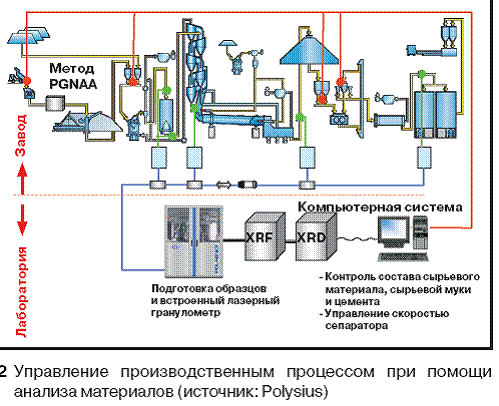
1. Сырьевой материал анализируется на входе в усреднительный штабель. Изменяемым параметром здесь является подача материала в дробилку. 2. Сырьевая мука анализируется как на входе, так обычно и на выходе из смесительного силоса. Изменяемый параметр здесь – загрузка сырьевой мельницы ленточным конвейером. Для управления печным процессом критична точно выверенная по времени информация о составе сырьевой муки, поступающей в теплообменник, т. е. и. На выходе смесительного силоса. Анализы на выходе мельницы слишком неточны для этой цели и производятся со слишком большим интервалом (время нахождения в силосе). 3. Анализ цемента производится на выходе цементной мельницы и на входе в силосы для хранения. Здесь изменяемым параметром является подача конвейером материала на вход цементной мельницы. 4. Анализ тонкости помола производится на выходе сепаратора мельницы. Он используется для управления скоростью сепаратора. В цементной промышленности лишь небольшое количество анализов выполняется строго в реальном масштабе времени (online), т. е. прямо в процессе без отбора образцов материала с передачей результатов на электронное устройство или компьютер для оценки. Примеры таких исследований – это анализ сырья, проводимый прямо в загрузочной системе усреднительного штабеля или в системе питания сырьевой мельницы. Небольшое количество заводов используют онлайн-анализ материала на выходе цементной мельницы. Онлайн-анализ на ленте конвейера производится циклами продолжительностью одна минута и охватывает весь слой материала. Для подавления шума в измерениях обычно интегрируются данные за 10 циклов, и таким образом получают изменяемый параметр, например, для входного материала на конвейере. Для целей управления процессом также одновременно регистрируется массовый расход, например, при помощи конвейерных весов параллельно с анализом материалов. Все другие анализы для управления процессом производятся inline, т. е. путем отбора образца материала и его обработки при помощи анализатора прямо на месте (atline) или в автоматизированной лаборатории. Для целей управления процессом рассматриваются только полностью автоматические системы. В случае использования автоматической версии материал транспортируется в капсуле по пневматической системе доставки от различных точек отбора образцов (зеленые линии на рис. 2) до лаборатории, снабженной автоматической системой подготовки материала и его последующего анализа (XRD, XRF). Результаты обрабатываются компьютерной системой, и определяются вышеупомянутые изменяемые параметры. В принципе, автоматизированная лаборатория способна обрабатывать характеристики образцов, отобранных из одной точки, каждые 2-3 минуты. При этом еще одну минуту занимает, доставка пробы при помощи пневматической системы со скоростью 10 м/сек на расстояние 600 метров. В стандартной системе разветвленных трубопроводов другие линии пневмодоставки на этот период времени блокируются. Для анализа горячей муки на входе вращающейся печи используется другой подход, так же, как и для анализа клинкера на выходе клинкерного холодильника. Эти анализы не используются напрямую для определения изменяемых параметров, а интегрируются для целей управления процессом в экспертную систему цементного предприятия. Анализ горячей муки может быть также использован для управления обходных потоков [2] цементного предприятия. Анализ клинкера (фазовый) дает базовые данные для настройки горелки. Однако эти переменные влияют на всю систему обжиговой печи, которая изначально управляется в соответствии с другими параметрами: расход топлива, температура зоны клинкерообразования и данные газового анализа. По этой причине результаты анализа горячей муки и клинкера подаются в систему в качестве дополнительных характеристических параметров. Учитывая комплексность и сложность входных параметров, здесь лучше использовать экспертную систему. Полностью автоматизированные лаборатории способны обрабатывать 15 образцов материала, полученного по пневматической линии доставки за час, что составляет четырехминутный аналитический цикл. Более жесткие требования могут быть удовлетворены при помощи установки параллельной лаборатории, однако в настоящее время значительного спроса на такую схему не существует. Это объясняется, в частности, тем, что анализ сырьевой муки проводится каждые 30 минут, анализ клинкера и цемента только каждый час, а анализ горячей муки каждые 1-2 часа. По этой причине управление процессом печной линии с последующим переделом помола цемента требует проведения в лаборатории только пяти анализов материала в час. Оставшееся время лаборатории можно использовать для измерения тонкости помола и других параметров качества. Для управления процессом измельчения при помощи анализов, производимых в режиме inline, получение изменяемых параметров более часто, чем каждые полчаса, пока не приводят к улучшению результатов процесса. На рис. 3 показаны результаты изменения качества стандартной извести, полученные при помощи анализа сырьевого материала. Наибольший разброс результатов наблюдается при проведении анализа в режиме offline с ручным отбором образцов. При проведении анализа в режиме inline с автоматическим отбором образцов и автоматической подготовкой материала зафиксирован незначительный разброс результатов, зависящий от количества проб в час. При отборе более двух образцов в час улучшения результатов не наблюдается. Вообще говоря, наилучшим средством для достижения оптимизации процесса является комбинация онлайновых и инлайновых методов анализа. Как следует из результатов анализа сырьевой муки, показанных на рис. 4, внутренняя управляющая цепь формируется онлайн-анализом, а входным материалом на конвейере манипулируют, рассматривая его в качестве изменяемого параметра. Внешняя цепь управления состоит из инлайновых лабораторных анализов. Такая схема может быть использована для разработки каскадных решений, где может быть также задействован смесительный силос для хранения сырьевой муки. Это позволяет значительно уменьшить уровень разброса по сравнению с контролем качества, отображенным на рис. 3. Однако это влечет за собой значительное увеличение количества оборудования и усложнение системы управления. |