Все фанеры с карбамидформальдегидным связующим выделяют в воздух помещений формальдегид СН,0 и метанол СН,ОН. Формальдегид является канцерогенным веществом и в этом качестве внесен в список канцерогенов Всемирной организации здравоохранения (ВОЗ) при ООН. Метанол также относится к высокотоксичным веществам. Достаточно широко известно, что по европейским стандартам ДПМ с формальдегидсодержащими связующими по содержанию формальдегида в мг/100 г ДПМ делятся на три категории: ЕО — 6 и менее мг/100 г; Е1 — от 9 до 7 мг/100 г; Е2 — от 10 до 20 мг/100 г. Лучшие виды фанер, выпускаемых в Российской федерации, соответствуют всего лишь классу Е2. В странах Восточной и Западной Европы выпускаются фанеры класса Е1, получаемые за счет применения КФ-смол с резко пониженным содержанием формальдегида и метанола. Однако для широкого применения в строительстве не подходит ни фанера Е1, ни тем более Е2. Причины здесь две: 1. Отвержденные КФ-смолы. независимо от любых обстоятельств, постоянно отщепляют формальдегид, и уровень его выделения в воздух помещений повышается при повышении температуры и влажности. В России официально установлено значение ПДК, для формальдегида, равное 0,003 мг/м-' воздуха, — это самое жесткое ПДК, в мире, что вызвано доказанной канцерогенностью формальдегида. В силу этого, любая фанера, использованная для чернового пола или отделки стен, потолков, будет создавать в помещении концентрацию формальдегида в 10 и бо¬лее раз превышающую 0.003 мг/м:. Для того чтобы вернуть фанеру как отделочный материал в строительство жилья, необходим целый ряд серьезных мер по улучшению качества смолы и введение в состав клеев компонентов, активно поглощающих (необратимо) формальдегид весь срок эксплуатации фанеры, то есть осуществить комплекс технологических и компо-зиционных нововведений, сводящихся к радикальной детоксикации фанеры. Что же касается бакелитовых фанер вышеуказанных марок, то они еще более токсичны, чем фанеры на основе. Карбамидоформальдегидных связующих, так как помимо формальдегида и метанола выделяют в воздух высокотоксичный фенол, для которого ПДК^. для атмосферного воздуха равно 0,003 мг/м', Наличие в воз¬духе помещений одновременно формальдегида, метанола и фенола превращает помещение в настоящую камеру по отравлению людей. Применение бакелизированных фанер для внешней отделки деревянных домов также не несет ничего хорошего, так как пары вышеуказанных ядовитых веществ активно проникают в помещение за счет диффузии через ограждающую конструкцию и через форточки, окна, кондиционеры, двери и т.д. Радикально снизить уровень выделения вредных летучих веществ из фанер можно как за счет введения в клеевую композицию детоксикантов, так и за счет обработки поверхности фа¬нер грунтовкой. Подавляющая масса производимой в РФ фанеры относится к ка¬тегории горючести Г4, то есть относится к полностью сгораемым материалам. Только одно предприятие в РФ выпускает трудногорючую фанеру класса Г2, применяемую в вагоно- и судостроении. Согласно приведенным в начале статьи принципам экологической безопасности строительных материалов и жилья в целом, применение материалов класса горючести Г4 в жилье недопустимо. В то же время введение в состав клеев для фанры эффективных отечественных антипиренов (одновременно являющихся детоксикантами}, а также обработка шпона после выравнивающих вальцев водными растворами высокоэффективных и нетоксичных антипиренов позволяют с небольшими изменениями технологии получать фанеру класса горючести Г2 и. при желании, П с одновременным многократным снижением уровня выделения формальдегида. В настоящее время в России выпускается около 2 млн.