Для устранения указанных недостатков были созданы агрегаты, способные выполнять несколько функций, по типу "два в одном", "три в одном" и т. д. К таким машинам можно отнести мельницы-сушилки зарубежных и российских фирм, таких как "Novorotor" (Германия), "Finpulva" (Финляндия), "Титан" и "Баскей" (Россия), новые обезвоживающие грохота фирмы "Kroosh Technologies Ltd." (Израиль) и др. На основе использования многофункционального оборудования и была разработана технологическая схема обогащения песка, показанная на схеме 2. Схема 2. Технологическая схема производства сухого обогащенного песка 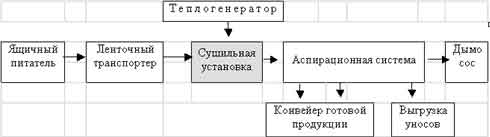
Основная технологическая идея переработки сырья по второй схеме заключается в его сушке, помоле и разделению частиц по плотности, крупности или электромагнитным свойствам в одном агрегате. Универсальность оборудования позволяет для песка организовать процесс без помола, а только по схеме "сушка - обогащение". Достоинства схемы: сушка материала осуществляется в вихревом потоке теплоносителя, где материал находится во взвешенном состоянии, при этом каждая частичка движется отдельно от других, комки (агломераты) отсутствуют. Это приводит к обдуву частиц песка со всех сторон и уносу молекул воды (преодолению сил поверхностного натяжения) с затратами меньшими, чем в традиционной сушилке. Удельный расход тепла в таких установках составляет 2800-4000 кДж на кг испаренной влаги при теоретически необходимом (мольная энтальпия испарения) 2259 кДж/кг влаги. При таком характере тепломассообмена частицы песка высушиваются за 0,3-0,5 сек., что обуславливает высокую напряженность сушил по влаге, достигающей 1000 кг/м3•час. Поскольку при обогащении песка по второй схеме его классификация осуществляется в полочных классификаторах аспирационной системы (отдув пылеватых частиц холодным воздухом), то температура песка на выходе составляет менее 50°С, следовательно, отпадает необходимость в установке дополнительно барабанного холодильника. Недостатки: повышенный расход электроэнергии, необходимый для создания пневмотранспорта высушенного материала по аспирационной системе, где осуществляется его классификация. Основные показатели работы технологических линий по двум вышеописанным схемам приведены в таблице 1. Табл. 1. Технико-экономические показатели технологических линий по обогащению песка. (Производительность линий - 10 тн/час для песка влажностью 10%). Технологическая линия | Тип сушильного аппарата | Удельные затраты тепла на сушку, кДж/кг влаги | Расход топлива | Объемное напряжение по влаге, кг/м3·час | Удельный расход электро-энергии, кВт/тн сырья | мазут, кг/тн влаги | природный газ, м3/тн влаги | Схема 1 | Сушильный барабан | 4200-5800 | 104-143 | 118-163 | 50-100 | 4,6-8 | Сушилка кипящего слоя | 5000-6500 | 123-161 | 141-183 | 150-200 | 4,9-8,3 | Сушилка виброкипящего слоя | 4000-5000 | 99-124 | 113-141 | 150-200 | 5,08-8,8 | Схема 2 | Виброгрохот Ultimate Screener | 2800-3000 | 69-74 | 79-84 | 1000 | нет данных | Мельница-сушилка "Баскей" | 3300-4000 | 82-99 | 93-113 | 600-800 | 10.2-13.3 |
Примечание: теплотворность газа - 35485 кДж/нм3; мазута - 40400 кДж/кг Таким образом, анализ существующих технологий обогащения песка показывает, что несомненными преимуществами обладают технологические линии, в которых организован более эффективный тепломассообмен. Их достоинства можно разделить на технологические и экономические. К технологическим преимуществам относятся совмещение процессов сушки, обогащения и охлаждения песка в одном агрегате, отсутствие грохочения и дополнительных пересыпок, потребность в меньших производственных площадях - в два и более раза. Экономическая эффективность применения технологической схемы №2 определяется соотношением цен на топливо и электроэнергию. Поскольку на сегодняшний день стоимость 1 кг мазута на порядок выше 1 кВт•ч электроэнергии, то простой расчет показывает, что при прочих равных условиях (производительность 10 тонн песка в час, влажность песка 10%, дозирование - ящичный питатель, подача в сушило - ленточный транспортер) за счет снижения затрат на топливо можно получить экономический эффект около 2 млн. рублей в год. 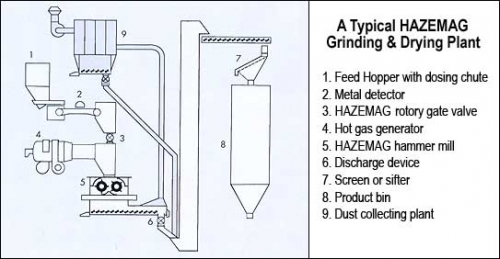
|