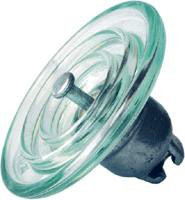
Использование силикатного фарфора для изготовления опорно-стержневых изоляторов (ОСИ) подорвало веру производителей электрической энергии России в отечественные фарфоровые изоляторы. В РФ эксплуатируется более 2 млн. шт. изоляторов серии ИОС старых типов в составе разъединителей и шинных опор 110-500 кВ. В соответствии с «Техническими требованиями на изоляторы керамические опорные на напряжение свыше 1000 В повышенной надежности для поставок в электро — и атомную энергетику», разработанными РАО «ЕЭС России», было начато создание нового поколения модернизированных ОСИ с повышенной надежностью работы в эксплуатации. Новые «Технические требования» устанавливали: • на вновь разрабатываемую или модернизированную продукцию выпуск технических условий и согласование их с потребителями; • применение материала керамического электротехнического подгруппы 120 (высокоглинозёмистого материала) ГОСТ 20419-83 взамен подгруппы 110 (кварцевого фарфора); • исключение применения серого чугуна для изготовления арматуры изоляторов; • обязательное проведение испытаний изоляторов на надёжность. Весомым аргументом в пользу безотказного применения модернизированных ОСИ является многолетний опыт эксплуатации изолятора ИОС-110-1250 М УХЛ1, в конструкции которого с момента его «рождения» был применен высокопрочный чугун при изготовлении фланцев и высокоглинозёмистый материал для изоляционной части изолятора. На протяжении всего времени изготовления ИОС-110-1250 М УХЛ претензий от потребителей по качеству изоляторов не было. ОАО «ЭЛИЗ» первыми в России в 2001 году освоил выпуск модернизированных изоляторов ИОС-110-600 М УХЛ1, ИОС-110-400 М УХЛ1 и провёл испытания в известных испытательных центрах России: НИИПТ, ФГУП ВЭИ им. Ленина и ВНИИЭ. В последующие годы в 2003 году ОАО «ЭЛИЗ» освоило изоляторы ИОС-110-1250 М УХЛ1, в 2005 году — ИОС-110-2000 М УХЛ1 и ИОС-110-2000 М-01 УХЛ1 и усовершенствовал конструкцию изоляторов ИОС-110-600 М УХЛ1, ИОС-110-400 М УХЛ1 с целью снижения весовых характеристик изоляторов. Снижение весовых характеристик в сравнении с освоенными ранее изоляторами составило в среднем 23 %. Результаты механических испытаний изоляторов облегчённых конструкций, проведенных в процессе проведения испытаний на надежность, не уступали достигнутым ранее результатам. Перевод изоляторов на надёжные материалы, как для изготовления изоляционной части изолятора, так и для изготовления арматуры изолятора, вернул веру у производителей электроэнергии, как в России, так и в странах ближнего зарубежья, в качество новой продукции. Все выпускаемые опорно-стержневые изоляторы сертифицированы в системе ГОСТ Р, в органе сертификации «Энергосерт» и по желанию потребителей — в «ЭнСЕРТИКО». В настоящее время в России стремительно расширяется выпуск и применение полимерных изоляторов. Число предприятий, выпускающих полимерные изоляторы, в несколько раз превышает производителей фарфоровых изоляторов. Ни для кого не секрет, что производство полимерных изоляторов не требует огромных вложений и помещений, как при производстве фарфоровых изоляторов. Производство полимерных изоляторов можно освоить в небольшой мастерской, тогда как для производства фарфоровых изоляторов нужен завод. Кажущаяся простота изготовления полимерных изоляторов привлекает многих предпринимателей. Однако не всегда в процессе производства соблюдаются технологические требования, что и приводит к отказам изоляторов в эксплуатации. Достаточно широкий опыт эксплуатации некерамических изоляторов первого поколения (1970-1985 г.) в целом был не очень благоприятным: наблюдались трек и эрозия защитной оболочки, хрупкий излом стеклопластикового стержня и другие повреждения. Это приводило во многих случаях, как к перекрытиям изоляторов, так и к тяжёлым авариям, в том числе с падением проводов на землю. В результате произошедших повреждений и аварий многие производители перестали выпускать некерамические изоляторы, а другие фирмы пошли по пути улучшения, как конструкции изолятора, так и технологии их изготовления. Учитывая недостатки конструкции изоляторов и изготовления изоляторов по технологии «шашлычного» оформления рёбер защитной оболочки, многие производители освоили новую технологию изготовления защитной оболочки изолятора — цельнолитое формование за один цикл. Опыт эксплуатации линейных полимерных изоляторов второго поколения ещё весьма ограничен и не позволяет сделать заключение о показателе надёжности таких изоляторов. У различных производителей технология изготовления и рецептура кремнийорганических композиций не являются полностью одинаковыми, что делает выбор изоляторов для эксплуатации крайне сложным. Изоляторы различных изготовителей с одинаковыми начальными электрическими и механическими характеристиками могут стать неодинаковыми по надёжности работы через несколько лет старения в условиях эксплуатации. |