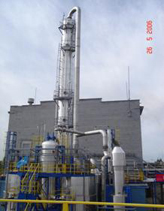 Безотходная технология производства клеящих смол на деревообрабатывающих предприятиях Современная деревообрабатывающая промышленность во многом обязана своим развитием использованию недорогих смол и связующих на основе формальдегида. Они на порядок дешевле альтернативных смол (эмульсия ПВА, эпоксидные смолы) и, при этом, обеспечивают приемлемые прочностные показатели. На сегодняшний день в мире сложились два механизма обеспечения потребностей деревообрабатывающих производств смолами: централизованная поставка смол предприятиями химической промышленности; приготовление смол непосредственно на деревообрабатывающих производствах. В России и странах СНГ в равной степени используются оба механизма. Применяемая на деревообрабатывающих предприятиях традиционная технология синтеза смол используется с начала 60-х годов и не отвечает современным требованиям по экологической безопасности. К тому же, отсутствие должного внимания к качеству производимых смол со стороны крупных фирм-поставщиков вынуждает малые предприятия выдерживать давление со стороны природоохранных органов и всеми силами бороться за сохранение своих смоляных цехов. Типовой цех смол, выпускающий карбамидоформальдегидные смолы для производства древесностружечных плит или фанеры, использует в качестве сырья формалин (37% раствор формальдегида в водно-метанольной среде) и карбамид. Смола изготавливается периодическим способом в реакторах, оборудованных мешалкой и рубашкой, где, в определенном кислотно-температурном режиме, проводится процесс поликонденсации исходных реагентов с последующим удалением надсмольных вод (стадия сушки) и доконденсацией не прореагировавшего формальдегида карбамидом. Недостатки такой технологии хорошо известны: сточные воды, потери формалина и метанола, долгий процесс варки и сушки, большие расходы пара и электроэнергии, малый выход товарной смолы из реактора. Помимо этого, прием и хранение формалина в зимний период требует постоянного подогрева емкостей паром. Часть формалина улетучивается, еще большая часть остается в виде параформа в цистернах и осаждается в емкостях.При изготовлении стандартной смолы марки КФМТ-15 образуется приблизительно 300 килограмм надсмольной воды на тонну выработанной смолы. Типовое производство ДСП мощностью 100 тысяч кубометров потребляет около 12 тысяч тонн смолы в год. Соответственно, предприятию ежегодно приходится сбрасывать в очистные сооружения более трех тысяч тонн надсмольных вод, содержащих около сорока тонн формальдегида и свыше трехсот тонн метанола. Таким образом, нагрузка на окружающую среду является неприемлемой. В последнее время решению данной проблемы уделяется большое внимание со стороны исследовательских институтов и отраслевых лабораторий. Предлагались различные варианты утилизации надсмольных вод, в том числе их подача в сушилки, сжигание, связывание свободного формальдегида аммиаком или карбамидом, возвращение отходов изготовителю сырья на переработку, и другие. Все перечисленные методы не нашли широкого применения из-за их низкой эффективности или экономической нецелесообразности. Санкт-Петербургское предприятие ЗАО “Безопасные Технологии”, занимаясь исследованиями в области металло-оксидного катализа и межфазной абсорбции, разработало безотходную технологию синтеза карбамидоформальдегидных смол полунепрерывным способом с использованием газожидкостного процесса получения формальдегидного концентрата на установках модульного типа. Установка представляет собой ряд аппаратов, объединенных в единый технологический модуль с оригинальной компоновкой. Предлагаемая технология изготовления карбамидных смол является сочетанием непрерывного процесса синтеза формалинового концентрата и периодического процесса поликонденсации формальдегида карбамидом, проводимого в обогреваемых реакторах по ускоренной, безотходной, энергосберегающей технологии. В технологическом процессе синтеза форконцентрата, метанол, проходя через испаритель, смешивается с потоком воздуха и подается в реактор. 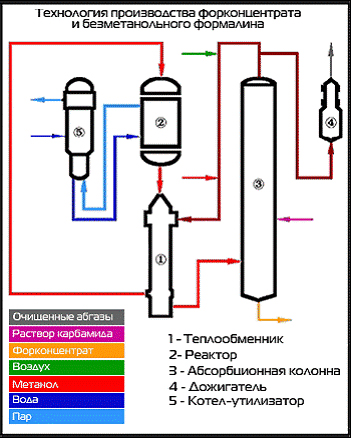 В процессе окисления кислородом воздуха на железо-молибденовом оксидном катализаторе происходит образование формальдегида- газа. После охлаждения в рекуператоре, газообразный формальдегид поступает в абсорбционную колонну, где поглощается водным раствором карбамида с образованием формалинового концентрата. Выходящий из колонны воздух, содержащий следы формальдегида, метанола и побочных продуктов реакции, перед выбросом в атмосферу подается в каталитический конвертер (дожигатель), где происходит его полная очистка от загрязняющих веществ. Процесс полностью автоматизирован и управляется одним оператором. Полученный концентрат и карбамид подаются в обогреваемый реактор, оборудованный мешалкой, где проводится синтез карбамидоформальдегидной смолы в заданном кислотно-щелочном режиме. Готовая смола, после охлаждения, поступает на склад готовой продукции.  По мнению Центрального научно-исследовательского института фанеры (АОЗТ ЦНИИФ), головной научно-исследовательской организации в области разработки технологии изготовления синтетических клеящих смол, использование модульных установок позволяет реализовать высокоэффективную энергосберегающую и экологически безопасную технологию изготовления карбамидоформальдегидных смол. В отличие от применяемой в настоящее время технологии, основанной на использовании привозного формалина, предлагаемая технология синтеза карбамидоформальдегидных смол имеет ряд существенных преимуществ: полное отсутствие сточных вод и других отходов производства, двукратное увеличение производительности оборудования, значительное уменьшение потребления пара и электроэнергии, существенное сокращение расходов на транспортировку и хранение сырья. Сравнительный анализ традиционной и предлагаемой технологий приведен в Таблице 1. Новая технология позволяет на современном уровне реализовать целый ряд крупных проектов по расширению, реконструкции и техническому перевооружению цехов по производству синтетических смол, входящих в состав предприятий Лесопромышленного комплекса России.
Семен Исаакович СТОМПЕЛЬ кандидат химических наук, Михаил Игоревич СИБИРЕВ Кандидат технических наук,
ЗАО “Безопасные технологии”
|