Критический анализ этих публика¬ций показывает следующее: - Не понятно, для чего OSB высокая водостойкость? Ведь плиты OSB не пред¬назначены для изготовления лодок, яхт, причалов и т.п. Более того, при использо¬вании в строительстве плиты OSB не под¬вергаются прямому воздействию погод¬ных факторов и всегда закрываются тем или иным финишным материалом, ко¬торый и должен обладать очень высо¬кой водостойкостью. Что же касается ис¬пользования OSB в производстве мебели, то мебель эксплуатируется не в водной, а в воздушной среде. Из публикаций, посвященных плитам OSB3 и OSB4, выяснилось, что повышен¬ные прочность и влагостойкость дости¬гаются за счет химико-технологическо¬го приема 60-летней давности, а именно путем замены. В связующем части карбамидформальдегидной смолы на фенолформальдегидную и мел амин форм альде¬гидную, а также за счет использования смол смешанного состава, например фе¬нол-меламин-карбамид-формапьдегидную смолу. В результате этого к выделениям формальдегида из плит OSB OSB1 и OSB2 добавляются выделения фенола — высоко¬токсичного вещества, для которого в России установлена величина ПДК, равная 0,003 мг/м3. - Важно также отметить, что «водо¬стойкая» и токсичная плита OSBЗ имеет разбухание по толщине после выдержки в воде 24 часа 20%, а нетоксичная ЦСП марки ЦСП1 имеет разбухание по тол¬щине после выдержки в воде 24 часа 2% и при этом не называется «водостойкой». С точки зрения экологической безопас¬ности основная масса плит OSB не про¬ходит в России как материал для жилищ¬ного строительства по тем же причинам, что и плиты ДСП, а именно, плиты OSB не соответствуют критериям химической безопасности и критериям пожарной безопасности. Несоответствие критерию химической безопасности плит OSB отражено в ни¬жеприводимых официальных заключени¬ях различных контрольных органов Рос¬сийской Федерации. Из приведенных документов видно, на¬пример, что при 20°С образец ОСП (OSB) создает в воздухе испытательной каме¬ры в условиях, моделирующих эксплуа¬тационные, концентрацию формаль¬дегида 0.087 мг/м3, что в 29 раз выше ПДК. (0,003 мг/м3), при 40°С концентра¬ция формальдегида в воздухе достига¬ет 0,230 мг/м3. что в 76,6 раз выше ПДК^,.. Здесь уместно рассеять широко распро¬страненное, но не на чем не основанное убеждение, что покрытие древесно-плитных материалов, выделяющих формаль¬дегид, метанол, фенол, приводит к сни¬жению уровней выделений вредных веществ. На самом деле это не так. Де¬ло в том, что интенсивность выделений вредных веществ из плитных материа¬лов определяется величиной диффузион¬ной проницаемости поверхностного слоя материалов Р, а значение Р для поверх¬ностных слоев плитных материалов и от¬делочных материалов отличается очень мало. Здесь уместно напомнить, что даже такой труднопроницаемый материал, как железобетон, пропустил через свою тол¬щу и формальдегид и фенол, что вызва¬ло массовое отравление жильцов в так называемых «фенольных» домах в Моск¬ве, в которых полые железобетонные па¬нели были утеплены минераловатными плитами с фенолформальдегидным свя¬зующим. По горючести плиты OSB относятся к категории Г4, то есть полностью сго¬раемые. В связи с этим понятно, по¬чему в многочисленных рекламных и рекламно-технических проспектах и статьях ничего не говорится о горючести OSB, в то время как показатели пожар¬ной опасности материалов и конструкций являются важнейшими характеристиками экологической безопасности домов. Таким образом, выпускаемые в настоя¬щее время плиты OSB неприемлемы для строительства по критериям химической и пожарной опасности. В связи с этим уместно отметить, что некоторые фирмы, рассчитывающие продавать плиты OSB на российском рынке. И знающие о жестком ПДК для формальдегида в России, пошли на сле¬дующее ухищрение. Они стали использо¬вать в качестве связующего жидкие смо¬лы — продукт конденсации Бисфенолов с дифенилметан-диизоцианатом (фенол-дифенип-метан-диизоцианатный клей РМ01) — и в проспектах пишут, что «на¬ши плиты OSB не содержат формальде¬гида» При этом не упоминается, что фенол-диизиционатные связующие после отвер¬ждения выделяют фенол и органический растворитель, а при горении — набор высокотоксичных веществ, включая синиль¬ную кислоту. Приведенные факты показывают, что до настоящего времени ни одна из фирм, производящих ДПМ с синтетическими связующими, не ведет серьезных работ по радикальному снижению токсичности и горючести своей продукции. 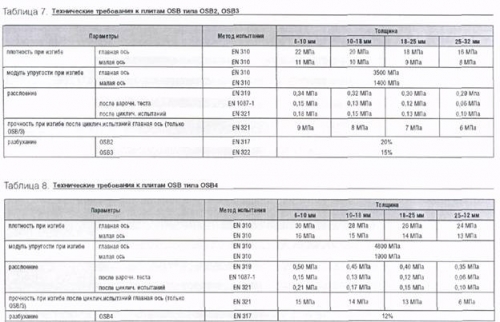
