В зависимости от содержания формальдегида плиты изготовляют трех классов эмиссии, указанных в табл. 5. В условном обозначении плит указывают: марку; сорт; вид поверхности (для плит с мелкоструктурной поверхностью); степень обработки поверхности (для шлифованных плит); гидрофобные свойства (для плит повышенной водостойкости), класс эмиссии формальдегида; длину, ширину и толщину в миллиметрах; обозначение настоящего стандарта. Примеры условных обозначений плит марки П-А первого сорта с мелкоструктурной поверхностью шлифованных класса эмиссии Е1 размерами 3500x1750X15 мм: П-А, I, М. Ш, Е1, 3500X1750X15, ГОСТ 10632-89; То же, плит марки П-Б второго сор¬та с обычной поверхностью, нешлифованных, класса эмиссии Е2, размерами 3500Х 1750 х 16 мм: П-Б, II, Е2, 3500x1750x16, ГОСТ 10632-89. На кромку плиты наносят в виде четкого штампа темным красителем маркировку, содержащую: наименование и (или) товарный знак предприятия-изготовителя, мар¬ку, сорт, вид поверхности и класс эмиссии, дату изготовления и номер смены. Плиты, предназначенные для использования в районах Крайнего Севера и приравненных к ним районах, упаковывают по ГОСТ 15846. Плиты перевозят всеми видами транспорта в соответствии с Правилами перевозки грузов, действующими для данного вида транспорта, и техническими условиями погрузки и крепления грузов МПС с обязательным предохранением их от атмосферных осадков и механических повреждений. Плиты хранят в закрытых помещениях в горизонтальном положении в штабелях высотой до 4,5 м, состоящих из стоп или пакетов, разделенных брусками-прокладками толщиной и шириной не менее 80 мм и длиной не менее ширины плиты, или поддонами Технология производства ДСП включает следующие стадии: 1. Подготовка и распиловка круглого леса. 2. Высокоскоростное изготовление щепы. 3. Сортировка щепы. 4. Подача щепы в смеситель, например, барабанного типа. 5. Осмоление щепы карбамидо-феноло или меламиноформальдегидной смолой. 6. Введение в смеситель водного рас¬твора отвердителя для смолы и специальных добавок. 7. Формирование «ковра" из осмоленной стружки. 8. Термопрессование набранных ковров на многоэтажном прессе при температуре 165-175°С в течение 5-7 мин. 9. Охлаждение и выгрузка плит. 10. Упаковка готовых плит и складирование. Соответствие ДСП требованиям эколо¬гической безопасности для материалов, применяемых в жилищном строительстве: • Химическая безопасность: Ни одна из разновидностей ДСП. Изготавливаемых в России, не соответствует требованиям химической безопасности, прежде всего из-за постоянного в течение всего времени эксплуатации выделения в воздух помещений формальдегида. Даже при использовании ДСП класса Е1 превышение концентрации формальдегида в воздухе помещений будет многократным по сравнению с ПДКсс в России 0,003 мг/мЗ. Именно по этой причине Минздрав СССР в конце 80-х годов XX века официально запретил использование ДСП (а также фанеры) в жилищном строительстве. • Физическая безопасность: Никаких претензий к ДСП с точки зре¬ния физической безопасности не имеется. • Биологическая безопасность: В сухих помещениях ДСП соответству¬ют критерию биологической безопасности. В помещениях с повышенной влаж¬ностью могут появляться грибковые образования, • Пожарная безопасность: Подавляющая часть выпускаемых в России ДСП относится по горючести к классу Г4. и без специальной противопожарной обработки не может быть ис¬пользована в жилищном строительстве. Таким образом, по двум важнейшим критериям экологической безопасности — химической и пожарной, российские ДСП не могут быть использованы в жилищном строительстве. Для серьезной реабилитации всех разновидностей ДСП необходимо: - вводить в состав ДСП детоксиканты, необратимо поглощающие формальдегид в течение всего срока эксплуатации со скоростью, превышающей скорость отщепления формальдегида от отвержденной карбамидоформальдегидной смолы; - вводить в состав ДСП эффективные антипирены постоянного действия. - при строительстве жилых помещений обрабатывать внутреннюю поверхность ДСП детоксицирующей и огнезащитной грунтовкой, снижающей как минимум в 10 раз уровень выделения в воздух формальдегида и полностью поглощающей фенол. Обработанная ДСП переходит по горючести из класса Г4 в класс П.