Учитывая, что влажность кека обычно находится в пределах 18…22%, то для его сушки достаточно тепла отходящих газов после третьей ступени циклонных теплообменников. При переводе печей мокрого способа на полумокрый можно получить экономию приблизительно 70…80 кут/т клинкера, т. е. 35…40% (рис. 4). 3.2. Сухой способ при использовании мягкого сырья высокой влажности (вариант II.c) Если используется легко измельчаемое сырье высокой влажности, то может быть применена такая же технологическая схема получения клинкера, только без выделенного сырьевого цеха и отделения фильтр-прессов, как это реализовано фирмой FLSmidth на заводе Chelm в Польше. Таблица 3. Газовые потоки по печной системе, нм3/кг клинкера 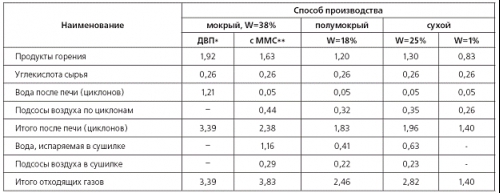
*ДВП – длинная вращающаяся печь **ММС – молотковая мельница-сушилка (дробилка-сушилка) В этом случае сырьевые компоненты с усреднительного склада поступают непосредственно в мельницу-сушилку. Для обеспечения при этом требуемого качества сырьевой смеси следует проводить непрерывный контроль химического состава и влажности с использованием современного поточного нейтронного анализатора, а также регулировать соотношение компонентов на складе высокоточными массовыми дозаторами. Для регулирования заданной тонкости помола после мельницы-сушилки устанавливается сепаратор. Количество ступеней циклонного теплообменника определяется в зависимости от влажности сырьевой смеси (рис. 4) с тем, чтобы тепла отходящих газов было достаточно для ее сушки. Теплотехнические расчеты показывают, что при влажности сырья в пределах 22…34% требуются две ступени. Так как при использовании мелового карбонатного компонента влажность сырьевой смеси обычно находится в пределах 22…28%. то расход топлива по данной технологии может составить ориентировочно 900…1050 ккал/кг или 130…150 кут/т клинкера. 3.3. Сухой способ при использовании твердого сырья пониженной влажности (вариант III) Данная традиционная схема имеет наибольшее распространение, когда по «классической» технологии осуществляется подготовка сырьевой смеси путем усреднения компонентов на складе, помола и сушки в вертикальной валковой мельнице и корректировки в силосах. Обжиг готовой сырьевой смеси осуществляется в короткой вращающейся печи с многоступенчатым циклонным теплообменником и декарбонизатором. Число ступеней определяется влажностью сырья и находится в пределах 4…6 (рис. 4). Согласно теплотехническим расчетам, при использовании в качестве сушильного агента отходящих газов после циклонов и избыточного воздуха из холодильника, суммарным теплоносителем можно высушить сырье с влажностью 13…5%. При этом удельный расход условного топлива на тонну клинкера составит: при четырех ступенях – 110 кг, при пяти – 100 кг, при шести – 90 кг, а температура отходящих газов – 360, 300 и 250оС соответственно. 4. Полумокрый и сухой способы производства с дополнительным сушильным агентом (варианты IV.b и IV.с) Данная технологическая схема имеет ряд преимуществ перед остальными, которые заключаются в следующем. 1. В случае, когда сушильный агент подается в сушилку, минуя печь и циклоны, можно стабилизировать влажность сырья на входе в печную систему, например, на уровне 1±0,5%, и таким образом применять однотипную схему с постоянным числом ступеней теплообменника независимо от влажности сырья. 2. В данном случае в процессе применения декарбонизаторов реализуется важный дополнительный технологический принцип, заключающийся в том, что, как уже отмечалось раньше, при высокой влажности сырья значительное количество тепла тратится на испарение воды. Во всех предыдущих схемах необходимый сушильный агент поступал из декарбонизатора через все циклоны. По данный схеме сушильный агент напрямую подается в сушильный агрегат, и, следовательно, разгружаются циклоны от избыточного газового потока. Так, при влажности сырья 18% объем избыточно просасываемого через циклоны газа ΔVг составит 0,43 нм3/кг клинкера или 23%, а при влажности 25% – ΔVг – 0,56 нм3/кг или 29% (табл. 3). Учитывая, что работа циклонных теплообменников определяется их газодинамикой, то, если исключить этот газовый поток из системы, на такую же величину можно уменьшить сечение газоходов и циклонов или увеличить производительность печи. 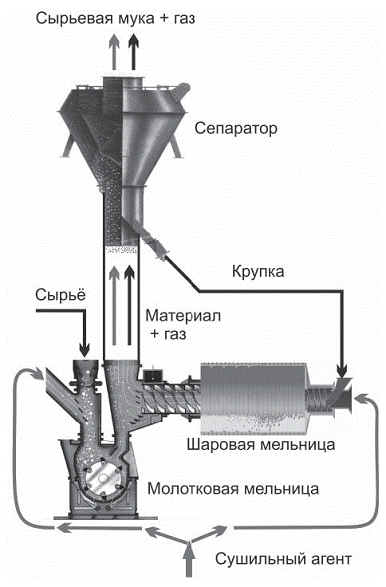
