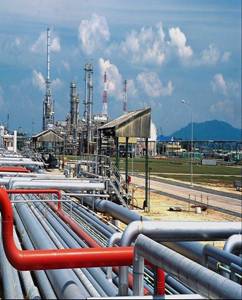
Аварийно¬сти магистральных нефтепроводов по причине внутренней коррозии практически не наблюдается. Это обусловлено тем, что транспортировке подлежит очищенная, обезвоженная и обессоленная нефть. Сеть нефтепромысловых трубопроводов протяженностью более 350 тыс. км включает в себя: • выкидные нефтепроводы от скважин до групповых замерных установок; • нефтепроводы, по которым продукция скважин транспортируется от замерных установок на пункты сепарации; • напорные нефтепроводы, предназначенные для транспортирования подготовленной нефти на центральные пункты подготовки нефти; • водоводы низкого и высокого давления, предназначенные для перекачки отделенной от нефти подтоварной воды до скважин. По данным 2004 г. в России ежедневно происходило 75-80 прорывов нефтепромысловых трубопроводов, из них более 90% этих аварий было связано с внутренней коррозией. Ежегодно на внутрипромысловых трубопроводах происходит до 40 тысяч аварий. По оценкам экспертов, срок службы стальных труб без ПК на нефтепромыслах составляет от 6 месяцев до 5 лет. Потери при добыче и транспортировке нефти в России составляют 3-7% от добываемого объема, что значительно превышает мировые стандарты. Причиной такого положения является высокая коррозионная агрессивность продукции нефтяных месторождений. По трубопроводам нефтяных месторождений транспортируется водонефтегазовая эмульсия, которая представляет собой смесь нефти, подтоварной воды и попутного газа. По мере выработки нефтяного пласта содержание воды в эмульсии увеличивается и может достигать 95%. При движении коррозионно-агрессивных жидкостей возникает общая и локальная коррозия. Если скорость общей коррозии составляет порядка 0,01-0,4 мм/год, то скорость локальной коррозии может достигать 1,5-6 мм/год. Прорывы трубопроводов по причине внутренней коррозии приводят к загрязнению территории и водных ресурсов разлившейся нефтью. В результате концентрация нефтепродуктов в водоемах некоторых густонаселенных городов в 9-15 раз превышает предельно допустимые нормы, экстремальное загрязнение почвы в 150-200 раз превосходит фоновые значения, а десятки тысяч гек¬таров земли уже частично или полностью исключены из хозяйственного оборота. Затраты на ликвидацию последствий коррозионных разрушений составляют до 30% от затрат на добычу нефти и газа. Практически во всех трубопро¬водах, транспортирующих нефть, существует проблема образования асфальто-смоло-парафиновых от¬ложений и солеотложений. Они существенно снижают пропускную способность трубопроводов, увеличивают энергозатраты на перекачку продукта и затрудняют внутритрубную диагностику. В процессе эксплуатации периодически проводится очистка внутренней поверхности трубопроводов от отложений. Указанные проблемы полностью или частично можно решить с помощью внутренних полимерных ПК, ко¬орые в зависимости от назначения условно можно разделить на две группы: гладкостные и антикоррозионно-гладкостные. Гладкостные покрытия на основе эпоксидных материалов предназначены для снижения шероховатости внутренней поверхности трубы и, как следствие, увеличения производительности трубопровода и сни¬жения затрат на транспортировку перекачиваемого не коррозионно-активного продукта. Толщина гладкостных ПК, как правило, составляет 60-150 мкм. История использования гладкостных ПК при транспортировке некоррозионно активных газов насчитывает более 50 лет. Доказано, что затраты на внутренние ПК газопроводов многократно окупаются в процессе эксплуатации. Одним из ключевых факторов, определяющих эффективность гладкостных ПК, является шероховатость поверхности. В таблице представлены показа¬тели шероховатости трубы с ПК и без него. Для максимального гидравличе¬ского эффекта желательна шероховатость поверхности порядка 5-10 мкм. Для