4. Какие пространственно-логистические факторы необходимо было учесть? Существующая планировка завода оставляла для строительства нового холодильника лишь узкое пространство шириной 12 м. Однако даже это ограниченное пространство необходимо было сделать доступным, убрав здание столовой. При ширине холодильника 4,5 оставалось очень мало площади для установки лестниц, платформ для техобслуживания, вентиляторов и дополнительного оборудования клинкерного холодильника. Это поставило перед конструкторами сложную задачу использования каждого квадратного метра свободного пространства (рис. 4). Вертикальная реперная точка для новой печной установки была определена по положению прежнего кабельного тоннеля, проходящего под поверхностью земли по территории, где планировалось поставить клинкерный холодильник. Из-за старого оборудования, установленного на расстоянии прямой видимости, перенос этого тоннеля был невозможен. Поэтому стало невозможным и использование подвальных помещений, определив необходимость сооружения всех конструкций над поверхностью земли. Таким образом, клинкерный холодильник был построен на стальной платформе высотой 3 м, чтобы конец холодильника, где происходит выгрузка, находился достаточно высоко с точки зрения расположенного над землей коротколоткового пластинчатого конвейера. Узость строительной площадки диктовала, чтобы остальные конструкции монтировались вверх, а не в ширину. Например, на печном фундаменте №3 должны располагаться три вентилятора охлаждения на двух уровнях – станцию гидропривода холодильника, обычно располагающуюся в этой области, пришлось переносить на фундамент №2, что повлекло за собой удлинение трубопровода. Оставшиеся четыре вентилятора пришлось устанавливать под углом 90° от обычного расположения, чтобы они уместились в узком пространстве между холодильником и зданием трансформаторной подстанции. Для дальнейшего техобслуживания эти вентиляторы будут доступны только с платформы горелки при помощи мостового крана, но и при этом понадобится снять несколько плит с платформы (рис. 5). Расположение над землей всех машин и оборудования означает, что в пределах видимости от теплообменника и холодильника не будет ни одного кармана, и потенциальный риск в случае просыпания горячей муки значительно снижается. 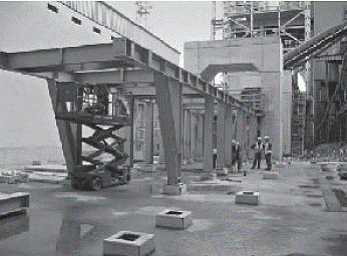
Рис. 4. Сборка стальной платформы 5 Последовательность установки и интеграции в существующую технологическую линию завода В августе 2007 г. компания IKN подписала контракт с группой Lafarge Zement на разработку и поставку клинкерного холодильника, включая головку печи и валковую дробилку. Поскольку пуск оборудования в эксплуатацию планировался весной 2009 г., график контрольных сроков был очень жесткий. Презентация основного проекта состоялась в октябре 2007 г., сооружение фундамента – в апреле 2008 г., поставка всех компонентов осуществлялась к июню 2008 г., а предварительная и основная сборки проходили с июля 2008г. Немецким заводам был поручен весь спектр производства наиболее важных функциональных компонентов клинкерного холодильника: качающейся рамы, гидравлического привода и валковой дробилки. В целях обеспечения качества эти компоненты также полностью собирались и испытывались там, где производились, во избежание риска при сборке на строительной площадке. Работа по сборке началась по графику, в июле 2008 г., параллельно работам по строительству башни теплообменника. Вначале были возведены опорные конструкции (рис. 4), затем шаг за шагом нижний корпус холодильника c колосниковым полотном. После приемочных и функциональных испытаний трехвалковая дробилка (рис. 6) в собранном и готовом состоянии была привезена на строительную площадку на автотрейлере с плоской грузовой платформой и просто опущена на заранее подготовленные рельсы в холодильнике без необходимости дальнейшей сборки. Таким же образом был поставлен и установлен узел гидравлического привода колосниковых решеток, полностью функционально оттестированный в комплекте с блоком ПЛК. 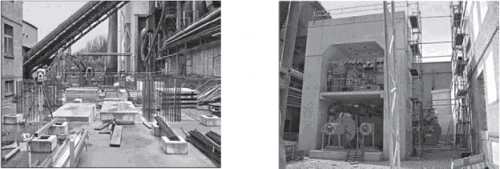
Рис. 5. Работы по строительству фундамента для вентиляторов охлаждения и стойка №3 (слева), а также готовая стойка с тремя вентиляторами на двух уровнях 6 Преодоление трудностей Основная инженерная фаза работы характеризовалась интенсивной координационной деятельностью между партнерами проекта, что было крайне важно для того, чтобы успешно разрешить сложную задачу строительства в ограниченном пространстве уже существующего предприятия. Специальные меры предосторожности были продуманы на начальной стадии. Это позволило снизить риски при случайном прорыве горячей муки из системы, а также обеспечить удобный доступ для инспекций и техобслуживания, сохранив существующую инфраструктуру и используя стальную платформу (рис. 7) для минимизации фундаментных и бетонных работ при установке нового холодильника с маятниковыми колосниками. Компоненты холодильника были поставлены по графику, фаза сборки была проведена без сбоев, оборудование принято для дальнейшей интенсивной работы. Благодаря функциональным испытаниям, проведенным до поставки, холодный пуск был произведен по плану, т. е. все было подготовлено для беспроблемного горячего пуска в конце первого квартала 2009 г. 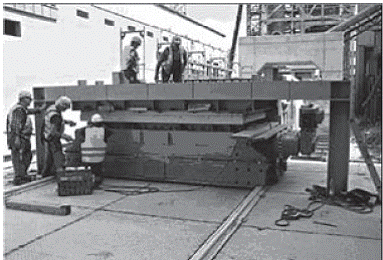
Рис. 6. Трехвалковая дробилка – валки приводятся индивидуально при помощи реверсивных электромоторов (11 кВт) 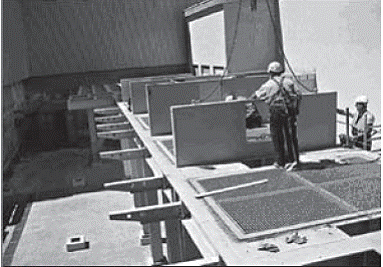 Рис. 7. Стальная платформа, служащая для установки холодильника с маятниковыми колосниками C текущей ситуацией и прогнозом развития российского рынка цемента можно познакомиться в отчетах Академии Конъюнктуры Промышленных Рынков «Рынок цемента в России». Цемент. Известь. Гипс.
|