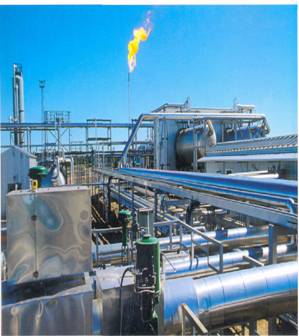
Для коммерческого использова¬ния газа плотность содержащейся в нем энергии должна быть увеличена. Обычно это достигается путем сжа¬тия газа до высоких давления или сто ожижения. Оба эти метода связа¬ны с большими капитальными и ор¬ганизационными затратами. Для осуществления подобных проектов требуется много времени, которое тратится, в частности, на создание устойчивых договоренностей между покупателем и продавцом, необхо¬димых для гарантии жизнеспособ¬ности проекта. Исторически сло-жившаяся сложность монетизации попутного нефтяного газа (ПНГ) приводит к тому, что в удаленных областях, особенно не имеющих выхо¬да к морю, газ выбрасывается в атмосферу или сживется, если это возможно, или закачивается в пласт, если другой возможности нет. Однако с недавнего времени боль¬шие ресурсы попутного нефтяного газа стали представлять большой интерес, поскольку' ценность энергии возросла. Тем не менее, даже сегодня 1я, по оценкам Всемирного банка, все еще сжигается ежегодно около 150 куб. млрд. газа, что приблизительно равно 70% мирового рынка сжижен¬ного нечитаного газа (СНГ) В России объем сжигания ПНГ, по скромным, хотя и неподтвержденным оценкам, составляет от 10 до 30 куб. млрд. в год. При условии превращения этого га¬за и жидкие топлива это составило бы, соответственно, 100 и 300 тыс. барр/день высококачественного топлива или более 4 млн. т в год. Эта ситуация волнует в большей или меньшей степени многие стра¬ны во всем мире. Кроме того, с по¬явлением новых норм, сокращаю¬щих или запрещающих сжигание попутного газа, возникает необхо¬димость принятия решений для вы¬бора метода переработки газов труднодоступных и удаленных мес¬торождений в легко транспортиру-емые и востребованные продукты. Переработка природных газов и метанол, жидкие углеводороды и другие удобные продукты исполь¬зуется в течение многих лет, но применяемые при этом технологии довольно громоздки, чтобы их можно было бы использовать во всех случаях без исключения. Существующие технологии Современная экономичная тех¬нология производства жидкого топлива требует, чтобы природный газ сначала был превращен в син¬тез-газ (смесь водорода и оксида уг¬лерода), а затем эта смесь подвер¬глась конверсии в процессе Фишера-Тропша (ФТ) с образованием синтетических жидких углеводо¬родных продуктов. Существующие процессы получе¬ния синтез-газа являются очень ка¬питалоемкими: они используют большие и тяжелые трубчатые па¬ровые конвертерные печи или тре¬буют наличия кислородных устано¬вок, которые позволили бы приме¬нять парциальное окисление или автотермическую конверсию. Обычные паровые риформеры имеют массивную конструкцию, поскольку должны обеспечивать передачу энергии от горящего топ¬лива в зону реакции через стенку, не допуская при этом попадания пламени па трубки с катализато¬ром. Большие теплообменники позволяют осуществлять оптимальный теплообмен между топливом, воздухом, паром и углеводородами, попадающими в систему с синтез-газом, и отходящими дымовыми газами, покидающими систему. Чтобы обеспечить высокую эффективность процесса, необходимо генериро¬вать пар с высоким давлением и высокой температурой, а это при¬вносит дополнительные проблемы, которые следует решать проекти¬ровщику. Установки, использующие кислород, имеют схожие недостатки, поскольку производство кислорода также является капиталоемким про¬цессом. Кроме того, высокие темпе¬ратуры и давления, применяемые в этом случае, требуют особого внима¬ния, также как и обычное для этих процессов производство пара высо¬кого давления, требующее значи¬тельных капиталовложений. Уста¬новки, использующие кислород, обычно очень большие и могут иметь значительную стоимость. Их сооружение должно осуществляться высококвалифицированным персо¬налом, а это может быть большой проблемой для некоторых удаленных мест, где рабочей силы недоста¬точно, она дорога, и трудные условия