Производители обнаружили, что эта технология обеспечивает высокую производительность и имеет множество других преимуществ перед выдувным формованием при производстве точных деталей с формой трубы для медицинской и автомобильной отраслей промышленности, а также бытовых товаров. Но технологи еще не реализовала весь свой потенциал в области, которая может быть для нее наиболее продуктивной: в области производства деталей с замкнутым концом, таких как бутылки. Похоже это отличная идея: непрерывная экструзия цепочки полых деталей с использованием специальных инструментов, смонтированных на установку для получения гофрированной трубы. Их можно потом просто нарезать. По сведениям, полученным от тех немногих компаний, которые пробовали это сделать, формование на установке для гофрирования автомобильных и медицинских деталей, а также деталей для бытовых устройств дает производительность на 30 - 50% выше, чем установка для выдувного формования с поступательно-возвратным движением с тем же размером экструдера. Они также сообщают, что образуется незначительное количество заусенцев или же не образуется никаких, и создаются стенки более однородной толщины, чем при выдувном формовании. Быстрее осуществляется замена инструмента и пуск. В то же время эта технология является более гибкой в том, что касается диапазона используемых смол и возможности одновременного производства разных продуктов. Так почему же и другие компании не делают этого? 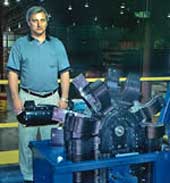
| Такая вертикальная установка для производства гофрированных труб у Omico действует так же, как и пневмоколесная установка для выдувного формования. Созданная компанией Cullom (в настоящее время Modern Machine), она имеет кокиль с вертикальным разъёмом типа "книга", который можно удалить с помощью одного стержня для быстрой замены формы. Рядом с ней стоит старший вице-президент Omico Роджер Эванс. |
Одной из причин является то, что невозможно просто купить готовую технологию. Хотя можно адаптировать под данную технологию практически любую установку для гофрирования, имеющие решающее значение инструменты и последующие операции подгонки являются патентованными разработками самих обработчиков. По всему миру известно о всего нескольких десятках случаев вакуумного формования компаниями на гофрировочной установке отдельных деталей. Но истинное количество могло бы быть намного больше, поскольку можно формовать детали и на обычных установках по производству гофрированных труб: для этого не требуется практически никаких модификаций, кроме различных пресс-форм. У этой технологии нет даже "официального" названия, хотя пользователи часто называют ее просто "вакуумным формованием". Эта технология в значительной степени общедоступна, поскольку весь процесс аналогичен процессу изготовления секций гофрированных труб с расширением, сформованным с одного конца. Если взять такие детали, как гофрированные шланги с гладкими секциями, то технология начала использоваться еще в семидесятых годах. Обычно при стандартном производстве гофрированной трубы используют непрерывную цепь формованных блоков, смонтированных на одной или двух овальных направляющих, для вакуумного формования непрерывно экструдируемой трубы или заготовки. Эта концепция не так уж сильно отличается от концепции пневмоколесной установки для выдувного формования, кроме того, что используется вакуум вместо положительного избыточного давления воздуха (хотя иногда при изготовлении более крупных деталей используется и давление воздуха). Более однородные стенки По словам знатоков, у формования деталей на установке для гофрирования имеется несколько преимуществ перед выдувным формованием. Сообщается, что пуск производится быстрее на установке для гофрирования, чем на установке для выдувного формования: от 5 до 10 минут, по сравнению с 30 минутами и более. Установка для гофрирования не дает практически никаких заусенцев то время как установка для выдувного формования дает большое количество заусенцев Сторонники технологии говорят, что при использования установки для гофрирования стенки значительно более ровные, поскольку детали изготавливаются вакуумным формованием, а не выдуванием. Сообщается, что выдувание профиля в форме делает стенки более тонкими на краях выступов, то есть именно там, где необходимо иметь больше материала. Формование на установки для гофрирования используется в настоящее время в первую очередь для изготовления деталей, имеющих форму трубы, которые должны иметь на концах разные размеры. Сторонники этого метода говорят, что он имеет еще больший потенциал при использовании его для производства изделий с замкнутым концом, таких как бутылки. Но установка для гофрирования все же не может соперничать по производительности с пневмоколесной установкой для выдувного формования. На установке для гофрирования можно формовать примерно на 30% меньше единиц в час, по крайней мере, за одну серию, здесь менее эффективное используется большое количество пресс-форм. Пресс-формы установки для гофрирования находятся в контакте с пластмассой только 49% времени, в пневмоколесной установке для выдувного формования контакт имеет место в течение, по крайней мере, 70% времени. 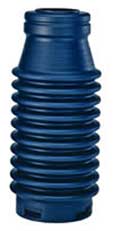
| Этот пылезащитный чехол для подвески автомобиля можно производить выдувным формованием, но компания ABC Group сочла гофрирование более рентабельным. |
Производить семейства деталей Сторонники данной технологии утверждают, что при формовании на установке для гофрирования можно производить полые детали из смол с меньшей прочностью расплава, которые нельзя было бы использовать при традиционном выдувном формовании. Установка для гофрирования позволяет также производить различные детали в последовательности в ходе одного цикла, но у них должны быть одинаковые диаметры и толщина стенок. Формование на установке для гофрирования является также эффективным способом производства данного продукта с широким диапазоном параметра длины. Так, например, Global Med Inc. из Трентона, Онтарио, формует медицинские гофрированные трубки для респираторов и введения анестезии, преимущественно, с длиной от 40 до 72 дюймов. Но компания Global Med также производит короткие трубки до 6 дюймов, и длинные до 120 дюймов. Изменение длины продукта при использовании установки для гофрирования требует всего лишь переключения положения одной пары формовочных блоков, которые образуют конец трубки. По словам представителей Global Med, это занимает от 15 до 20 минут. Другим применением, при производстве которого установки для гофрирования изготавливают семейство продуктов различной длины, является многожильный кабель для автомобилей. В компании Corma говорят, что они продали более 100 установок для гофрирования в США и более 30 в Японию для вакуумного формования пучков проводов для автомобилей. Corma, Unicor и Olmas Plastics Machinery из Италии (представленная здесь Summit Machinery Sales) – все предлагают двухстренговые установки для гофрирования, которые могут увеличить производительность.
|