Меламин – С3Н6N6, 2,4,6-триамино-1,3,5-триазин, аминопроизводное симметричного триазина, тример цианамида или триамид циануровой кислоты, рис. 1.
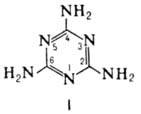 Рис. 1. Структурная формула меламина. Химически чистый продукт представляет собой бесцветные, не имеющие запаха кристаллы. Это соединение относится к классу циклических цианамидов и обладает комплексом свойств, являющихся следствием энергетической стабильности триазиновых ядер. К ним относятся тепло-, свето- и химическая стойкость, а также способность образовывать полифункциональные реакционноспособные химические соединения. Именно поэтому меламин – ценное сырье для получения очень многих полимерных соединений. Экскурс в историю В 1834 г. Либих впервые получил меламин при сплавлении тиоцианата калия с хлоридом аммония. В 1913 г, Штоле и Краух получили его другим путем, из дициандиамида, но первые промышленные установки, основанные на этом методе, появились значительно позднее, только в конце тридцатых годов ХХ века. После Второй мировой войны начали разрабатывать технологию производства этого продукта из карбамида. Синтез меламина из мочевины был впервые осуществлен в начале 40-х гг, но лишь в 60-е обратил на себя внимание промышленности. И до семидесятых годов прошлого века так и продолжали эксплуатироваться два типа установок получения меламина – из дициандиамида и из карбамида. Рост популярности способа синтеза меламина из карбамида совпал с ростом популярности последнего как удобрения. По мере того как производство карбамида приобретало массовый характер, а технология совершенствовалась, все более выгодным становилось производство меламина на его основе. В настоящее время весь этот химический продукт в мировой промышленности так и получают из карбамида. 
Специалисты ОАО «НИИК» (бывший Дзержинский филиал ГИАП) в конце 1950-х гг. первыми в мире разработали непрерывный процесс его получения из дициандиамида, который являлся исходным материалом, как и в большинстве промышленных процессов того времени, осуществлявшихся в периодическом режиме. Тогда же в Кировакане (Ванадзор, Армения) ОАО «НИИК» была спроектирована и успешно действовала более 20 лет промышленная установка высокого давления мощностью 6 тыс. т/год. Одновременно с ее проектированием были начаты исследования, направленные на создание процесса получения меламина из карбамида при высоком давлении. На их основании силами института в Дзержинске, на Чернореченском химзаводе (сегодня ОАО «Корунд»), спроектировали и построили опытно-промышленную установку. Однако параллельно проводившиеся за рубежом работы по созданию аналогичных процессов раньше достигли промышленного воплощения. С пуском в 1968 г. в Кировакане установки на базе закупленного у фирмы Montedison оборудования специалисты ОАО «НИИК» сосредоточились на процессе освоения приобретенной техники и решали проблемы: усовершенствования системы обогрева реактора, интенсификации процесса, повышения качества меламина, очистки сточных вод. Дальнейшие работы в том же направлении позволили спроектировать и запустить в 1985 г. в Кировакане новую установку, которая превосходила аналогичную (фирмы Montedison) по ряду параметров. Промышленные технологии Было предложено несколько технологических схем промышленного получения меламина на основе карбамида, каждая из которых обладала своими характерными особенностями. Схемы, прежде всего, отличаются тем, проводится ли синтез в одну или две стадии. Второе отличие – разное рабочее давление. При синтезе под высоким давлением обычно отпадает необходимость в катализаторах. Соответственно их применение позволяет проводить процесс при гораздо более низком давлении, вплоть до атмосферного. Вначале были разработаны схемы высокого давления. Значительные трудности при эксплуатации производства создавала коррозия оборудования, весьма интенсивная при высоких показателях температуры и давления. Первые установки низкого давления были пущены в 1967 г/ Разница в технологиях была также обусловлена необходимостью переработки побочных продуктов. При синтезе меламина из карбамида на один моль образовавшегося целевого прдукта приходится три моля диоксида углерода и шесть молей аммиака. Выбор схемы переработки этих отходов определялся, прежде всего, выбором метода синтеза меламина, а также местом расположения установки и возможностью переработки газов в производстве карбамида. Известные схемы отличаются и способами выделения меламина из реакционной смеси и его последующей очистки.Разработки фирм Montedison (Италия), Nissan Chemical (Япония) были основаны на пиролизе карбамида при высоком давлении без катализатора, в технологиях фирм BASF (ФРГ), Stamicarbon (Нидерланды), ChemiLinz (Австрия) используется каталитический пиролиз карбамида при низком давлении. Выбор методов делался компаниями на основе успешного развития какого-то определенного направления научно-исследовательских и проектно-конструкторских работ. По технологии пиролиза карбамида при высоком давлении без катализатора реакция образования меламина происходит при давлении 8-10 МПа и температуре 380-400°C; по технологии каталитического пиролиза карбамида при низком давлении – при давлении до 0,7 МПа и температуре 380-390°С. Оба процесса успешно конкурируют между собой, т.