Однако пионерами повсеместного применения цифровой техники стали многозонные регуляторы, такие, как представленные на K’79 Multiplastomatic, и, в первую очередь, используемые с 1983 года системы PMC 1000 с 12-канальными картами термостата, управлением посредством цветного дисплея и функцией сохранения рецептур, в том числе на съемные электронные носители информации. Удобство управления улучшено за счет графических элементов, таких как пиктограммы и представления статистических кривых, а также технологии адаптивного считывания параметров регулирования и автоматического последовательного управления приводами (функция обучения) и унифицированных единых обусловленных технологическим процессом стратегий управления. Уже в этом поколении были внедрены первые привязки к главным производственным компьютерам. В последующие десятилетия модули становились все меньше и мощнее. Алгоритмы регулирования продолжали совершенствоваться и оптимизировались для универсального применения. Место электронно-лучевых трубок заняли плоские дисплеи, а стандартизированные полевые шины объединили в сети компактные модули автоматизации (P8, P-open), которые заменяют более объемные 19“ съемные платы. Благодаря концепции полевых шин были интегрированы такие технологии оптимизации как гравиметрия, регулирование центрирования труб и толщины стенок. Сегодня имеется широкий ассортимент особенно компактных сенсорных экранов (например, в системах varioEC они имеют диагональ 5,7“, 10“, 12“, вплоть до 20“), которые обеспечивают простоту управления одним касанием пальца, что по достоинству оценили на практике операторы машин! Сегодняшняя промышленная компьютерная технология делает возможным экономически выгодное использование проверенных и хорошо известных в офисном мире технологий (интерфейс Ethernet, OPC-сервер) для объединения в корпоративные сети, дистанционной диагностики через интернет, обеспечения качества, анализа баз данных и т.д. Мощность современных модулей автоматизации выросла настолько, что многие задачи могут надежно решаться небольшим количеством микропроцессоров, или даже одним (множественное регулирование температуры, измерение давления расплава, управление скоростью вращения и т.д.). Надежность используемых электронных деталей возросла еще больше: теперь нет необходимости в подвижных механических деталях, таких как вентиляторы или жесткие диски, кроме того, современные технологии отличаются заметным увеличением срока службы фоновой подсветки. Следующий важный пункт заметно отражается на бюджете - в последние десятилетия расходы стали чрезвычайно ниже! Даже при оснащении простыми дискретными одиночными приборами – отдельными термостатами, индикаторами / регуляторами приводов, средствами контроля давления расплава – экструдеры стоят значительно дороже по сравнению с самой компактной системой автоматизации varioEC. За счет использования новой компактной техники также заметно снижаются расходы на установку. При этом новые системы дают пользователям и другие материальные преимущества, о которых будет подробно рассказано ниже. 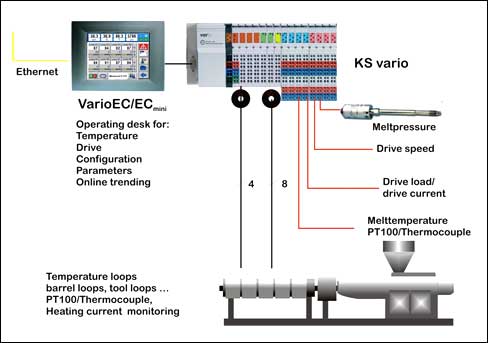
Переоборудование: критерии рентабельности Зачем вообще нужно переоборудование экструзионных установок? При условии своевременной замены изнашивающихся деталей, механические части экструдера на протяжении десятилетий сохраняют свою функциональность. Однако, несмотря на профилактические работы, работоспособность старых установок снижается, а расходы растут. Старые регуляторы на базе релейной техники, мониторы с ЭЛТ-трубками, устаревшие средства управления все чаще выходят из строя. Это ведет к повышению затрат на ремонт и увеличению производственного брака. Вместе с тем требования, предъявляемые производством растут, и даже при использовании «простых» и не новых экструдеров растет стремление к модернизации средств сбора данных измерений с целью обеспечения качества и оптимизации техпроцесса. Но интеграция отдельных систем MDE означает почти такие же высокие издержки, как при переоборудовании на новые компактные системы для комплексной автоматизации! Воспроизводимое производство требует сохранения рецептур и надежного повторения установок заданных параметров. Для исключения ошибок оператора здесь необходимы всеохватывающие способы обработки данных, которые старые системы не в состоянии обеспечить. Итак, желаний много, однако не всегда есть возможность вложить средства в совершенно новые экструзионные установки. Поэтому перед тем, как принять решение об инвестициях, целесообразно сравнить сопутствующие затраты и эффективность с таковыми при модернизации. В первую очередь необходимо внести ясность в ключевой вопрос: кто может / должен выполнять переоснащение? •При отсутствии на предприятии собственных специалистов-электриков все переоборудование и ввод в эксплуатацию необходимо поручить поставщику средства автоматизации и производителю распределительных шкафов! •При наличии таковых возможно разделение труда. Работы с электрическими сетями проводятся самостоятельно в соответствии с предписаниями поставщиков средств автоматизации, а ввод в эксплуатацию осуществляется затем при поддержке приглашенных специалистов. •При наличии собственных специалистов-электриков и специалистов по автоматизации, а также согласованном предоставлении базового программного обеспечения (исходного кода комплексного пакета) возможна собственная модификация панели управления и управляющих программ (ПЛК в соответствии IEC 61131-3) для индивидуальных решений (это относится в первую очередь к машиностроителям и крупным экструзионным предприятиям). Важнейшие параметры техпроцесса – физические основы Наряду с регулированием температуры (нагрев / охлаждение) отдельных зон и индикацией температуры расплава со всеми функциями контроля (блокировка запуска, управление шнеками, поле допусков, превышение температуры (например, отключение охлаждения или нарушения в работе твердотельных реле) осуществляется контроль соответствующих токов нагрева. Измеряется скорость вращения шнеков и контролируется аналоговая величина нагрузки (крутящий момент). Также измеряется и контролируется давление расплава. Предусмотрена автоматическая калибровка датчика давления расплава DMS. Средства измерения других показателей периферийного оборудования могут соединяться с системой посредством имеющихся подключений. Таким образом, на экструдере можно оценить или настроить все «классические» сигналы.
|