работы приводят к низкой произво¬дительности труда. Оценивая недостатки существую¬щих технологий, а также понимая необходимость использования воз¬можностей, предоставляемых по¬путным и трудноизвлекаемым су¬хим газом на материке и на шельфе, компании ВР и DPT начали свои ис¬следования по конверсии газа. Предпосылки Учитывая вышеуказанные слож¬ности, следовало создать новый подход, позволяющий извлекать выгоду от разработки удаленных месторождений посредством ис¬пользования лучших качеств уста¬новок конверсии природного газа, таких как простота и надежность, и в то же время позволяющий повы¬сить их эффективность. Таким образом, возникла идея со¬здания «компактного конвертера». Ее целью была разработка простого модульного противоточного реактора, который обеспечивал бы предварительный подогрев топлива, воздуха, сырья и охлаждение продуктов и отходящих дымовых газов и не требовал бы выработки пара. Такой реактор можно было бы производить на заводе и транспор-тировать на место, при этом его монтаж был бы несложным и мог бы быть осуществлен при исполь¬зовании рабочей силы средней ква¬лификации. Компактный риформер должен демонстрировать высо¬кие показатели процесса при использовании обычного катализато-ра. Целью работы было не только создать процесс конверсии при¬родного газа, который позволял бы получать синтез-газ высокого каче¬ства, не содержащий примесей азо¬та, которые неизбежны при исполь¬зовании окисления воздухом, но также избежать неудобств, связан¬ных с высокой стоимостью и чрез¬вычайной сложностью разделения воздуха, используемого в процессе каталитического окисления. Кроме того, в пашем процессе GTL не должна образовываться вода, по¬скольку вода, синтезируемая в про¬цессе Фишера-Тропша. будет пере¬рабатываться на стадии получения синтез-газа, а не сбрасываться в ес¬тественные водоемы, что требует построения громоздких водоочис-тительных сооружений. Концепция компактного риформера была первоначально провере¬на на однотрубном реакторе с це¬лью изучения научных основ про¬цесса. После того как эта концеп¬ция была подтверждена, была раз¬работана многотрубная пилотная установка. Успешная работа этой установки убедила разработчиков в том, что необходимо построить больший компактный риформер. Была также проведена разработка технологии процесса ФТ. Было ре¬шено создать новый катализатор, поэтому были проведены специ¬альные исследования по его созда¬нию, позволяющие определить на¬илучшую комбинацию активного компонента и носителя. В програм¬ме исследований использовали ми¬крореакторы и другие методики, позволившие разработать патенто¬способный катализатор, способ¬ный работать в реакторах раз¬ных типов. Было произведено тщательное изучение того, какой именно тип реактора следует использовать. Ключевым моментом при этом служила легкость его масштабирования, т.к. целью исследования было достижение большой производительности. Кроме того, учитывалось значительное тепловыделение в процессе ФТ. С учетом этих факторов был выбран простой трубчатый реактор с фик¬сированным слоем катализатора. Соответственно, был построен опытный однотрубный реактор, позволяющий определить количе¬ство катализатора — основной па¬раметр, ответственный за масшта¬бирование. После успеха одно¬трубного реактора были проведе¬ны исследования по увеличению мощности аппарата. Было решено, что технология ФТ готова к даль-нейшему масштабированию. Следующим шагом было строи¬тельство опытного завода, на кото¬ром были бы совмещены компакт¬ный риформер и синтез ФТ с при¬нятыми усовершенствованиями. Компания ВР решила, что завод бу¬дет построен в Nikiski (Аля¬ска), в трех часах пути от Анкориджа. Компании DRT выполнила основное проектирование для всего завода. Услуги по закупкам и строительству были предоставлены подразделением Kvaemer group ныне Aker Solutions. Строительство завода бы¬ло завершено в 2002 г., в том же году он был пущен в строй.
|