Рис. 5. Рациональная схема измельчения и сушки сырья при использовании компонентов повышенной влажности с твердыми включениями 3. Вследствие того, что по данной схеме топливо распределяется в три зоны, то в каждой зоне легко поддерживать заданные параметры путем изменения расхода топлива и, следовательно, автоматизировать процессы сушки и обжига клинкера. 4. По данной схеме для получения сушильного агента целесообразно использовать газотурбинную установку с генератором для выработки электроэнергии. При относительно высокой влажности сырья можно получить электроэнергию, достаточную для покрытия собственных нужд цементного завода. В этом случае полностью утилизируется тепло отходящих газов из турбины. На основании опыта работы Белорусского завода, установлено, что стоимость одного кВт•ч снижается в 1,5 раза. Если в легко размалываемом сырье присутствуют твердые включения, то в качестве помольно-сушильного агрегата целесообразно применять «тандем-схему», состоящую из молотковой мельницы-сушилки и шаровой мельницы для домола крупки, разработанную и внедренную фирмой KHD Humboldt Wedag GmbH в Стерлитамаке (рис. 5). Для измельчения и сушки твердых сырьевых компонентов несомненный интерес представляют последние разработки этой же фирмы на основе новой модификации пресс-валкового измельчителя (роллер-пресса) с высоко износоустойчивой поверхностью, статического-V и динамического сепараторов (рис. 6). 5. Заключение 1. На основании проведенного анализа различных тепловых систем можно сделать заключение о целесообразности реконструкции цементных заводов мокрого способа с переводом их на полумокрый или сухой способы в зависимости от природных свойств сырья. Во всех случаях предпочтение следует отдать варианту IV, когда сушильный агент напрямую, минуя циклоны, подается в сушилку. Это позволит полностью стандартизировать оборудование печной системы, не приспосабливая ее к влажности сырья, и, следовательно, уменьшить затраты на проектные и конструкторские работы, а также на изготовление оборудования. 2. При высокой естественной влажности сырьевых компонентов предпочтение следует отдать полумокрому способу, который помимо реконструкции печи потребует строительства отделения фильтр-прессов. При использовании мягкого легко измельчаемого сырья целесообразно применять вариант IV.b – прямой подачи сырьевых компонентов в мельницу-сушилку. В этом случае отпадает необходимость строительства отделения фильтр-прессов. 3. Вариант IV.b может быть применен и для твердого сырья, но тогда в дополнение к молотковой мельнице-сушилке следует установить сепаратор и шаровую мельницу (тандем-схему) для выделения и домола крупки. Представляет определенный интерес схема по измельчению и сушке твердого сырья с использованием пресс-валкового измельчителя (роллер-пресса), статического-V и динамического сепараторов. 4. При ограниченности средств реконструкцию можно проводить в несколько этапов. Например, на первом этапе реализовать мокрый способ по варианту IV.a, произведя только реконструкцию печи с сушкой шлама в молотковой мельнице с использованием индивидуальной топки, а затем перейти на сухой или полу мокрый способы, проведя реконструкцию сырьевого отделения. 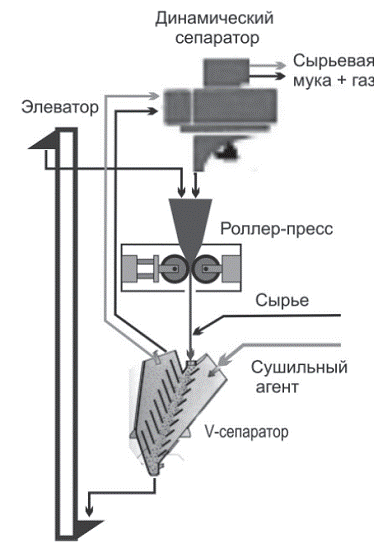
Рис. 6. Рациональная схема измельчения и сушки сырья при использовании твердых компонентов пониженной влажности C текущей ситуацией и прогнозом развития российского рынка цемента можно познакомиться в отчетах Академии Конъюнктуры Промышленных Рынков «Рынок цемента в России». Классен Виктор Корнеевич, БГТУ им. В. Г. Шухова www.newchemistry.ru
|