к. близки по технико-экономическим показателям. Качество получаемого меламина в обеих технологиях примерно одинаково, основными его показателями являются: - массовая доля меламина, не менее 99,7%; - массовая доля воды, не более 0,1%; - массовая доля нерастворимых в воде веществ, не более 0,01%; - массовая доля железа, не более 0,0005%; - pH 2%-го водного раствора 7,5-8,5. Из материалов иностранных фирм следует, что в каждом процессе имеют место выбросы в атмосферу, сточные воды и твердые отходы. ОАО «НИИК» предлагает технологию пиролиза карбамида при высоком давлении без катализатора. Предложение основано на собственном пакете ноу-хау, накопленном во время исследовательской и проектной деятельности, работ по научному сопровождению и совершенствованию технологии действующих промышленных установок. Технологии под высоким давлением имеют свои преимущества перед каталитическими: - нет необходимости решения ряда проблем, связанных с подбором катализаторов, поддержанием их активности, возможным отравлением, закупкой в связи с потерей активности, измельчением и износом (потери); - применение катализаторов может явиться источником нерастворимых примесей в полученном продукте;- присутствие катализатора в реакторе неизбежно усложняет его конструкцию в связи с необходимостью равномерного распределения газообразного сырья по всему сечению катализатора; - объемы реакционной аппаратуры в методах высокого давления значительно ниже, чем в методах низкого давления; - все процессы получения меламина из карбамида сопровождаются образованием большого количества стехиометрической смеси аммиака и двуокиси углерода. Наиболее рациональным способом использования этих газов является их рециркуляция в процессе производства карбамида. Способы высокого давления создают наилучшие условия для такой рециркуляции.Однако при всех плюсах процессы с высоким давлением требуют больших энергетических затрат на транспортировку исходного сырья. Конкретные сведения об усовершенствованных технологиях, предлагаемых сегодня, в открытой печати отсутствуют. О направлениях развития производства меламина можно судить по направлениям поисков, описанных в патентной литературе. Из этого анализа напрашивается вывод о том, что фирмы, имеющие процесс с использованием катализатора, активно занимаются исследованием процесса под давлением, и именно его реализуют на всех вновь вводимых установках. Сферы использования Меламин является важнейшим полупродуктом в производстве пластмасс. Получаемые на его основе меламиноформальдегидные смолы обладают многими преимуществами перед карбамидоформальдегидными. Получение меламиноформальдегидных смол – основное направление потребления меламина, имеющее широкое применение в производстве различных изделий технического и бытового назначения. Продукты отверждения смол из меламина, представляющие собой так называемые сетчатые полимеры, обладают высокой прочностью, тепло-, водо-, износо- и светостойкостью, что выгодно отличает их от карбамидоформальдегидных смол. Преимуществами изделий на их основе являются: значительно меньшая токсичность, большая прочность и теплостойкость, стойкость к горению, высокие декоративные качества и способность окрашиваться во всевозможные цвета. Указанные свойства определяют возможность широкого применения этих изделий в следующих областях: - пропитка декоративной бумаги в производстве слоистых пластиков, служащих отделочными материалами при облицовке мебели, стен, салонов транспортных средств, кабин лифтов и пр.; - производство лакокрасочных покрытий (ЛП) с хорошим цветосохранением и высоким сопротивлением износу, царапанью и истиранию; эти ЛП применяются при окраске автомобилей, бытовой электротехники и др.; - ламинирование древесностружечных плит и фанеры, используемых при изготовлении мебели и в строительстве; - изготовление пресс-композиций с различными наполнителями (целлюлоза, стекловолокно, древесная мука) при формовании посуды, пригодной для контакта с пищевыми продуктами, пуговиц, пепельниц, корпусов, ручек, кнопок, клавишей различных аппаратов, приборов и инструментов; - обработка бумаги, используемой в производстве обоев, карт, денег, ценных бумаг, а также для обработки тканей с целью придания им свойств безусадочности и несминаемости; - улучшение текучести жидкого бетона и снижение его водосодержания (пластификаторы для бетона); - производство огнезащитных вспучивающихся покрытий. Российский рынок Меламин является перспективным и востребованным на российском рынке продуктом. В России в настоящее время его не производят. До 1989 г. удовлетворение потребности в нем внутреннего рынка России и других республик бывшего СССР осуществлялось за счет производства меламина мощностью 20 тыс. т/год на Ванадзорском (Кироваканском) заводе «Рубин» и за счет закупок недостающего количества продукта по импорту. В 1988 г. в связи с землетрясением в Армении предприятие было закрыто. С 1989 года и до настоящего времени Россия меламин импортирует.Маркетинговые исследования рынка продукта, проведенные ОАО «НИИК», свидетельствуют о том, что текущее потребление меламина в России в 2004 году составило 23 тыс. т., в 2005-м ~ 26 тыс. т. (табл. 1). Таблица 1. Структура текущего потребления меламина в России. Районы потребления | Доля, % | Северный район | 6,0 | Северо-Западный район | 12,4 | Центральный район | 64,8 | Волго-Вятский район | 0,6 | Центрально-Чернозёмный район | 0,6 | Поволжский район | 1,3 | Северо-Кавказский район | 6,6 | Уральский район | 4,7 | Западно-Сибирский район | 2,3 | Дальневосточный район | 0,6 | Калининградская область | 0,1 | ВСЕГО: | 100 |
