Более экономичны по расходу топлива и простоте конструкции печи, работающие по пересыпному способу на короткопламенном топливе (антрацит или тощий каменный уголь). Производительность шахтных пересыпных печей составляет 100-110 тонн в сутки. К недостаткам пересыпных печей относится загрязненность извести золой топлива. Более чистая известь получается в шахтных печах с выносными топками, работающих на длиннопламенном топливе (бурый уголь, дрова, торф), и в печах газовых. Однако эти печи имеют несколько меньшую производительность. В шахтных печах можно обжигать только твердые породы (известняк, мрамор и др.), а во вращающихся — как твердые породы, так и шламы мягких пород, например мела. Основная задача при обжиге - обеспечение максимальной степени декарбонизации СаСО при минимальной температуре. Повышение температуры ускоряет реакцию разложения карбоната кальция, но излишне высокая температура обжига негативно сказывается на качестве продукта, так как развивается явление «пережога». Наибольшее распространение для производства извести получили шахтные печи, высота которых достигает 20 м. Шахтные печи различают по виду применяемого в них топлива и по способу его сжигания. В пересыпных печах твердое топливо подается вместе с сырьем и сгорает между кусками обжигаемого материала. Здесь применяют топливо с малым содержанием «летучих» — антрацит, кокс и тощие сорта каменного угля, дающие при горении короткое пламя. В печах с выносными топками последние расположены по внешнему периметру печи. В них сжигается твердое топливо (полностью или частично) и образующиеся горячие газы поступают в зону обжига. Применяют длиннопламенное топливо с высоким содержанием «летучих», а также торф, дрова, горючие сланцы. В газовых печах топливом чаще всего служит природный газ, который подается непосредственно в шахтную печь и сжигается в слое материала. Вращающиеся печи позволяют получать мягкообожженную известь высокого качества из мелкокускового известняка и из мягких карбонатных пород (мела, туфа, известняка-ракушечника), которые нельзя обжигать в шахтных печах из-за склонности этих материалов к «зависанию» в шахте, приводящему к нарушению технологии обжига. Длина известеобжигательных вращающихся печей составляет 30 — 100 м при диаметре 1,8 — 3 м, производительность достигает 400 — 500 т/сут., что в 2-4 раза выше, чем у шахтных печей. Одно из важнейших технологических преимуществ обжига извести во вращающихся печах — малое время прохождения материала от места загрузки до выхода из печи, что обеспечивает оперативность управления процессом. Вращающиеся печи обеспечивают компактность технологической схемы, позволяют автоматизировать процесс и снизить капитальные затраты на строительство цехов. Во вращающихся печах может быть получена известь высокого качества обжигом при средних и достаточно высоких температурах. Из-за малого времени пребывания материала в печи, опасность пережога в них минимальна. При этом известь значительно более однородна по составу и содержит меньше примесей. Рис 1.2. Схема обжига молотого известняка во вращающейся печи 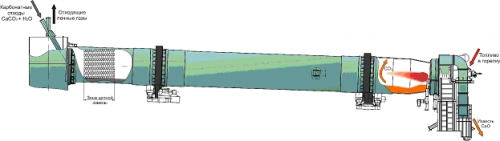
Значительно снижает качество комовой извести наличие в ней негасящихся кусков (недожог) и кусков, гасящихся медленно (пережог), которые могут образоваться из-за неравномерного распределения температур в известеобжигательных печах или неравномерного содержания в сырье примесей (например, углекислого магния). Негашеную комовую известь нельзя непосредственно использовать в качестве вяжущего, ее требуется дополнительно измельчать либо размолом на мельницах (получается негашеная молотая известь), либо гашением водой (гашеная известь). Для облегчения помола в мельнице комовую известь предварительно дробят до зерен размером 15 — 20 мм. Помол осуществляют обычно в шаровых одно- и двухкамерных мельницах, но возможно применение также валковых и роликовых мельниц, а при необходимости получения очень тонкого порошка используют вибромельницы. Наряду с бездобавочной известью выпускают также известь с активными минеральными добавками (золы, шлаки), в последнем случае их вводят в мельничный агрегат, где происходит совместное измельчение и одновременно перемешивание. Тонкость помола негашеной извести оказывает существенное влияние на ее свойства, особенно при наличии «пережога». В соответствии с требованиями ГОСТ негашеную известь следует измельчать до тонкости, при которой остаток при просеивании пробы через сита № 02 и № 008 должен быть соответственно не более 1,5 и 15%. Обычно заводы выпускают известь, характеризующуюся остатками на сите № 008 до 2-7%, что примерно соответствует удельной поверхности 3500-5000см /г.
|