В процессе грануляции увлажненный до рыхло-сыпучего состояния материал при участии физических явлений, возникающих на разделе жидкой и твердой фаз, агрегируется в рыхлые комочки. Последние, благодаря взаимному воздействию, а также центробежным силам, уплотняются и теряют избыточную воду, образующую пленку на поверхности гранулы, которая, в свою очередь, адсорбирует порцию шихты и таким образом наращивает свой объем. По указанной причине гранулы имеют в разрезе четко выраженную слоистую структуру. При окомковании на тарели укрупнение гранул сопровождается их перемещением в поверхностные горизонты. При достижении “критического” размера гранулы, вытесняемые шихтой, постоянно поступающей на тарель, пересыпаются через ее борт и поступают на упрочнение. Обычно прочность сырцовых гранул составляет 1—5 Н. Она обеспечивается главным образом за счет склеивания твердых частиц шихты водными пленками и теряется при высушивании. В случае высокой дисперсности материала высушенные гранулы способны сохранять достаточно высокую прочность, причиной которой являются так называемые “контактно-конденсационные” силы межмолекулярного притяжения, уровень которых пропорционален дисперсности шихты. Производительность процесса, наряду с физико-химическими характеристиками материала и его дисперсностью, определяется также конструкцией гранулятора и режимом его работы.
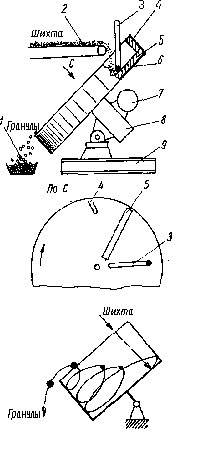 Рис. 1. Схема устройства и работы тарельчатого гранулятора: 1 — транспортер гранул: 2 — транспортер подачи шихты, 3 — водопровод с форсунками, 4 — бортовой скребок, 5 — донный скребок; 6 — тарель. 7 — привод вращения тарели; 8 — механизм регулирования угла наклона тарели, 9 — опорная рама На рис. 1 изображены устройство и принцип работы тарельчатого гранулятора, продукция которого характеризуется небольшими расхождениями в размерах гранул и высоким коэффициентом сферичности. Для получения необходимого размера гранул подбирают соответствующий режим работы гранулятора. Чаще всего варьируют угол наклона тарели, места подачи шихты на нее, точки доувлажнения шихты, положения скребков на тарели. Получение продукта монофракционного состава важно для увеличения удельной вместимости массива, т. к. в этом случае объем пустот в слое в сравнении с полифракционным уменьшается на 10—15 %. Соответственно возрастает уровень использования площади хранилища. По нашему мнению, целесообразно получать на складирование гранулы размером 10—15 мм, т. к. в этом случае, с одной стороны, сохраняется высокой производительность процесса (рис. 2), с другой — при транспортировании и утилизации без особых затруднений возможно использовать оборудование, обычно применяемое в технологии получения заполнителей для щебня и гравия, имеющих примерно те же размеры. 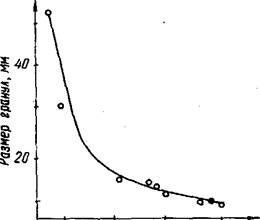 20 40 Выход гранул, т/ч Рис.2. Зависимость среднего диаметра гранул от производительности гранулятора
По своему устройству барабанный гранулятор аналогичен барабанным сушилкам, широко применяемым в различных отраслях промышленности. Это — наклонная труба с установленными внутри скребками и форсунками для распыления воды. При вращении барабана материал, окомковываясь, перемещается от высокого загрузочного конца в сторону низкого разгрузочного. Недостатком данных устройств считается полифракционный состав продукта, поэтому при производстве рудных окатышей они обычно доукомплектовываются грохотами, которые позволяют выделить нужную монофракцию, а мелкая, некондиционная фракция возвращается на укрупнение. При окомковании отходов на складирование, в случае когда нет необходимости добиваться максимальной вместимости хранилища, использование барабанного гранулятора будет вполне оправданным. Кроме упомянутых, существует еще ряд конструкций гранулирующих устройств, однако их возможности ниже, чем у рассмотренных.
|