрального газопровода. Расчеты показывают, что такая схема значительно дешевле, чем инвестирование в новое строительство. Что касается малотоннажных установок GTL-технологий, то их разработано и произведено очень мало, в первую очередь потому, что в СССР в них не было потребности, добыча нефти исчислялась сотнями миллионов тонн, а газа ? сотнями миллиардов кубометров. Сегодня более половины углеводородного сырья в России добывается на малых и средних нефтегазовых месторождениях, и потребность в блочных, мобильных малотоннажных установках по переработке природного и попутного нефтяного газа многократно возросла. Ратификация Россией Киотского протокола, истощение крупных нефтяных и газовых месторождений обострили проблему. Поэтому малотоннажные установки по глубокой переработке углеводородных газов, основанные на GTL-технологиях, являются одним из реальных решений проблемы утилизации низконапорных природных и попутных нефтяных газов. В мировом энергобалансе наибольшая доля приходится на нефть (39%), вторым по значимости в структуре энергопотребления является природный газ (21%). Далее следует каменный уголь (13%), бурый уголь (10%), ядерная энергия (13%), прочие энергоносители (4%) [4]. Попутный нефтяной газ - углеводородный газ, растворенный в нефти и выделяющийся из неё при сепарации, обладающий наиболее ценными компонентами для газохимии. Количество попутных газов, приходящееся на 1тонну добытой нефти, зависит от условий формирования и залегания нефтяных пластов и может колебаться от нескольких десятков до нескольких сотен кубометров. Попутные нефтяные газы (ПНГ) в отличие от природных, состоящих в основном из метана, содержат значительные количества этана, пропана, бутана и других предельных углеводородов. Кроме того, присутствуют пары воды, иногда азот, углекислый газ, сероводород и редкие газы, такие как гелий и аргон. В настоящее время от нефтегазового месторождения до ближайших потребителей - газоперерабатывающих и нефтехимических заводов, доходит в лучшем случае ПНГ первых ступеней сепарации нефти, газ же концевых ступеней сепарации, в котором содержатся наиболее ценные компоненты тяжёлых углеводородов (до 40% С3+В), сгорает на факелах. В результате извлекается не более 25% компонентов С3-С4 от их потенциала в пластовом газе. При сжигании попутного нефтяного газа, горит не только метан - основной компонент углеводородного газа, но и широкая фракция углеводородов: пропан, бутан, гексан и прочие. За год в атмосферу выбрасывается около сотни тысяч тонн вредных веществ - оксидов и диоксидов углерода, азота, углеводородов, сажи. При этом исходные продукты менее вредны для окружающей среды, чем продукты их горения [5]. Сжигание ПНГ, за счёт большого потребления кислорода и теплового излучения, способствует усилению парникового эффекта. Таким образом, проблема рационального использования ПНГ - комплексная: техническая, экологическая, экономическая. Аналогичная проблема в газовой отрасли с остаточным природным низконапорным газом (ННГ) выработанных газовых месторождений, когда по мере разработки месторождения пластовое давление снижается и неизбежно наступает момент необходимости инвестиций в дорогостоящие подготовительные мероприятия, в результате которых добыча газа становится нерентабельной. В целом, под категорию низконапорного сейчас уже попадает (15-20)% извлекаемых запасов газа. Учитывая, что регионы с падающей добычей обладают всей необходимой инфраструктурой, квалифицированным персоналом и социальной сферой, то организация переработки ННГ на месте добычи позволит на долгие годы продлить эксплуатацию этих месторождений, организовать производство ценнейших продуктов, решить социальные задачи занятости населения и развития регионов. Не меньший интерес представляет оживление ныне законсервированных разведочных скважин и других забалансных источников газа с целью его переработки. Стоимость газа на них будет определяться в основном необходимым обустройством и эксплуатационными затратами, так как дорогостоящее бурение уже осуществлено, а в компримировании ещё нет необходимости. Большие перспективы, а зачастую и единственный выход из положения, даёт организованная на месте добычи переработка газа малых месторождений, расположенных вдали от магистральных трубопроводов. Как правило, эти месторождения находятся в собственности небольших компаний, у которых перспектива продажи газа отсутствует, а использование его для энергетических целей весьма ограниченно, так как средняя газотурбинная электростанция мощностью 1Мвт потребляет 0,4 м3 газа на выработку 1 кВт.ч электроэнергии а ресурсы газа даже небольшого месторождения намного больше. Основной продукт конверсии углеводородных газов - метанол (общепринятые названия - метиловый спирт, древесный спирт), является универсальным полупродуктом, имеющим большое практическое применение и служащим сырьем для производства практически всей гаммы нефтехимических продуктов. С этапами изучения химии метанола связаны имена величайших химиков. Впервые метанол был обнаружен ещё в середине XVII века Робертом Бойлем при изучении продуктов перегонки дерева. В чистом виде метиловый спирт был получен только через 200 лет. В 1857 году Марселен Бертло получил метанол омылением хлористого метила. Но процесс сухой перегонки древесины долгое время оставался практически единственным способом производства метанола. Получение метанола из синтез-газа впервые осуществлено в Германии в 1923 году фирмой BASF, в 1927 году в США был реализован промышленный синтез метанола. Метиловый спирт (метанол) в настоящее время находит все более широкое применение во многих отраслях промышленности, в первую очередь, в газохимии. Необходимость борьбы с образованием кристаллогидратов при добыче и транспортировке углеводородов для предотвращения закупорки магистральных газопроводов представляет большую проблему для нефтегазодобывающей промышленности. Согласно оценкам, затраты на эти цели составляют 20% от промысловой себестоимости газа и поглощают 5?8% от всех капитальных затрат в газодобывающей промышленности, так как основным практическим методом предотвращение гидратообразования является использование "термодинамических ингибиторов", главным образом метанола. В относительно недалекой перспективе метанол послужит универсальной основой большинства процессов органического синтеза. Эти процессы могут стать ключевыми в химической промышленности. Поэтому необходимо, чтобы конверсия природного газа и ПНГ в метанол и далее в олефины проводилась на основе эффективных и экологически безопасных процессов. Перспективы использования метанола позволяют прогнозировать многократное увеличение потребностей в нем в самое ближайшее время, так как ведущие страны-производители и потребители моторных топлив рассматривают метанол и метанольно-спиртовые смеси как наиболее перспективные с экономической и экологической точки зрения заменители традиционных моторных топлив нефтяного происхождения.
|