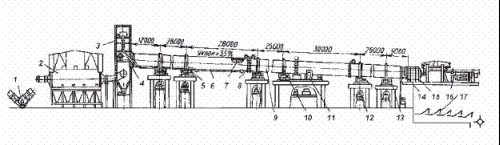
Рис. 2. Печной агрегат сухого способа производства с вращающейся печью 4,5 х 80 м с циклонным теплообменником возрастает в разы, а значит возрастает и эффективность теплообмена. Серьезные инвестиции в охладители также позволили значительно повысить эффективность их работы. Охладители стали компактнее, до 75% возрос их КПД при снижении расхода электроэнергии до 6…8 кВт•ч/т клинкера и расхода охлаждающего воздуха с (2,6…3,2) до (1,4…1,6) нм3/кг клинкера. Таким образом, современные технологии обжига по сухой схеме отражены в следующих мероприятиях: – применение теплообменников с циклонами современной конструкции, обеспечивающих низкую потерю давления и высокоэффективное пылеотделение; – применение изменяемых декарбонизаторов, приспособленных для сжигания всех видов природного и вторичного топлива, обеспечивающих равномерное распределение по его сечению сырьевой муки, топлива и воздуха для горения при максимально полном сгорании топлива, включая альтернативное, при высокой степени декарбронизации (до 95%) сырьевой муки; – применение коротких вращающихся печей с низкой потерей тепла через корпус и небольшим энергопотреблением, обеспечивающих меньшие инвестиционные затраты как на механические узлы, так и на строительство при меньших затратах на расход огнеупоров; – применение охладителей последнего поколения с максимально высокой степенью рекуперации тепла за счет отсутствия эффекта фонтанирующего воздуха при минимальном износе рабочих поверхностей, где благодаря отсутствию относительного движения между клинкером и колосниковой решеткой. В табл. 1 показан расход тепла современных печей сухого способа. Анализ табл. 1 показывает, что современные печные системы сухого способа производства весьма эффективны с точки зрения теплового КПД. Представленные данные соответствуют печным агрегатам с большой производительностью, где относительные потери тепла меньше, чем в малых печных агрегатах. Низкий расход топлива при данном способе производства цемента, обеспечивает низкий выход СО2, составляющий 540…570 кг/т клинкера от сырьевых материалов. Уровень выбросов СО2 от сгорания зависит от вида применяемого топлива. Снижение выбросов СО2 от сгорания топлива можно достичь путем замещения обычного топлива биомассой или горючими отходами. Например, растворителями, обрезками пластмассы, деревянной щепой и т. д., которые могут быть поданы в декарбонизатор для сжигания. Более крупнокусковое топливо (покрышки, крупногабаритные отходы) можно сжигать во внешних устройствах, в которых обеспечивается более длительное время их горения. Таблица 1. Расход тепла в печах, работающих по сухому способу производства 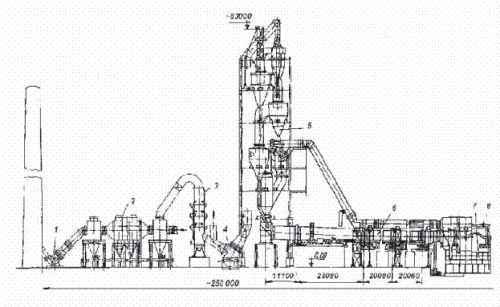
Концентрация NOx в отходящих газах по сухой схеме производства увеличивается до 500…2500 мг/нм3. Для снижения NOx целесообразно применять декарбонизаторы современных конструкций, а также проводить мероприятия, уменьшающие выброс NOx на тракте сброса отработанного воздуха в атмосферу. Активность клинкера при сухой схеме производства составляет 40…45 МПа. Учитывая, что при производстве цемента по сухому способу перерабатываются большие объемы сухих сыпучих материалов, на всех переделах наблюдается сильное пыление, требующее дополнительной установки пылеочистного оборудования. Разработаны печные