Брикетирование как альтернатива грануляции окатыванием, применительно к задачам складирования отходов, по нашему мнению, менее перспективно, т. к. не столь продуктивно, более капитало- и эксплуатационнозатратно, а также требует применения связующих добавок. Очевидное преимущество грануляции окатыванием заключается в характере процесса формирования агрегата (гранулы или брикета). В брикетировании он происходит последовательно и при значительном внешнем давлении. При грануляции же формирование агрегатов и их укрупнение происходит одновременно во многих точках гранулятора. Поэтому продуктивность окомкования намного выше. Важно, что уплотнение гранул и их прочность обеспечиваются за счет эффективного использования поверхностно-активных сил, что в конечном счете позволяет значительно снизить удельное энергопотребление на единицу продукции. Для обеспечения прочности гранул в состав шихты вводят связующие добавки (цемент, известь и др.) в количестве 3—15 %, которые в ряде случаев играют и пластифицирующую роль, т. е. ускоряют накатывание материала, повышают прочность сырцовых гранул и улучшают их сферичность. Дешевыми заменителями указанных дорогостоящих вяжущих могут служить пыли цементных и известковых печей, некоторые виды шлаков в размолотом состоянии, высококальциевые золошлаки от сжигания углей, сланцев, торфа и другие виды отходов, обладающих вяжущими свойствами. При брикетировании представляет интерес новый класс поверхностно-активных веществ типа “Konsolit”, отличающихся способностью полностью удалять водную пленку с поверхности частиц, благодаря чему возможно при относительно малом усилии обеспечить сближение частиц до уровня проявления молекулярного притяжения, т. е. достичь агрегирования без применения связующего. За рубежом подобные вещества эффективно применяют в современном дорожном строительстве. Впервые масштабную грануляцию отходов предложили специалисты Уральского политехнического института и предприятия “Уралтехэнерго” еще в 1978 г. как альтернативу гидрозолоудалению для проектируемой (и до сих пор не построенной) Новосибирской ТЭЦ-5, на которой предполагалось сжигать угли Канско-Ачинского бассейна с золами, содержащими повышенное (до 60 %) количество оксида кальция. Эти золы обладают сильно выраженными вяжущими свойствами. Соответственно гидроудаление такого материала весьма проблематично, но зато его грануляция и отвердение не вызывают затруднений. Позднее гранулирование золошлаков было предусмотрено как основной способ золошлаков удаления в проектах всех ТЭС, где предполагается сжигать подобные угли — Омская ТЭЦ-6, Чайковская ТЭЦ, Курганская ТЭЦ-2 и др. Одновременно разрабатывались проектные решения по замене гидрозолоудаления на грануляцию для ТЭС, уже использующих угли с высоко-кальциевыми золами, поскольку здесь имели место крупные аварии из-за ненадежности систем гидрозолоудаления. Наиболее удачным и эффективным следует считать проект, разработанный в Ростовском отделении института “Атом-ТЭП” для Березовской ГРЭС в Красноярском крае, предусматривающий грануляцию, транспортирование и складирование 1 млн м3 золы и шлака в год. В проекте предполагалось создание двух линий, оснащенных четырьмя тарельчатыми грануляторами диаметром 5,5 м (из них два резервных) и конвейером-отвердителем производительностью 120 т/ч. Для складирования затвердевших гранул запроектирована кольцевая канатная дорога производительностью 230 т/ч, с выгрузкой в надземный бурт высотой до 60 м, вместимостью 7 млн м3 и площадью около 25 га (рис. 3). При подготовке площадки планировались укладка легкого противофильтрационного экрана и система сбора и отведения атмосферных осадков. В сравнении с традиционным гидроотвалом новый вариант обеспечивал улучшение проектных показателей: снижение капитальных затрат на 20 %, эксплуатационных — на 30 %, сокращение площади складирования более чем в четыре раза. К сожалению, в связи с последними изменениями в энергетической политике страны сооружение упомянутой ГРЭС приостановлено на уровне 20 %-ной мощности, для золошлакоудаления используются так называемая “пусковая схема” с гидравлическим транспортированием и гидроотвал для складирования золошлаков. В летнее время большая часть золы отгружается строителям непосредственно с электрофильтров ТЭС. В ближайшем будущем планируется эначи тельное увеличение использования дешевых, экологичных и качественных углей Канско-Ачинского бассейна, причем на всех ТЭС, проектируемых для их сжигания, предусматривается применение грануляции золы. Наряду с канатными дорогами для складирования гранул рассматривают варианты конвейерного, железнодорожного и других видов транспорта. 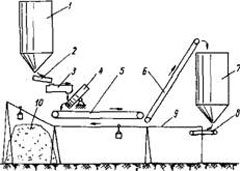 Рис. 3. Схема золоудаления с грануляцией золошлаков Березовской ГРЭС: 1— силос золы; 2 — пневмопитатель; 3 — гидрозолосмеситель; 4 — гранулятор; 5 — конвейер-отвердитель; 6 — элеваторный подъемник; 7 — силос гранул; 8 — транспортер; 9 — кольцевая канатная дорога; 10 — гранулохранилише Изучение превращений, происходящих в гранулохранилищах под воздействием атмосферных процессов, необходимо с позиции экологии, а также для оценки изменений в потребительских свойствах гранул. На рис. 4 изображено устройство для изучения воздействия атмосферных процессов на гранулированные продукты, моделирующее поверхностный слой гранулохранилища толщиной около одного метра. Оно состоит из четырех плотно соединяющихся пластиковых емкостей диаметром и высотой 0,3 м, с перфорированным, кроме нижней емкости, дном. Устройство заглублялось в грунт почти на всю высоту, что обеспечивало температурный режим хранения гранул, близкий к естественному. В заданные сроки емкости последовательно извлекались для отбора проб гранул и фильтрата, сборником которого служило дно нижней емкости. У фильтрата определяли показатель рН, у гранул — прочность, потери при прокаливании до 600 и 900 °С, а также содержание извести. Объектом исследования служили гранулы опытно-промышленной грануляции золы угля Березовского месторождения.
|