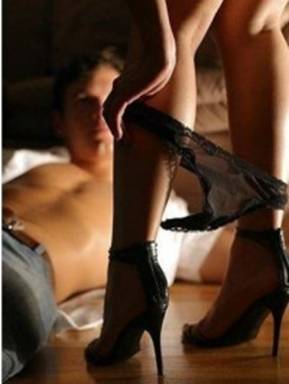
Кроме того, возрастает роль волокон с функциональными свойствами: термо- и огнестойких и др. Несмотря на то, что их выпуск в мире не превышает 1% от объема производства всех химических волокон, финансовые результаты реализации впечатляют - около 1, 1 млрд. USD в год. К числу этих полимерных волокон относятся: пара-арамидные; углеродные; карбидокремниевые; термоогнестойкие (поллимидные и других классов); хемосорбционные (ионообменные); полые с селективно-проницаемой стенкой. Пара-арамидные волокна. Это волокно, которое получается из ароматических полиамидов и содержит в своей цепи не менее 85% амидных групп. К числу данных волокон относятся кевлар(фирма «Дюпон», США), тварон(фирма «Тейджин-Акзо», Нидерланды), технора(фирма «Тейджин», Япония), армос(ООО «Лирсот», Россия).1 Общий объем производства этих волокон составляет более 40 тыс. тонн и неуклонно растет. В США - на 15% ежегодно (с инвестициями до 50 млн. USD), в Нидерландах с 7 тыс. до 18,5 тонн/год (с инвестициями до 200 млн. евро), в Японии с 1,4 тыс. до 2 тыс. тонн/год (с объемом инвестиций 10 млн. USD).2 Механические свойства пара-арамидных волокон достаточно высоки. При этом соответствующие показатели волокон этого класса отечественного производства заметно превышают показатели зарубежных (табл. 1).3 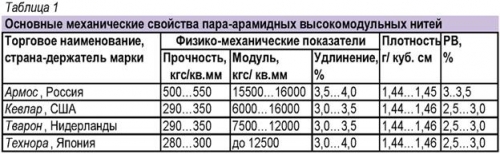
Отечественные производства выпускают армос в виде нитей линейной плотности 14,7...100 текс и жгутов - до 600 текс. Пара-арамидные волокна характеризуются высоким уровнем огне- и термостойкости. Так, для пара-арамидов характерны почти полная безусадочность при высоких температурах (только при достижении температуры 400...450°С наблюдается усадка, не превышающая 3-4%) и высокая устойчивость к воздействию открытого пламени (до 500°С; после удаления из пламени волокно гаснет, что обусловлено высоким кислородным индексом - 38...40% и высокой температурой разложения - 450...550°С). Кроме того, эти волокна мало меняют свои свойства в мокром состоянии, так как они достаточно гидрофобны и после сушки восстанавливают свои свойства. Этот вид волокон используется в основном для изготовления высоконапряженных конструкционных пластиков, средств баллистической защиты, в резинотехнике, а также там, где нужно получить прочные малодеформативные текстильные изделия для средств спасения или обеспечения профессиональной безопасности. В настоящее время планируется создание отечественного пара-арамидного волокна с повышенными баллистическими и механическими свойствами. Углеродные волокна. Использование этих волокон не только целесообразно, но и экономически достаточно выгодно. Созданные на их основе теплозащитные и конструкционные материалы обладают регулируемыми электрофизическими свойствами, низкой плотностью, высокими механическими показателями, хемостойкостью и сорбционной активностью. По прочности (как абсолютной, так и относительной) эти волокна в настоящее время являются непревзойденными. Ведущие фирмы-производители углеродных волокон действуют в Японии и США, там же находятся и основные потребители. Общие мощности производства превышают 20 тыс. тонн/год.4 Углеродные материалы могут выпускаться в виде нитей, жгутов и тканей. Хотя в настоящее время прочность по углеродному волокну достигла свыше 700 кгс/мм2(марка Т 1000 фирмы «Торей», Япония), наиболее широко используется материал с прочностью 300...350 кгс/мм2. В свое время НПО «Химволокно»(г. Мытищи)разработало технологии получения углеродных волокон на основе вискозы и ПАН-волокон, которые по тому времени относились к числу передовых (а на базе вискозы таковыми остались и сегодня), и внедрила эти технологии на предприятиях отрасли в Светлогорске и Балакове. Однако к настоящему моменту эти технологии достаточно устарели. Для того чтобы выйти на передовые позиции, необходимы смена качества исходного сырья по ПНА-волокну для повышения механических характеристик углеродного волокна, а также замена температурного оборудования - для снижения энергоемкости производства. Как видно, области использования материалов на основе углеродных волокон (табл. 2) достаточно широки, объем их потребления постоянно увеличивается, особенно в машиностроении и строительстве. 
Заметим, что углеродные волокна могут заменять собой до 10 кг металла, при этом при их производстве электроэнергии расходуется в 3...20 раз, чем при выпуске металла. Ресурс эксплуатации изделий на основе этих волокон увеличивается до 300%, а трудоемкость при изготовлении изделий снижается до 40...60%. Карбидокремниевые волокна. Высокопрочные и высокомодульные эти волокна (керновые и бескерновые) являются наиболее перспективным армирующим материалом для создания высокотемпературных композитов. Особенно остро эта проблема стоит перед создателями авиационных двигателей: процесс достиг своего критического уровня, так как ни улучшением конструкции двигателя, ни применением новых металлических сплавов невозможно решить проблему повышения его эксплуатацонных характеристик. Выход представляется в применении жаростойких материалов, к числу которых относится керамика, способная работать при высоких температурах в окислительной среде. Однако керамика обладает низким коэффициентом трещиностойкости. Для устранения этого недостатка и используются карбидокремниевые волокна. Их применение позволяет получать металлокомпозиты на основе интерметаллидных сплавов титана, работающие при 800°С (вместо 500...600°С) и поднять прочность и модуль упругости примерно в 1,5 раза, а также создать керамические композиты на рабочие температуры в окислительной среде - выше 1300°С. Это позволит создать новые газотурбинные авиационные двигатели с повышенными техническими и экономическими характеристиками с массой на 40...50% ниже, чем у ныне действующих. |