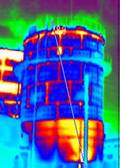
Хотя теории и практике химической энерготехнологии с детальным анализом отдельных производств и процессов в последнее время уделяется большое внимание, методы энергосбережения медленно внедряются в практику промышленных предприятий. Вместе с тем, проблемы энергосбережения и пути их решения имеют достаточно общий характер для предприятий со схожей структурой производств. На предприятиях азотной промышленности, как правило, имеется избыточный пар низких параметров, образующийся в технологических процессах, отработанный низкопотенциальный пар с турбоприводов, потоки конденсата и органических продуктов, имеющих высокую температуру, утилизация тепла которых затруднена из-за невозможности его использования напрямую в технологии. Значительное количество тепла теряется с отходящими дымовыми газами печей риформинга природного газа, при дросселировании пара до технологически необходимых параметров и так далее. В связи с этим представляет интерес рассмотрение некоторых общих подходов при решении проб-лем энергосбережения, не требующих существенного изменения в технологии и больших капитальных вложений. На основании опыта многолетней совместной работы Гродненского ПО"Азот" с ОАО ГИАП (г. Москва), лабораторией термодинамики органических веществ НИИ физико-химических проблем Белгосуниверситета (г.Минск), НПО ЦКТИ (г. С.Петербург) можно выделить следующие, наиболее эффективные с точки зрения сроков окупаемости затрат направления: Наиболее простым и эффективным способом решения проблемы утилизации низкопотенциального пара является повышение его давления до технологически приемлемых параметров с помощью паро-струйных компрессоров, методы расчета ко-торых хорошо разработаны [3]. В результате процесса инжекции за счет энергии пара более высоких параметров повышается давление инжектируемого пара и, кроме того, есть возможность повысить его температуру до необходимого значения, что очень важно в случае, если утилизируемый пар является насыщенным. Этот метод утилизации низкопотенциального пара имеет преимущества перед другими способами ввиду низких капитальных вложений и исключительной простоты конструкции применяемого оборудования, которое может быть изготовлено силами ремонтно-механических цехов предприятий. Нами с применением паро-струйных компрессоров решены проблемы утилизации низко-потенциального пара с турбоприводов компрессоров в аммиачных производствах, избыточного технологического пара в производствах карбамида, реализуются схемы использования тепла горячего конденсата с предварительным получением пара вторичного вскипания, его последующим компремированием и выдачей в заводскую сеть, а также насыщенного низкопотенциального пара от теплоутилизационных установок [4]. Комбинированная выработка электроэнергии и теплоты на теплоэнергетическом оборудовании В энергоемких химических производствах, потребляющих в больших количествах пар, су¬ществует, как правило, развитая система редукционно-охладительных установок (РОУ), редуцирующих пар высокого давления до технологически необходимых параметров, а также для собственных нужд котельной, отопления и так далее с большими теплопотерями. Основной резерв экономии энергоресурсов в данном случае заключается в установке паровых турбин с максимально возможной выработкой электроэнергии, при котором питание основных потребителей пара организовано из отборов турбины, в минимальной степени предусматривая работу РОУ [5]. При этом, расход топлива на выработанный 1 кВт/ч, по сравнению с выработкой электроэнергии по чисто конденсационному циклу, снижается в три раза, а ее себестоимость для условий Гродненского ПО"Азот" ниже цены электроэнергии, потребляемой из сети, в 3-7 раз (в зависимости от места установки турбины). Возможна ситуация, когда с целью максимальной выработки электроэнергии пар низких параметров вырабатывается в большем количестве, чем это необходимо для технологических нужд. В этом случае корректировку баланса необходимых параметров пара возможно осуществлять с помощью паро-струйных компрессоров. Существенным элементом обоснования энергосберегающих технологий является термодинамический анализ процессов действующих производств с выполнением необходимых эксергетических расчетов. Возможности такого подхода при решении задач энергосбережения можно проиллюстрировать на примере комплекса работ, выполненных совместно с лабораторией термодинамики НИИ физико-химических проблем Белгосуниверситета (рук. Г.Я. Кабо), в области технологии производства капролактама. Выполнение эксергетических расчетов и на их базе разработка энергосберегающих технологий особо важно для многостадийных энергоемких производств, каким является производство капролактама, так как проектные решения даже современных производств не всегда базируются на глубоком термодинамическом анализе технологической схемы и при их проектировании больше следуют традициям и требованиям нормативной документации, чем логике энергосбережения. Так, например, не практикуется использование тепла выходящих потоков ректификационных колонн для нагрева исходных продуктов, поступающих на ректификацию, часто не используется тепло, уносимое с продуктами реакции из химических реакторов, и так далее. В результате теплообменных процессов большая часть теплоэнергии, поступающей на производство капролактама с паром, отводится оборотной водой и безвозвратно рассеивается в окружающей атмосфере. Следует отметить, что хотя капролактам и является многотоннажным промышленным продуктом, данные о термодинамических свойствах полупродуктов его синтеза, необходимые для расчетов, немногочислены. В связи с этим были исследованы термодинамические свойства всех промежуточных (циклогексанол, циклогексанон [6,7], циклогексаноноксим [8,9,10], капролактам [11]) и основных побочных (2-циклогексилциклогексанон, 2-циклогексенилцик-логексанон, 2-циклогексилиденциклогексанон [12], циклогексилацетат [13]) продуктов синтеза капролактама. Для определения термодинамических свойств использовались методы исследования равновесия реакций, определения энтальпий сгорания, энтальпий фазовых переходов, измерение теплоемкости веществ в интервале 5-500 К, давления насыщенного пара, методы статистической термодинамики и в сочетании с литературными сведениями создана база термодинамических данных для всех ключевых соединений производства [14,15]. С использованием полученных данных выполнен эксергетический анализ отдельных стадий и определены основные направления снижения энергопотребления, часть из них реализована в производстве.
|