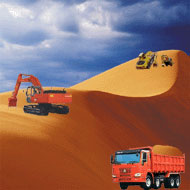
Исходный песок может поступать на производство с влажностью до 12% и содержать в качестве примесей глинистые, пылеватые частицы и крупнозернистые включения. К обогащенному песку предъявляются особые требования. Он должен быть сухим, без посторонних примесей (глинистых, пылеватых), иметь определенный гранулометрический состав и др. Например, для песка, используемого в ССС, необходимо учитывать следующие технологические особенности: • влажность песка - 0,5%; • температура песка - не более 50°С, в противном случае сушилка должна быть обеспечена холодильником для охлаждения песка; • так как при производстве ССС предъявляются весьма жесткие требования к фракционному составу песка, то сушилки необходимо оборудовать системой барабанных сит или использовать вибрационный грохот. Анализ научной, патентной и рекламной информации [1-9] позволяет сделать заключение, что в настоящее время производство сухого обогащенного песка реализуется по двум технологическим схемам, достоинства и недостатки которых мы рассмотрим ниже. • Схема 1 - использование традиционных тепловых агрегатов для сушки и их совмещение с холодильниками и оборудованием по классификации и обогащению сухого песка; • Схема 2 - использование новых установок, на которых можно одновременно сушить, охлаждать и обогащать песок без грохочения и дополнительных пересыпок. Аппаратурное обеспечение технологической схемы 1 состоит из сушильной установки (кипящего слоя, виброкипящего слоя, вращающегося сушильного барабана), теплогенератора с системами подготовки и подачи теплоносителя, охладителя песка, системы обеспыливания и очистки отходящих газов. Для обогащения (классификации) сухого песка используются традиционный вибрационный грохот или системы плоских или барабанных сит. Технологическая схема производства выглядит при этом следующим образом (см. схему 1). Схема 1. Технологическая схема производства сухого обогащенного песка.
Достоинства схемы: сушилки кипящего слоя и - особенно - сушилки виброкипящего слоя обладают достаточно высокой тепловой эффективностью, обеспечивают влагосъем 150-200 кг/м3•час установки. Удельный расход тепла в таких установках - в пределах 5000-6500 кДж на кг испаренной влаги, а установки виброкипящего слоя позволяют достигать удельного расхода тепла в пределах 4000-5000 кДж на кг испаренной влаги, что сопоставимо с затратами тепла в сушильных барабанах. К преимуществам использования сушильного барабана также можно отнести высокую надежность при непрерывной работе с выпуском десятков тонн сухого песка в сутки. Недостатки связаны с большим количеством пересыпок и транспортирующих устройств, необходимостью использования дополнительных агрегатов для охлаждения песка и его классификации, а также с конструктивными и технологическими особенностями сушильных аппаратов, используемых в схеме. Недостатком установок кипящего слоя является повышенный расход электроэнергии, необходимый для создания кипящего слоя при производительностях более 1-2 тонн в час, а также сложность поддержания режима кипения при полифракционном составе песка. То же относится к установкам виброкипящего слоя. Предпочтительными для сушки песка в количестве более 2 тонн в час являются барабанные сушилки, однако объемное напряжение по влаге сушильных барабанов невелико - 50-100 кг/м3•час. Поэтому конструкторские разработки в последнее время направлены на повышение интенсивности сушки за счет использования встроенных насадок и придания материалу водопадного режима движения путем обеспечения скорости вращения барабана, близкой к критической. В этом случае можно достичь влагосъема на уровне 300-500 кг воды с кубического метра барабана в час. Одной из самых распространенных проблем традиционного грохочения, используемого в схеме 1, является проблема забивания сеток. Это приводит к низкой эффективности процесса, неоправданным и очень большим потерям материала в отвалы, низкому качеству конечного продукта. |