Так как получаемый из реакторов метанол содержит достаточно большое количество примесей, необходим процесс ректификации, что в свою очередь также требует энергозатрат. Суммируя всё вышеизложенное, можно сделать вывод, что подобные технологии применимы только в случае крупных производств (не менее 500 тысяч тонн в год). Крупнотоннажное производство предполагает создание предприятия с развитой инфраструктурой, социальной сферой, мощным энергохозяйством. Малотоннажные промысловые установки требуют принципиально -иного подхода к концепции построения, например блочно-модульное исполнение, позволяющее заводу-изготовителю выпускать отдельные модули в виде законченных изделий высокой заводской готовности. Монтажные работы на месте строительства, в основном, сводятся к монтажу блоков, прокладке внешних коммуникаций и к соединению разъёмов. Всёвозрастающий интерес в России и во всём мире к децентрализованному производству ценных жидких продуктов из природного или попутного нефтяного газа, а также ужесточение экологических требований при добыче нефти дало толчок для разработки новых высокоэффективных технологий, связанных с модернизацией первой, наиболее энергозатратной и дорогой, стадией получения синтез-газа. Во многих странах ведутся работы по осуществлению одностадийного процесса синтеза метанола непосредственно из метана, минуя стадию получения синтез-газа или совмещая с ней. Существует ряд разработок, где в отличие от традиционной, рассмотренной выше энергопотребляющей технологии, предлагается использовать реакцию частичного окисления метана при высокой температуре и недостатке кислорода, что сопровождается большим тепловыделением, а процесс может быть некаталитическим, что значительно удешевляет и упрощает его. Инженерное воплощение этих идей предлагается совершенно различным. Например, в качестве исходных агрегатов для создания генераторов синтез-газа используется энергетические агрегаты, в которых могут быть получены высокие температуры. К ним относятся ядерные реакторы, ракетные двигатели, газовые турбины, модифицированные дизельные двигатели и др. На протяжении последних десятилетий во многих организациях проводились теоретические и опытно-исследовательские работы по возможности использования ракетного двигателя (плазмо-химические реакции) в качестве генератора синтез-газа, далее получения из него диметилового эфира и высокооктанового топлива. На экспериментальной установке Приморского НТЦ были получены замечательные результаты [6], на наш взгляд этот метод имеет большие перспективы, но до промышленного внедрения пока далеко. Ведутся разработки плавучих энерго-технологических комплексов, в которых в качестве генератора синтез-газа используется охлаждающий контур ядерного реактора четвертого поколения Другим примером генератора синтез-газ (ГСГ) является конвертер на основе модифицированного газодизеля. Принципиальная возможность этого метода была предложена в пятидесятые годы прошлого века. Затем проводились исследования, как в нашей стране, так и за рубежом. В Институте Высоких Температур (ИВТ) РАН была создана опытно-промышленная установка, на которой синтез-газ получали на выхлопе газодизеля, а затем в реакторах с применением катализаторов получали метанол, высокооктановый бензин или диметиловый эфир (Рис.3). Научно-исследовательские работы, выполненные в Экспериментальном комплексе "Новые энергетические технологии" ИВТ РАН позволили создать теоретическую базу для промышленной установки, в которой в качестве ГСГ применён модифицированный тепловозный газодизель Д-49 (Рис.4). 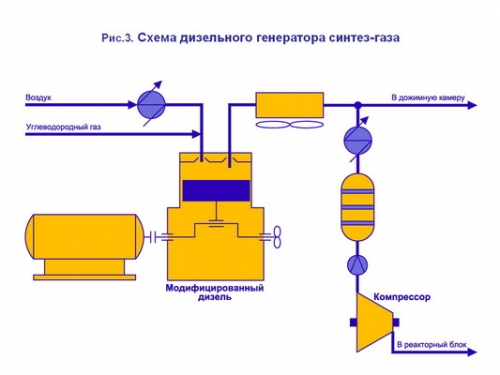
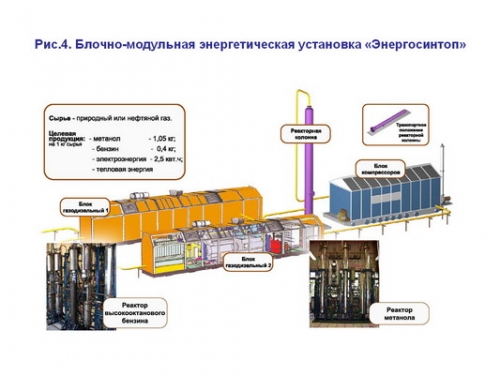
Преимуществом такого ГСГ является его компактность, многофункциональность, т.к. к валу газодизеля через магнитную муфту прикреплен электрогенератор, что делает такую установку привлекательной в качестве промысловой установки, утилизирующей природный или попутный нефтяной газ и генерирующей тепловую и электрическую энергию. Для организации промышленного выпуска таких установок необходимо решить целый ряд научных и организационных проблем. Наиболее привлекательным из всех перечисленных методов получения синтез-газа является метод прямого гомогенного окисления углеводородов кислородом. Но за кажущейся простотой скрыты сложные разветвлено- цепные реакции. Научная основа метода прямого гомогенного окисления - кинетика разветвлено-цепных процессов, созданная и успешно развиваемая учеными школы академика Н.Н.Семенова. Многие выдающиеся представители этой школы академики В.Н.Кондратьев, В.В.Воеводский, Н.М.Эмануэль, Н.С.Эниколопов внесли большой вклад в изучение процессов окисления углеводородов. Процесс состоит из трёх основных стадий. • Короткая начальная стадия является разветвленной цепной реакцией с явно выраженной S-образной кинетической зависимостью роста концентрации радикалов от времени. • Вторая стадия представляет собой квазистационарную разветвлено-цепную реакцию с квадратичным обрывом цепей, медленным накоплением промежуточных продуктов и медленным разогревом. • На третьей стадии происходит быстрое самоускорение за счет разветвления на продуктах реакции и теплового разогрева. При выполнении комплекса экспериментальных исследований неполного фазного окисления метана, этана и их смесей при высоких давлениях работы проводились на установках различного масштаба с расходом газа от нескольких литров до 1000 м3/ч и реакторами диаметром от 5 до 30 мм. Изучали влияние материала поверхности реактора, в частности, покрывали стенки из коррозионно-стойкой стали кварцевыми вставками. Работали как с заранее перемешанными газами, так и при смешении их только в самом реакторе. В качестве окислителя применяли как кислород, так и воздух. Полученные результаты хорошо согласуются между собой и с результатами кинетического моделирования процесса. Это дает надежду на отсутствие проблем при масштабировании процесса и практически полной воспроизводимости результатов при сопоставимых условиях, что было подтверждено при испытаниях опытно-промышленной установки на Шебелинском газоконденсатном месторождении (Рис. 5).
|