агрегаты производительностью до 12 000 т/сут клинкера. Преимущества производства по сухому способу используются в полусухой схеме производства цемента. Здесь подготовка сырьевой муки осуществляется по сухому способу, а готовая сухая смесь затем увлажняется до 10…14% для образования гранул размером 8…15 мм. Полученные гранулы обжигаются в конвейерном кальцинаторе типа Леполь (рис. 3), в котором гранулы высушиваются, подогреваются и частично декарбонизируются отходящими печными газами. В современных конструкциях кальцинатор разделен перегородкой (3) на две камеры – сушки и подогрева. Отходящие печные газы дважды просасываются системой дымососов через слой гранул для максимально полного использования тепла, нагревая их до 700…800°С. Затем они попадают в печь для обжига. 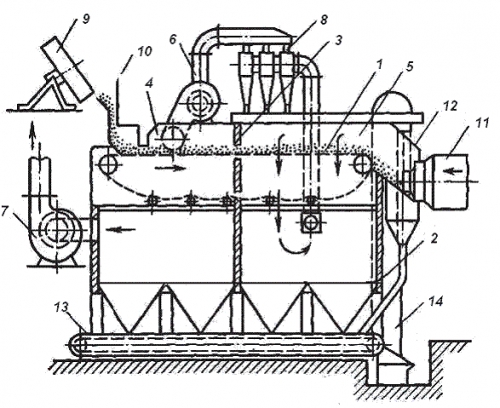
Рис. 3. Конвейерный кальцинатор Расход тепла на обжиг в печах Леполь составляет 800…950 ккал (3,40…4,0 МДж) на 1 кг клинкера при производительности 25…38 т/ч. С увеличением размера печи удельный расход тепла падает. Например, печь размером 3,6 х 40 м имеет расход 808 ккал на 1 кг клинкера, а печь размером 3,8/4 х 60 м – 760 ккал на 1 кг клинкера. Известны и более крупные установки печей Леполь производительностью до 2000 т/сут при расходе тепла 720 ккал (3,2 МДж) на 1 кг клинкера и потреблении электроэнергии 12…13 кВт•ч/т. К недостаткам этих печей следует отнести возможность обжига только пластичных. Сырьевых материалов, дающих прочные гранулы, сложность конструкции самого конвейерного кальцинатора, увеличивающая расходы на ремонт, а также трудности, возникающие при установке необходимого аэродинамического режима работы печного агрегата. Опыт эксплуатации предприятий цементной индустрии показал, что клинкер, полученный по мокрому способу производства, качественнее, чем клинкер, полученный по сухому способу. В первую очередь это объясняется тем, что степень гомогенизации сырьевой смеси в первом случае выше. Улучшается корректирование химсостава, а также меньшее пыление при подготовке шлама и т. д. К тому же, учитывая то, что влажность основных компонентов сырьевой смеси многих предприятий России превышает 20%, нецелесообразно высушивать эти компоненты перед обжигом, чтобы в итоге получить клинкер не самого высокого качества. Преимущества мокрого и сухого способов производства цемента сочетаются в комбинированном способе. Получаемый на заводе шлам влажностью 35…45% обезвоживается до 16…21% (кек) в прессильтрах, затем высушивается отходящими печными газами до 0,5…1,0% влажности, как правило, в молотковых аэробильных дробилках-сушилках и обжигается во вращающихся печах с циклонными теплообменниками (рис. 4). В Аргентине работает завод мокрого способа с печью Леполь. На пресс-фильтрах влажность шлама снижается до 14…15%, и кек в барабанном грануляторе превращается в гранулы размером 8…12 мм. Расход тепла на обжиг в этой печи составляет 1000 ккал/кг (4,19 МДж/кг) клинкера. В Нигерии работает цементный завод с запечным теплообменником в виде шахты. Кек влажностью 20% формуется в виде маленьких цилиндров. Затем цилиндры загружаются на вращающийся подогреватель шахты, где высушиваются и частично декарбонизируются, а оттуда поступают во вращающуюся печь. Производительность печи 3,8 х 60 м – 25 т/ч при расходе тепла на обжиг 1000 ккал/кг (4,19 МДж/кг) клинкера.
|