Плиты МДФ (мелкодисперсные фракции) Основным исходным компонентом для производства плит МДФ служит древес¬ное волокно, получаемое путем размола на мельницах-дефибраторах распаренной технологической щепы (ГОСТ 15815-83.9). На первой стадии процесса получают гру¬бое древесное волокно, которое подвер¬гают затем повторному размолу с получе¬нием тонкого древесного волокна. Готовое древесное волокно подается затем при помощи сжатого воздуха в пневмопровод, где происходит опыление его сначала па¬рафиновой эмульсией, а затем водным раствором карбамидформальдегидной смолы и в заключение водным раствором кислотного отвердителя, например, 20% раствором хлористого аммония. Распыление всех упомянутых компо¬нентов происходит в противоток древес¬ному волокну. Обработанное древесное волокно поступает затем в накопитель¬ный бункер, откуда поступает на формо¬вочную линию, где происходит форми¬рование первичного «ковра», который. Затем поджимается по ходу линии вал¬ками до нужной толщины, а на горячих лен точно-валковых прессах происходит окончательное уплотнение массы. И отверждение связующего. Охлажденная плита режется затем на нужные размеры. Ниже в таблице приводятся сравни¬тельные физико-механические характе¬ристики плит МДФ и ДСП. Плиты МДФ являются главным конку¬рентом ДСП, по сравнению с которыми обладают рядом преимуществ: • меньшее разбухание в воде: •лучшие показатели прочности: •больший выход готовой продукции по отношению к исходному сырью; •производство плит МДФ различных размеров и плотности, что позволяет по¬лучать плиты с заранее заданными свой¬ствами; • однородность и ровное распределе¬ние волокон по всей толщине, в отличие от других древесных плит, дают возмож¬ность проводить машинную обработку на лицевой поверхности и на краях без повреждения плиты; • гладкая, плотная поверхность МДФ без сучков облегчает процесс отделки, например ламинирование или непосред¬ственное нанесение рисунка. Первоначально плиты МДФ использо¬вались в качестве элементов мебели, од¬нако со временем произошло расшире¬ние областей применения МДФ. и прежде всего они нашли применение в изготов¬лении стеновых панелей, подоконников, основы для изготовления ламинирован¬ной половой доски (для этого используют одну из разновидностей МДФ - МДФ по¬вышенной плотности), дверей внутри по¬мещений, оконных рам. Вышеописанные достоинства плит МДФ действительно имеют место, одна¬ко, принимая во внимание их широкое распространение в строительстве, необ¬ходимо учитывать и недостатки с точки зрения экологической безопасности. Концентрация формальдегида в поме¬щениях, отделанных стеновыми панелями или половой доской на основе ламиниро¬ванных плит МДФ. создают в воздухе по¬мещения концентрации формальдегида в десятки раз превышающие ПДК. При этом уместно упомянуть об одном широко распространенном заблуждении, что, яко¬бы, ламинирование древесно-плитных ма¬териалов декоративной бумагой или бу¬мажно-слоистым пластиком существенно снижает уровень выделения формальдеги¬да. Все обстоит, как раз наоборот и де¬коративная бумага и бумажно-слоистые пластики пропитаны меламино-формальдегидными смолами, которые после отвер¬ждения сами выделяют формальдегид, до¬бавляя его к выделениям из плиты-основы. С точки зрения пожарной безопасности плиты МДФ относятся к категории го¬рючести Г4 и с этой точки зрения не соответствуют требованиям экологической безопасности к материалам жилищного строительства. Древесно-волокнистые плиты высокой плотно¬сти (твердые) (ДВП-Т, ДВП НТ) ГОСТ 4598-86 Основным сырьем для производства ДВП-Т является древесное волокно, получаемое размолом пропаренной техно¬логической щепы в одну или две стадии на дисковых мельницах. Наиболее рас¬пространенным является дефибраторный способ размола, в котором процес¬сы пропаривания и размола происходят в одном агрегате. В качестве связующего для получения ДВП-Т используют в ос¬новном фенолформальдегидные смолы в количестве от 0,6 до 4% массовых час¬тей от веса абсолютно сухого волокна. Для гидрофобизации волокна приме¬няют парафиновые эмульсии (1% от веса сухого волокна). В качестве альтернатив¬ного абсолютно нетоксичного связующе¬го используют альбумин (животный бе¬лок, получаемый из крови животных). Однако в настоящее время ДВП-Т с аль¬буминовым связующим не производятся. В качестве осадителей парафина и свя¬зующего на волокнах используют серно¬кислый алюминий или серную кислоту. В мировой практике существуют два основных способа производства ДВП-Т мокрый и сухой. Принципиально они от¬личаются тем, что по мокрому способу нанесение всех необходимых компонен¬тов на древесное волокно осуществляет¬ся в водной среде, а по сухому способу в воздушной среде методом пневмораспыления. Недостатком мокрого способа является необходимость использования большого количества воды и значитель-ные затраты на очистку сточных вод, осо¬бенно от остаточного фенола. В связи с этим мокрый способ производства ДВП-Т за рубежом практически не используется,производство по сухому способу имеет свои проблемы.
|