кв.м. фанеры, из которых 65-70% идет на экспорт. В общем мировом производстве фанеры доля России составляет примерно 4%. Однако за последние 3 года объем экспорта российской фанеры в США и, особенно, в Западную Европу стал заметно сокращаться из-за высокой токсичности и несоответствия стандарту Е1. В первую очередь это коснулось высокотоксичных фанер типа ФСР, от которых западные потребители отказываются. При этом важно и интересно отметить, что российские предприятия несут серьезные убытки от сокращения или невозможности экспорта фанеры (равно как и ДСП и МДФ), но не желают вкладывать ни рубля в работы по созданию малотоксичных древесно-плитных материалов класса Е1 и ЕО. Древесно-стружечные плиты (ДСП, ДСтП) ГОСТ 10632-89 Древесно-стружечные плиты (ДСП) впервые стали производиться в Германии в конце 30-х годов XX века, а побудительной причиной разработки и организации промышленного производства стала потребность в рациональном использовании отходов деревообработки, тонкомера, низкосортной древесины В СССР первое производство ДСП было организовано в 1955 году, а массовое производство на импортном оборудовании — с 1957 года. Через 50 лет. в 2007 году, объем производства ДСП в России составил немногим более 5 млн.кв.м. При современном оборудовании в принципе возможно производство ДСП толщиной от 8 до 40 мм, но преобладающий объем составляют ДСП толщиной от 13 до 26 мм. Физико-механические показатели ДСП, в зависимости от марки и толщины, при¬ведены в табл. 2. По структуре плиты подразделяются следующим образом: • по конструкции — однослойные, трехслойные и многослойные; • по физико-механическим показателям — на марки П-А и П-Б; • по качеству поверхности — на I и II сорта; • по виду поверхности — с обычной и мелкоструктурной (М) поверхностью; • по степени обработки поверхности — на шлифованные (Ш) и нешлифованные; • по гидрофобным свойствам — с обычной и повышенной (В) водостойкостью; • по содержанию формальдегида — на классы эмиссии ЕО. Е1. Е2. По показателям прочности и жесткости древесно-стружечные плиты приближаются к древесине хвойных пород. Плиты выпускаются малой плотности - менее 550 КГ/куб.м., средней - 550-750 кг/куб.м., высокой - более 750 кг/м3. По виду используемых частиц плиты могут быть из специально заготовленных древесных частиц, из стружки, из опилок. Плиты с мелкоструктурной и шлифованной поверхностью пригодны для облицо¬вывания пленочными и полимерными материалами. Размеры плит должны соответствовать размерам, указанным в табл. 3. 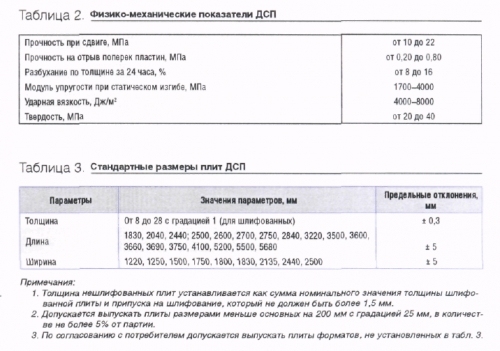
Отклонение от прямолинейности кромок не должно быть более 2 мм. Отклонение от перпендикулярности кромок плит не должно быть более 2 мм на 1000 мм длины кромки. Перпендикулярность кромок может определяться разностью длин диагоналей пластин, которая не должна быть более 0,2% длины плиты. В условиях эксплуатации количество химических веществ, выделяемых плитами, не должно превышать в окружающей среде допустимых концентраций, утвержденных органами санитарно-эпидемиологического надзора для атмосферного воздуха. Качество поверхности плит должно соответствовать нормам, указанным в табл. 4. 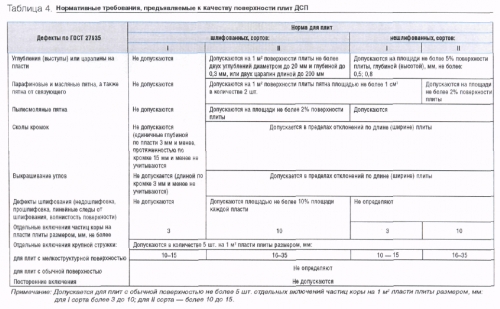
|