С помощью новой находящейся на стадии выдачи патента технологии, разработанной компанией AtoFina Chemicals из Филадельфии, можно создавать пенопласты с высокой огнестойкостью из поливинилиденфторидного (PVDF) фторполимера без использования вспенивающего вещества или формования из расплава. Новая технология сочетеют использование жидколатексного сополимера Kynar PVDF от компании AtoFina со стекломатом или другим тканевым наполнителем для производства пенопластов с открытыми порами, которые, по имеющимся данным, производят очень мало дыма и пламени при проведении испытания на воспламеняемость. Источники из AtoFina описывают пенопласты Kynar как “практически не воспламеняющиеся”. Kynar PVDF пропускает ультрафиолетовые лучи, устойчив к воздействию атмосферных явлений, он также устойчив к воздействию химических веществ при повышенных температурах. В число потенциальных применений для новых пенопластовых композитов входят термоформованный лист для производства противопожарных панелей в оборудовании для транспортировки, строительства и обработки нефтехимических продуктов. К числу прочих относятся: изолирующая оболочка пожаростойкого кабеля для высотных зданий, покрытия на огнезащитной одежде для команд спасателей, защитное экранирование для домов и прочих сооружений, которым угрожают природные пожары, и покрытия на сальниках или прочих применениях, в которых материал уже пожаростойкий, но не выдерживает воздействия химических веществ. 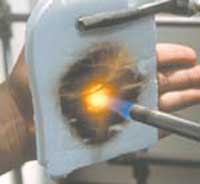
Панель из стекломата в 3/8 дюйма, инкапсулированная в пенопласт из латексного PVDF, устойчива к прожогу пропановой горелкой дольше, чем алюминиевый лист в 1/8 дюйма. Обратная поверхность пенопласта остается холодной на ощупь на протяжении 2 минут и более. Компания AtoFina рассматривает лицензионные соглашения или иные способы коммерческой реализации технологии. Никаких вспенивающих веществ Хотя из фторполимеров можно экструдировать пенопласты с использованием химических вспенивающих веществ или прямой инжекции газа, у латексной технологии AtoFina имеется то преимущество, что она позволяет использовать длинноволоконные маты или волокна. Осуществление технологии начинается с пропитывания армирующего мата латексом PVDF на водяной основе. После этого используется собственный метод компании по замораживанию смеси и высушиванию ее до твердого состояния в пресс-форме. По мере того, как вода испаряется из смоляной матрицы, ее замещает воздух, оставляя при этом очень однородную открыто пористую структуру из взаимосвязанных пустот, поясняет научный сотрудник Рамин Амин-Санайеи Подробности технологии охлаждения составляют тайну, но этот процесс может занимать от 3 до 12 часов. Источники в компании AtoFina сообщают, что можно сократить цикл всего до 20 минут за счет использования умеренного нагревания до примерно 1400 F вместо охлаждения. Плотность получаемого пенопласта зависит от концентрации твердого полимера в латексе. Плотность ненаполненного твердого сополимера PVDF составляет примерно 1.78 г/куб. см. Латексная технология AtoFina позволяет создавать пенопласт с плотностью 0.25 г/куб. см. или менее. Объемная доля пустот в пенопласте может составлять до 85% или даже более. Для того, чтобы создавать различные значения удельной плотности и текстуры пенопластов, можно добавить некоторые растворители в небольших концентрациях для повышения однородности структур пор и их распределения.
|