получения гладкостных ПК используют ЛКМ, содержащие и не содержащие растворители, ЛКМ с высоким сухим остатком, а также порошковые ЛКМ. В настоящее время в России практически все вновь строящиеся магистральные газопроводы имеют внутреннее гладкостное ПК. К сожалению, в отличие от газопроводов, магистральные нефтепроводы в Рос¬сии эксплуатируются без внутреннего гладкостного ПК. Долгое время считалось, что нефть в силу своей консистенции улучшает характери¬стики потока. Зарубежными специалистами доказана ошибочность этого положения. Ряд статей и проспектов фирмы Е WOOD Limited, Великобритания, показывает преимущества применения гладкостного ПК на не-фтепроводах. К ним относятся: • увеличение пропускной способности трубопровода; • снижение образования парафиновых отложений; снижение энергозатрат насосно-компрессорных станций; • снижение капитальных затрат; • защита от коррозии при хранении труб до монтажа; более эффективная очистка и диагностика; • чистота транспортируемого продукта; • снижение эксплуатационных расходов за счет сохранения работоспособности задвижек. Вычисления, выполненные спе¬циалистами фирмы. Е WOOD Limited, показывают, что для нефтепровода диаметром 660 мм и длиной 200 км применение гладкостного ПК СОРОМ EP2306XF или COPON EP2306HF даст экономический эффект поряд¬ка $1 млн. в год. Имеется опыт при¬менения ПКТК-33 фирмы Tuboscope Vetco, США. Необходимо учесть имеющийся уже сейчас зарубежный опыт по гладкостным ПК нефтепроводов, провести дополнительные исследования, подобрать ЛКМ и организовать в России строительство магистральных нефтепроводов с внутренним ПК. Антикоррозионно-гладкостные покрытия внутренней поверхности нефтепромысловых трубопроводов выполняют сразу несколько функций, обеспечивая: • защиту от коррозионного воздействия эксплуатационных сред; • защиту от гидроабразивного и коррозионно-механического из¬носа; • предотвращение или значительное снижение отложений асфальто-смолопарафинов и солей; • чистоту продуктов при их транспортировке. Критериями выбора ЛКМ для внутренней изоляции труб являются условия эксплуатации трубопровода, защитные и физико-механические свойства ПК, а также технологические свойства ЛКМ. Наиболее подходящими для внутренней изоляции труб по всем параметрам являются ЛКМ на основе эпоксидных, модифицированных эпоксидных и феноло-формальдегидных смол. Из порошковых полимеров широко применяются эпоксидные ЛКМ, нанесенные по грунтовке на основе жидких феноло-формальдегидных смол. Толщина антикоррозионных ПК, как правило, составляет 300-600 мкм. Шероховатость внутренней поверхности труб нефтяного сортамента 
Для антикоррозионных ПК труб могут использоваться традиционные жидкие ЛКМ с высоким сухим остатком и порошковые полимеры. Традиционные ЛКМ с содержанием сухого остатка менее 70% следует наносить в 3-5, а иногда и более, слоев для получения необходимой толщины ПК. Недостатки применения этих материалов очевидны: увеличение трудоемкости процесса, снижение производительности линии внутренней изоляции, возможность повреждения покрытия штангой при нанесении последующих слоев. Применение ЛКМ с высоким сухим остатком позволяет полностью исключить вышеперечисленные недостатки. Кроме того, улучшаются санитарно-гигиенические условия труда, сокращаются невозвратимые потери материала при окраске по сравнению с ЛКМ, содержащими растворители. Использование высоковязких ЛКМ приводит к улучшению экологической обстановки за счет снижения выбросов в атмосферу ле¬тучих органических растворителей. Порошковые полимерные материалы в отличие от жидких ЛКМ, содержащих растворители, технически и экологически более выгодны. Недостатками порошковых полимеров являются необходимость дополнительных энергозатрат за счет формирования ПК при температурах 180-230 'С и их взрывоопасность. |