Создание образцов листа Были созданы образцы листа шириной 640 мм и длиной 890 мм и толщиной, в пределах допуска, 4.7 мм. Образцы листа изготавливались с помощью экструзии листа на экструдере с диаметром 63.5 мм, соотношением длины и диаметра 30 и при температуре около 230 град. С и производительностью 113 кг в час. Реологическая и физическая характеристика Объемная вязкость была измерена при 170oC на приборе, называющемся объемным реометром Sentmanat (SER) fixture (Xpansion Instruments).[1] Прибор SER основан на системе с двойными вальцами. Он сконструирован как устройство на основе стандартного ротационного вискозиметра, которое состоит из иерархически функционирующих наматывающих барабанов, соединенных через систему сцепленных шестерен. Постоянная скорость деформации по Хенки получается просто благодаря заданной скорости наматывания. SER устанавливается внутри камеры искусственного климата вискозиметра с усовершенствованным реологическим расширением (ARES). Испытания проводились на полосках, вырезанных из листов толщиной 0.5 мм, изготовленных методом прессования в форме. Применялись постоянные скорости деформации по Хенки (1 и 10 s-1), и определялось напряжение, зависящее от времени, от измеренного крутящего момента, а также от зависящего от времени поперечного сечения образца. Объемную вязкость получали за счет деления натяжения на постоянную скорость деформации по Хенки. Скорость течения расплава определялась для всех компаундированных образцов в соответствии с ASTM D-1238 с нагрузкой 2.16 кг. для 10 минут при 230oC. Свойства основного материала были измерены с использованием образцов, изготовленных литьевым формованием. Модуль упругости при изгибе был измерен в соответствии с ASTM D-790 со скоростью 0.13 см в минуту после испытания в течение, по крайней мере, 48 часов. Ударопрочность с надрезом по Изоду измерялась в соответствии с процедурами, определенными в ASTM D-256. Устойчивость против провисания Образцы листов были последовательно сформованы на машине для термоформования с возвратно-поступательным движением ZMD International Model V223. Каждый из листов размещался в зажимной раме термоформовочной машины, и жестко зажимался со всех четырех сторон. Далее, зажатый лист направлялся в станцию нагревания термоформовочной машины, где лист нагревался за счет поглощения инфракрасного излучения, поступающего из кварцевых излучающих инфракрасные лучи нагревателей. По мере того, как температура листа повышалась, изначально плоский лист начинал прогибаться под тяжестью своего собственного веса, как схематично изображено на Рисунке 1. 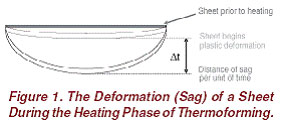
Рисунок 1. Деформация (провисание) листа во время этапа нагревания при термоформовании Объем провисания был ограничен конфигурацией оборудования и сказывался на качестве конечной детали. Вертикальное расстояние провисания листа от изначального положения рамы зажимного устройства измерялось с использованием инфракрасного профилирующего сканера (световая завеса), который расположили для обнаружения провисания в середине печи. Было зафиксировано время, которое потребовалось для обнаружения провисания листа с 57 мм ниже начального положения до 108 мм от начального положения. Скорость провисания была определена с помощью деления изменения вертикального расстояния листа на время, необходимое для изменения высоты. Лист извлекали из печи, когда провес достигал примерно 108 мм от изначального положения, и перемещали на станцию формования. В конце термического цикла измеряли температуру поверхности листа на нижней части листа с помощью инфракрасного пирометра. После того, как нагретый лист размещали в станции формования, вакуумная камера вступала в контакт с листом снизу. Вакуум используется для того, чтобы втянуть лист в вакуумную камеру и осуществить его предварительное растяжение. Механически обработанную алюминиевую пресс-форму, показанную на Рисунке 2, опускали поверх предварительно растянутого листа, и использовали вакуум для вытяжки 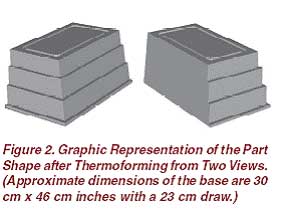 Рисунок 2. Графическое представление формы детали в двух видах (примерные размеры основания составляют 30х46 см. с вытяжкой в 23 см).
расширенного листа по всей форме в то время, как вакуум выпускался из вакуумной камеры. Деталь формовали и давали ей охладиться, затем ее окончательно извлекали из рамы зажимного устройства. |