Практически решены все технические вопросы, связанные с применением метанола на автотранспорте. Существуют естественные биологические процессы разложения метанола, что выгодно отличает его от сложных (метил-трет-бутилового, этил-трет-бутилового) эфиров и других соединений, предлагаемых на роль альтернативного топлива. Важным преимуществом метанольных топлив является возможность их использования как в двигателях с искровым зажиганием, так и в газодизелях. Разработаны системы, в которых для получения синтез-газа, а затем метанола или моторных топлив используется энергия выхлопных газов газодизеля. Наиболее реальные проекты электромобиля основаны на топливных элементах, питаемых непосредственно метанолом, либо водородом, получаемым из метанола на борту автомобиля.
За рубежом и в нашей стране накоплен большой опыт, который показывает, что при соблюдении правил эксплуатации опасность использования метанола не превышает опасности использования традиционных нефтяных топлив, а токсичность его паров примерно в три раза ниже, чем высокооктанового бензина. В настоящее время метанол - один из наиболее крупнотоннажных химических продуктов, на его долю приходится 9% мирового потребления нефтехимической продукции, и интерес к метанолу, как основе газохимии возрастает с каждым годом. Проблема производства и транспортировки метилового спирта будет обостряться по мере продвижения основных месторождений нефти и газа России на восток и в заполярные регионы, а также в связи с ростом удельного веса мелких газовых месторождений с запасами газа менее 10 млрд.м3 (к этой категории могут быть отнесены около 70% месторождений стран СНГ). Уникальные условия России как-то: обилие нефтегазовых месторождений, удаленных от основных транспортных артерий и центров промышленной инфраструктуры с крупнотоннажным производством метанола; суровый климат, требующий большого количества метанола для предотвращения гидратообразования при добыче и транспортировке природного газа; высокая стоимость доставки метанола в районы промыслов - диктуют необходимость создания ориентированной на районы газо- и нефтедобычи малотоннажной технологии переработки углеводородов в метанол. Создание малотоннажной газохимии на основе попутного газа или низконапорного природного газа из собственных источников сырья открывает возможность удовлетворить местные потребности в метаноле, моторном топливе, сухом газе. Потребность в метаноле, например, в районе Уренгоя, составляет примерно 100 тысяч тонн в год. Доставка метанола на промыслы Крайнего Севера как минимум удваивает его стоимость, а для некоторых месторождений, в частности Ямала, зачастую вообще отсутствует возможность его доставки. Организация в условиях газо и нефтесборных пунктов или газоперерабатывающих заводов мало- и среднетоннажных производств, основанных на технологиях превращения природного и попутного нефтяного газа в жидкие продукты (GTL-технологии) позволяет решать помимо чисто экономических, экологические проблемы, связанные с транспортом и хранением огромного количества метилового спирта, сократив потребность только в металле на трубопроводный транспорт более чем в 2,5 раза. Производство и применение метилового спирта непосредственно на месторождениях позволит сократить количество вредных выбросов в атмосферу при сжигании на факелах попутного нефтяного газа, а также за счет перевода двигателей внутреннего сгорания на метиловый спирт или его производные. Дополнительный экономический эффект достигается за счет сокращения транспортных расходов, расходов на хранение, а также за счет более низкой себестоимости исходного сырья в пунктах добычи, чем в местах традиционного производства метилового спирта. Сравнительный анализ методов получения метанола Рассмотрим два основных направления получения метанола из природного или попутного нефтяного газа: непрямую конверсию через синтез-газ и прямое окисление. Примером непрямой конверсии газа являются широко используемые промышленные процессы синтеза метанола и аммиака. В настоящее время промышленное производство метанола основано на его каталитическом синтезе из окиси углерода и водорода (синтез - газе). По отработанной технологии производства метанола из природного газа каталитическую конверсию метана осуществляют при повышенном давлении и высокой температуре. В качестве окислителя используется кислород в водяном паре. В зависимости от их сочетания различают: " паровую конверсию; " пароуглекислотную конверсию; " парокислородную конверсию; " парокислородуглекислотную конверсию. Существующие мощности по производству метанола, как правило, базируются на традиционных технологиях двух и более стадийных процессов. Производство метанола по этой технологии состоит из следующих стадий: Риформинг ? Компримирование ? Синтез метанола ? Ректификация метанола. Риформинг На первой, наиболее сложной и дорогостоящей стадии, осуществляется паровая, парокислородная или пароуглекислотная конверсии метана в присутствии катализатора (Рис.2) при температурах 700-900С и давлении 2-3 МПа. Происходит это в высокотемпературных трубчатых печах из дорогостоящей аустенитной стали. Процесс проходит с высоким потреблением энергии. К этому необходимо добавить энергозатраты на производство кислорода и пара. 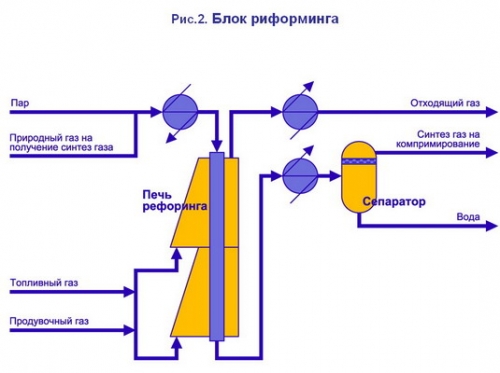
Компримирование Полученный синтез-газ после охлаждения и очистки в зависимости от технологической схемы дальнейшей переработки синтез-газа в жидкие продукты компримируется до 8?30 МПа центробежными компрессорами с приводом от паровой турбины, чтобы более эффективно использовать энергию отходящего после реформинга пара, хотя могут применяться и другие технические решения. Синтез метанола На второй стадии осуществляется конверсия полученного синтез-газа в метанол в реакторах в присутствии катализатора. После первой стадии получается практически чистый синтез-газ, однако каталитический процесс синтеза метанола происходит с высоким выделением тепла, отвести это тепло существующими способами и тем самым обеспечить равномерное распределение температур во всём объёме реактора весьма сложно. А именно это требование необходимо для достижения высокой степени селективности конверсии с целью получения чистого продукта. На практике за один проход удаётся достигнуть степень конверсии углеводородов на уровне (8-12)%, для ее повышения приходится вводить многократную рециркуляцию синтез-газа, что связано с энергозатратами. |