Очистка после газификации Все катализаторы парового риформинга, используемые на заводах по производству аммиака, в большей или меньшей степени чувствительны к присутствию серы. Первой стадией почти на каждом таком заводе является стадия гидродесульфирования и улавливания серы. При газификации тяжелого сырья невозможно провести предварительное десульфирование, и сера (чаще всего в виде сероводорода) попадает в блок очистки вместе с сырым синтез-газом. Синтез-газ имеет также высокое содержание угарного газа, который отнимает тепло на стадии очистки. В системах газификации с низким давлением принято удалять кислые газы в два этапа – сероводород перед высокотемпературной стадией очистки, а углекислый газ после. Но в наши дни, согласно докладу фирмы Johnson Matthey Catalysts, существуют катализаторы, которые нечувствительны к сере и способны противостоять большим температурам, возникающим при высоком парциальном давлении диоксида углерода. На современных заводах, где проводят газификацию при высоком давлении, обычно неочищенный синтез-газ пропускают через «кислую» стадию (всего две стадии с промежуточным теплообменником), и потом удаляют кислотные газы в отдельной установке. Эти катализаторы, в качестве активных компонентов содержат кобальт и молибден, а не железо и хром, как это было раньше. Они способны значительно снизить содержание угарного газа в составе синтез-газа, а остатки можно удалить на конечном этапе – промывке жидким азотом. Таким образом, нет необходимости в низкотемпературном этапе очищения и его чувствительном медноцинковом катализаторе. Усовершенствование системы очистки от C02 Большинство заводов по производству аммиака, основанных на процессе парового риформинга используют систему удаления углекислого газа с помощью химической абсорбции. Этот прием является энергозатратным. Больших успехов удалось достигнуть за последние годы в вопросах понижения потребления энергии и усовершенствования химии промывных растворов. Существует два основных типа очистки: алканоламинами и горячим карбонатом калия. Компания Indo Gulf Fertilizers (IGF) предлагает одну из своих последних разработок 1520/2620 t/a. Это разработка Giammarco-Vetrocoke (GV) с двухэтапной системой регенерации (100 и 20 кПа), использующая глицин и диэтаноламин в качестве активаторов. Как было установлено, эта методика позволяет снизить содержание C02 до 0,1%. Компания IGF предложила модифицировать схему для повышения эффективности процесса (синие пунктирные стрелки на рисунке 1). Была встроена маленькая дополнительная испарительная емкость, функционирующая при 30 кПа, и новая тарелка для отбора фракции. Раствор, покидающий колонну низкого давления, передается в главную секцию абсорбера. Пар, образовавшийся при мгновенном испарении, и углекислый газ из испарительной емкости попадают в регенератор высокого давления всего на одну тарелку ниже, а не в самое основание. Поток раствора из регенератора высокого давления в регенератор низкого давления в основном увеличивается с 200 до 350 м³/ч. Раствор со дна колонны высокого давления, становится чище, и через другую испарительную емкость попадает в секцию тонкой очистки C02. Процесс, модифицированный таким образом, позволяет снизить содержание C02 в составе очищенного газа до 0,04%. 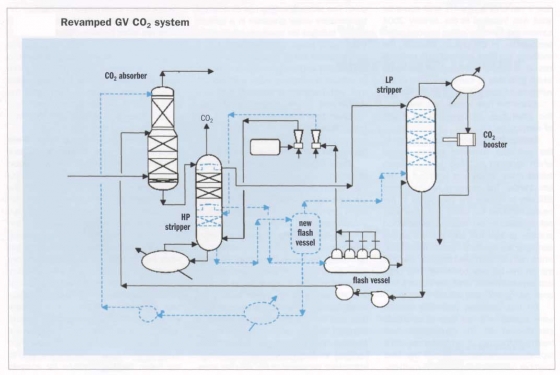 Рис. 1. Модификация схемы очистки от СО2
Очистная колонна Purifier™ Когда фирмы Brown & Root и Kellogg объединились для формирования установки KBR, две прежде конкурирующие технологии производства аммиака были объединены под одной крышей. В последующие годы успешные разработки Braun, формально принадлежащие Brown & Root, были введены в процесс Kellogg, в основном это касалось заключительной стадии на заводе по производству синтез-газа – криогенной очистки в колонне Purifier™. В отличие от схемы, где для очистки используется жидкий азот, получаемый в воздухоразделительной установке, очистная колонна Purifier является автокриогенной системой встроенной в газопровод технологического газа завода синтез-газа. В обычном процессе метонатор используется для превращения остатков окиси и двуокиси углерода в метан, содержание которого в цикле синтез-газа допустимо до определенного уровня. Очистная колонна Purifier™ действительно удаляет оксиды углерода вместе с метаном, аргоном и другими атмосферными инертными газами. Таким образом, можно поддерживать низкое содержание инертного газа в цикле синтез-газа, применяя минимальную очистку, и это сохраняет ценный синтез-газ и повышает производительность процесса. В начале 2006 г. в Австралии построили самый большой завод Bur-rup Fertilizers Pty Ltd, использующий очистную колонну Purifier™, с производительностью 2,200 т/день. Кроме очистной колонны Purifier™, главными отличительными чертами является то, что воздушный компрессор приводится в действие паровой турбиной вместо газовой турбины, используемой в стандартной схеме Braun. Также установка первичного риформинга работает при умеренных температурных условиях, что позволяет рабочему давлению подняться до 40 атм., что хорошо влияет на работу очистной колоны Purifier™, а в процессе вторичного риформинга получается 42% избытка воздуха и используется неметаллическая смесительная горелка. В системе удаления C02 используется двухэтапный процесс, разработанный компанией BASF. В качестве конвертера аммиака применяется горизонтальная модель от фирмы Kellogg, состоящая из трех подложек с обычным магнетитом в качестве катализатора. И, наконец, он имеет унифицированный охладитель аммиака. Эксплуатационные испытания были проведены в июне. Завод работал на 100% рассчитанной мощности и даже больше, потребление энергии составило 6,78 Гкалл/т, что оказалось ниже проектного (8,86 Гкал/т). |