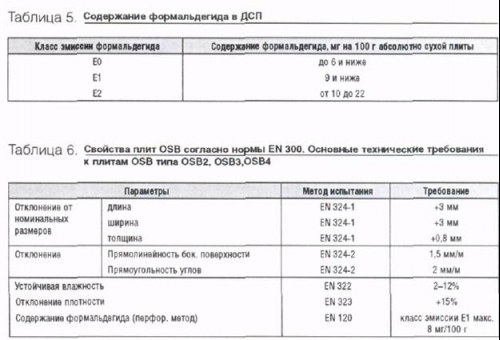 Ориентированные стружечные плиты ОСП (OSB-плиты) Плиты ОSB существенно отличаются от плит ДСП, прежде всего размером и порядком укладки стружки (щепы) в стружечном ковре перед прессованием. Диапазоны размеров стружки (щепы) для ОЗВ составляют: длина 75-150 мм, ширина 10-25 мм, толщина 0,50-0,75 мм. Осмоленная щепа с указанными параметрами при помощи специальных шнековых укладчиков раскладывается так, что в верхнем слое щепа располагается вдоль длины плиты, в среднем слое — поперек и в нижнем слое снова вдоль длины плиты. Набранный таким образом ковер подвергается горячему прессова¬нию при температурах 165-175°С в мно¬гоэтажных прессах. Принцип укладки щепы в плитах ОЗВ полностью аналогичен принципу укладки фанеры, однако производительность процесса значительно выше в технологии, а также значительно больший выбор исходного древесно¬го сырья. Прочность при изгибе плит OSB со средней плотностью 685 кг/куб.м. составляет около 45 МПа (прочность фанеры аналогичной плотности составляет в среднем 57 МПа). Начало производства плит относится к 1978 году (США), а к 2000 году в США производство плит OSB по объему сравнялось с производством фанеры. В последние годы процесс производства плит OSB значительно усовершенствовали, и производительность труда еще больше увеличилась за счет замены периодического процесса горячего прессования на непрерывный процесс с использованием ленточных процессов. Современная технология производства плит OSB. В качестве основно¬го сырья для изготовления плит OSB используется круглый лес сосны. Окорка круглого леса осуществляется вне производственных цехов при помощи окорочного барабана, в котором можно обрабатывать стволы длиной до 2,5 м. Окоренные стволы направляются в цех на стружечные станки с ножевыми кольцами. Стружка для наружного слоя изготавливается длиной 100 мм, толщиной 0,6 мм и шириной 20 мм. И для внутреннего слоя — шириной 15 мм. По ленточному транспортеру длиной 250 м стружка направляется к бункеру сырой стружки для промежуточного хранения. Барабанная сушилка нагревается прямым нагревом при помощи горячего воздуха, который вырабатывается на газомасляной горелке. Испарительная мощность сушилки составляет 28 т/час. Два параллельных сита НотЬак барабанного типа отделяют полезное сырье от мелких фракций. На выходе из сепаратора более широкая стружка для наружного слоя отделяется от более узкой стружки для внутреннего слоя при помощи простого двухходового распределителя. Затем в одном смесителе для внутреннего слоя и двух смесителях для наружного слоя происходит нанесение клея. При изготовлении плит OSB-2 процентное содержание клея составляет 11% {относительно абсолютно сухого веса стружки) для стружки наружного слоя и 2% для стружки внутреннего слоя. Причем для наружного слоя используется клеевая смесь на основе карбамидной или меламиновой смолы, а для стружки внутреннего слоя - фенол-дифенил-метан-диизоцианатный клей РМ01. Для соблюдения требований норм для плит OSB-3 для стружки наружного слоя используется смесительный конденсат МУРР (13-14%), а для внутреннего слоя — клей (4%). Фор¬мирующая станция имеет две насыпные головки с дисковыми вальцами для на-ружного слоя и одну насыпную голов¬ку с камерными вальцами для внутреннего слоя. Максимальная ширина насыпки составляет 2.93 м. Прибор-металлоискатель соединен с управляющей заслонкой ошибочной насыпки. Первый в Европе пресс непрерывного действия фирмы «Диффенбахер». для производства плит OSB, имеет длину 34 м с возможностью удлинения на 10 м, Ширина стальной ленты - З м, толщина - 3 мм. Стальные ленты нагреваются котлом мощностью 8 МВт при помощи термомасла до тем-пературы 220°С. В передней зоне уплотнения давление прессования достигает 5 Н/мм1. Расчетное время отвердения составляет 9 секунд на каждый миллиметр толщины плиты. Плиты изготавливаются толщиной от 6 до 40 мм. Пыль и отработанный пар после пресса удаляются вентилятором влажным способом. Участок транспортировки «сырых» плит начинается на установке раскроя на базовый размер плиты (от 3 м до 6,3 м). После прохождения устройства распознавания расслоений плиты направляются на два веерных охладителя, установленных последовательно друг за другом, После охлаждения плиты укладываются в штабели. Поперечные транспортеры направляют плиты на участок разборки штабелей. Затем 5-пильными агрегатами осуществляется продольный и попереч¬ный раскрой плит на 4 плиты необходи¬мой длины и ширины. За последние три года в рекламно-технических публикациях, посвященных плитам OSB, участилось упоминание так называемых водостойких OSB. к которым относятся OSBЗ и OSB4. обладающих большей прочностью и водостойкостью по сравнению с плитами OSB OSB1 и OSB2. Авторы многих публикаций наибольшее внимание уделяют OSBЗ, которые сочетают высокую прочность, водостойкость (% разбухания в воде за 24 часа) и приемлемую цену. Некоторые авторы прогнозируют бурное развитие производства OSBЗ.
|