Параллельно с этим по инициативе ОАО «ТВЭЛ» на базе ОАО «Новосибирский завод химконцентратов» в 2006 г. было создано промышленное производство цеолитных катализаторов ароматизации мощностью до 150 т/год. На основе исходных данных в 2007 г. Проведено рабочее проектирование и начато создание первой в России промышленной установки ароматизации мощностью до 250 тыс. тн/год по сырью. В качестве первоочередного потребителя технологии может выступить ОАО «Сибур-Холдинг». Учитывая годовой дефицит в России ароматических углеводородов (около 500 тыс. тн/год), вряд ли эта установка окажется единственной. На базе вышеупомянутых цеолитных порошков были созданы катализаторы для одностадийной переработки широких фракций углеводородного сырья в высокооктановые бензины и зимнее (арктическое) дизельное топливо (процесс БИМТ) [4]. Эта технология удобна для использования в районах добычи углеводородного сырья, прежде всего там, где существуют транспортные проблемы с доставкой качественных моторных топлив. Технологическая схема процесса отличается простотой и включает собственно каталитический реактор и схему ректификации. Именно вследствие этого энергозатраты на получение моторных топлив по процессу БИМТ в 4 раза ниже, чем для традиционных технологий (табл. 4). Процесс позволяет использовать для получения качественных моторных топлив и высокосернистое сырье — в ходе процесса осуществляется гидрирование сернистых соединений до H2S, который выводят из системы традиционными способами. При пилотных испытаниях процесс на установке мощностью по сырью до 5 тыс. тн/год был получен высокооктановый бензин (с октановым числом от 80 до 95) и зимнее (арктическое) дизельное топливо с температурой замерзания до 55оС. Сейчас ведется строительство нескольких установок по процессу БИМТ мощностью от 50 до 200 тыс. тн/год. Каталитические технологии энергетического использования метансодержащих выбросов угольных шахт. На рис. 2 приведены данные по выбросам метана в мире и доле метана, приходящейся на угольные шахты. Как видно из рис. 2, за счет добычи угля в атмосферу поступает около 10% от всех антропогенных выбросов метана. При добыче угля разделяют выбросы метана, образующиеся при дегазации угольных пластов перед началом угледобычи, и метановые выбросы за счет вентилирования угольных шахт. Доля поступлений метана за счет дегазации пластов не превышает в общих метановых выбросах угольных шахт 15%, хотя концентрация метана в таких выбросах составляет от 30 до 70% об. Вентиляционные выбросы угольных шахт представляют собой воздух, содержащий 0,52,0% об. Метан и валовой выброс достигает 85% от всех метановых выделений угольных шахт. В России наиболее значимые выбросы метана связаны с шахтами Кузбасса. Здесь среднее содержание метана в угольных пластах достигает 20-25 м3/т угля, а удельные выбросы достигают 8 кг метана на 1 тонну добытого угля. Суммарные выбросы метана в атмосферу составляют 1,5-2,0 млрд. м3/год (притом, что в Кузбасс ввозится до 1,5 млрд. м3 природного газа и работает более 2000 котельных на угле). В целом же запасы метана в угольных пластах Кузбасса оцениваются более чем в 13 трлн. м3. 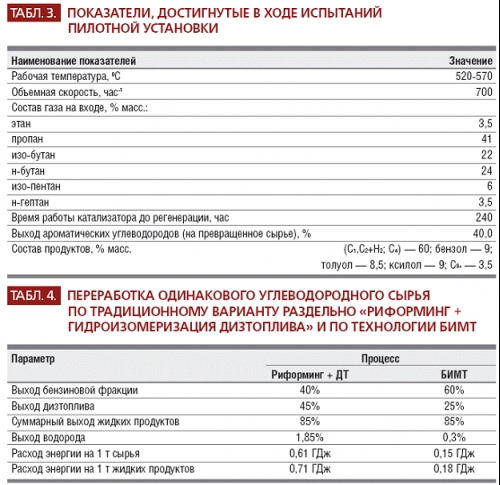
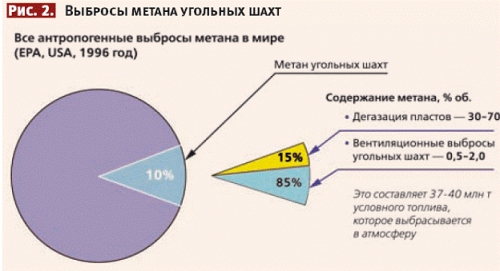
Для утилизации низкоконцентрированных метансодержащих выбросов угольных шахт разработан каталитический способ сжигания, основанный на периодическом (каждые 15-20 мин.) изменении направления фильтрации выбросов через слой неподвижного катализатора (рис. 3) [5]. Процесс осуществляют следующим образом. Метансодержащие вентиляционные выбросы через клапан подаются в реактор, где расположены предварительно нагретые от постороннего источника слои теплоаккумулирующего инертного материала и катализатора. В слое инертного материала вентвыбросы нагреваются, и на катализаторе происходит окисление метана до углекислого газа и паров воды, которое сопровождается выделением тепла. Часть тепла снимается в теплообменнике, а часть используется для нагрева до необходимой температуры в следующем по ходу реакторе слоя катализатора и инертного материала. Через каждые 15_20 мин. производят переключение клапанов, и исходные вентвыбросы подаются в реактор, который ранее был выходным. Такой процесс позволяет при концентрации метана всего 1% об. получить в центре реактора температуру около 1000°С и использовать такой режим для выработки горячей воды и/или технологического пара. Установки производительностью по очищаемым вентиляционным выбросам до 30 тыс. м3/ч и концентрации метана 1% об. позволяют вырабатывать до 40 т/ч теплофикационной воды с температурой до 115°С, что соответствует 1,8 Гкал/ч теплоты. Разработанный теплоагрегат предназначен для производства горячей воды со стандартными теплофикационными параметрами для бойлерной и бытовых нужд шахты. Его использование позволит обеспечить бесперебойное снабжение шахты теплом, без ущерба для нужд шахты производить ремонтные работы и сезонную профилактику основных теплостанций. Ниже даны характеристики теплоагрегата: 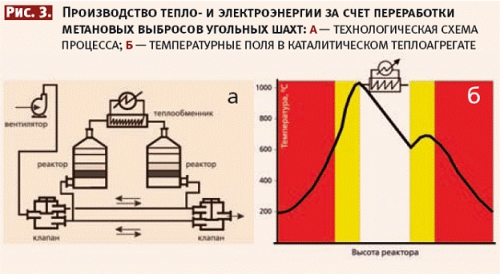
|