Каталитический крекинг различных видов дистиллятного и остаточного сырья с целью получения высокооктановых бензинов и газа с высокой концентрацией пропан-пропиленовой и бутан-бутиленовой фракций. Процесс протекает при температуре 420 — 550 0С и давлении 0,1 — 0,3 МПа в присутствии алюмосиликатных, цеолитсодержащих и других катализаторов. Схема реактора каталитического крекинга (установки Г-43-107) 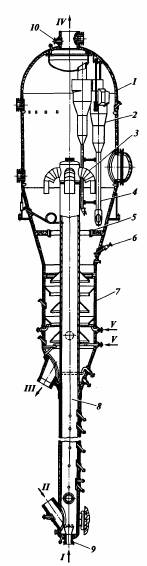
Примечание: 1- корпус; 2 – духступенчатые циклоны; 3 – баллистический сепаратор; 4 – стояки циклонов; 5 – подвижная опора; 6 – форсунки для шлама; 7 – десорбер; 8 – лифт-реактор; 9 – сопло с форсунками; 10 – штуцер предохранительного клапана. Потоки:
I – сырьё; II – регенерированный катализатор; III – закоксованный катализатор; IV – продукты крекинга; V – водяной пар.
Изомеризация Изомеризация нормальных углеводородов (пентан, бутан, бензиновая фракция) для получения изобутана, используемого для алкилирования, или изопентана — сырья для получения синтетического каучука и высокооктановых компонентов бензина. Катализатором изомеризации служит хлористый алюминий. Процесс ведут при температуре 120—150 °С и давлении до 1 МПа.
Гидроочистка Гидроочистка — для обессеривания нефтяных фракций, а также для насыщения водородом непредельных углеводородов, содержащихся в продуктах вторичной переработки. Этот процесс используется также для завершающей очистки масел и парафинов. Процесс осуществляется при температуре 300 — 420 °С и при давлении 3-4 МПа. Реактор гидроочистки дизельного топлива (с аксиальным движением сырья) 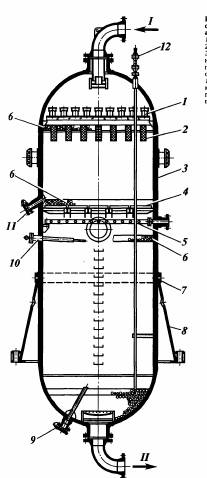 Примечания: 1 – распределительная тарелка; 2 – фильтрующее устройство; 3 – корпус; 5 – коллектор для ввода пара; 6 – фарфоровые шары; 7 – опорное кольцо; 8 – опора; 2, 11 – штуцер для выгрузки катализатора; 10, 12 – термопары. I – поток сырья; II – продукты реакции
Гидрокрекинг Гидрокрекинг высококипящих дистиллятных фракций для получения дополнительного количества светлых нефтепродуктов. Процесс осуществляется при температуре 370 — 420 ' С и давлении 14 — 20 МПа. Путем гидрокрекинга высокосернистых мазутов может быть обеспечено значительное снижение содержания серы в котельном топливе с целью уменьшения загрязнения воздушного бассейна двуокисью серы. Коксование Коксование нефтяных остатков и высококипящих дистиллятов вторичного происхождения, используемое для получения малозольного нефтяного кокса. Получаемые коксовые дистилляты вовлекаются в дальнейшую переработку для получения светлых нефтепродуктов. Коксование ведут при давлении 0,1 — 0,3 МПа и температуре 480 — 540 °С. Пиролиз Пиролиз нефтяных дистиллятов (бензин, керосин) или газа (этан, пропан) служит основным процессом производства важнейшего сырья нефтехимии — непредельных углеводородов (этилен, пропилен, бутадиен). При пиролизе получают также ароматические углеводороды (бензол, толуол) и пироконденсат. Процесс осуществляется при давлении ниже 0,01 МПа и температуре 650-900 0С. Алкилирование Алкилирование изопарафиновых углеводородов непредельными осуществляется с целью получения высокооктановых компонентов бензинов. В качестве непредельных углеводородов используют пропилен, бутилены, амилены, в качестве изопарафиновых углеводородов — изобутан или изопентан. Так, при алкилировании изобутана бутиленом получают изооктан. Реакция алкилирования осуществляется при температуре от 0 до — 10 0С, если в качестве катализатора используется серная кислота, или при 25 — 30 °С в присутствии катализатора — фтористоводородной кислоты. Реактор алкилирования (горизонтальный с турбосмесителем) Дегидрирование Дегидрирование — процесс, сопровождающийся отщеплением водорода от молекул, предназначается для получения непредельных углеводородов из предельных, например бутилена из бутана, бутадиена из бутилена, изоамилена из изопентана, изопрена из изоамилена. Процесс протекает на хромоалюминиевых катализаторах при температуре 530 — 600 °С и давлении атмосферном или ниже атмосферного. В результате дегидрирования из этилбензола получают стирол, а из изопропилбензола — а-метилстирол. Полимеризация Полимеризация — процесс получения высокомолекулярного вещества — полимера в результате взаимодействия низкомолекулярных веществ — мономеров. Этот процесс используется для получения пластмасс, синтетических каучуков, масел и других продуктов. Так, полимеризацией пропилена в присутствии катализатора — фосфорной кислоты получают тетрамер пропилена, используемый в производстве моющих средств. Полимеризацией пропилена получают высококачественную пластмассу — полипропилен. Полимеризацией изобутилена получают твердый полиизобутилен (молекулярная масса около 200 000) или жидкий полиизобутилен (молекулярная масса около 10 000). Подробнее с текущей ситуацией и прогнозом развития нефтеперерабатывающей промышленности в России можно познакомиться в отчете Академии Конъюнктуры Промышленных Рынков «Нефтепереработка в России: анализ текущего состояния и прогноз развития». Об авторе: Академия Конъюнктуры Промышленных Рынков оказывает три вида услуг, связанных с анализом рынков, технологий и проектов в промышленных отраслях - проведение маркетинговых исследований, разработка ТЭО и бизнес-планов инвестиционных проектов. • Маркетинговые исследования • Технико-экономическое обоснование • Бизнес-планирование
Академия Конъюнктуры Промышленных Рынков Тел.: (495) 918-13-12, (495) 911-58-70 E-mail: mail@akpr.ru WWW: www.akpr.ru |