Из представленных в таблице 1 данных следует, что основные потребители меламина сосредоточены в Центральном районе. На его долю приходится 65% общего потребления продукта. Потребность Северо-Западного района составляет примерно 12%, Северного и Северо-Кавказского районов ~ по 6%, Урала ~ 5%. Доля других регионов незначительна.В таблице 2 представлена структура текущего потребления меламина по направлениям его использования, а также прогноз спроса на продукт в перспективе до 2015 г. Таблица 3. Потребность в меламине по направлениям использования. Направленияиспользования | 2005 г. | 2010 г. (прогноз) | 2015 г. (прогноз) | тыс. т | % | тыс. т | % | тыс. т | % | Ламинирование древесных плит (ДСП, МДФ, ОСБ) | 17,2 | 68 | 34,0 | 78 | 43,0 | 80 | Бумажно-слоистые пластики | 2,2 | 9 | 2,9 | 7 | 3,7 | 7 | Пластмассы | 1,0 | 4 | 1,3 | 3 | 1,7 | 3 | Лаки и краски | 1,9 | 7 | 2,4 | 5 | 3,0 | 5 | Прочие потребители | 2,9 | 12 | 2,9 | 7 | 3,0 | 5 | Итого | 25,2 | 100 | 43,5 | 100 | 54,4 | 100 |
Основным покупателем меламина, как и прежде, является подотрасль древесных плит лесопромышленного комплекса России. На долю ее приходится 70% общего потребления продукта за 2005 г. Предприятия лесопромышленного комплекса России используют меламин для ламинирования плит (ДСП, МДФ, ОСБ), их производство является одним из перспективных направлений в изготовлении мебели и деревянного домостроения. Развитие этой отрасли определяется наличием емкости внутреннего рынка и постоянно растущим спросом на продукцию. Объемы производства ламинированных плит ежегодно будут увеличиваться, будет расширяться и их ассортимент. Для обеспечения потребности страны в конкурентоспособных изделиях требуемого ассортимента и качества и для выхода на мировой рынок «Программой восстановления и развития производства древесных плит в Российской Федерации» предусматривается техническое перевооружение и реконструкция действующих заводов, а также строительство новых большой мощности на основе применения современного оборудования и технологических процессов. Доля подотрасли древесных плит в структуре общего потребления меламина в России к 2010–2015 гг. возрастет примерно до 80%. Если считать, что доля России в общем потреблении меламина в странах СНГ осталась на прежнем уровне и составляет 65÷70%, то можно оценить суммарное потребление этого продукта в странах СНГ с учетом России: - 2005 г. ~ 40 тыс. т/год; - 2010 г. ~ 60 тыс. т/год; - 2015 г. ~ 80 тыс. т/год. Быть или не быть? Российский рынок меламина, перспективный и динамично развивающийся, сегодня весьма привлекателен для зарубежных фирм. По этой причине предложения по поставке в Россию технологии и оборудования для производства продукта носят скорее декларативный характер. По ряду косвенных признаков можно говорить о направленной политике ведущих мировых компаний-производителей и владельцев технологии меламина препятствовать созданию этого производства в России. И все же самый логичный ответ на вопрос: быть или не быть производству меламина в России? – будет оптимистичным: быть! В нашей стране есть для этого все предпосылки: наличие производственных мощностей карбамида, к которым должна быть привязана установка по производству меламина, активно развивающийся рынок, благоприятная для производителей цена на газ и, соответственно, низкая себестоимость карбамида – основного сырья для производства продукта. Есть отечественная компания – ОАО «НИИК», которая располагает опытом проектирования промышленных установок для производства меламина из карбамида с использованием процесса высокого давления. Собственный пакет ноу-хау, накопленный во время исследовательской и проектной работы, позволяет коллективу института проектировать агрегаты мощностью 20 тыс. т/год. Разносторонний опыт этой организации в области технологии карбамида дает возможность найти оптимальные решения по привязке производства меламина к производству карбамида, с учетом существующих мощностей и технологий или вновь создаваемых установок карбамида. Многолетний стаж разработки, изготовления и поставки оборудования, в том числе высокого давления, способствует тому, что институт может предложить не только инжиниринг, но и комплектную поставку оборудования для производства меламина. По материалам статьи, опубликованной в журнале «Химия и бизнес» |