Взрыв произошел, когда пары углеводородов, более тяжелые, чем воздух, воспламенились, по всей видимости, вследствие контакта с работающим двигателем автомобиля. Причиной появления углеводородов стало то, что отгонная колонна рафината была переполнена, сработала система защиты от избыточного давления, и произошел перелив жидкости из выпускной трубы. Серьезность происшествия усугубилась из-за большого количества людей находившихся в эпицентре взрыва. Нефтеперерабатывающий завод в Техасе - самый крупный и наиболее комплексный НПЗ компании ВР с проектной мощностью более 70 млн. л/сут. и производством порядка 40 млн. л бензина/сут. Он также производит авиатопливо, дизельное топливо и сырье для химической промышленности. НПЗ насчитывает 30 технологических установок, расположенных на площади в 480 га. Численность постоянного персонала этого предприятия составляет около 1800 сотрудников, в момент происшествия примерно 800 подрядчиков выполняли важные ремонтные работы. На заводе широко применяются системы управления промышленной безопасностью внедренные компанией Amoco до ее слияния с ВР в 1999 г. Взрыв произошел на установке изомеризации и захватил отгонную колонну рафината (далее – Колонна), а также продувочный барабан и выпускную трубу. Установка изомеризации перерабатывает низкооктановое смешанное сырье в компоненты с более высоким октановым числом для компаундирования неэтилированного бензина стандартного качества, с октановым числом не менее 82. Установка включает четыре секции, одной из которых является Колонна, на которую из регенерационной установки ароматических веществ поступает поток неароматических соединений, разделяющихся в ней на легкие и тяжелые компоненты, рис. 1. Колонна может работать совместно с установкой изомеризации либо автономно, обеспечивая накопление запасов при отключенной установке изомеризации.
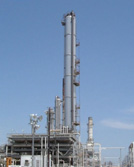 Рис. 1. Колонна рафината Колонна была впервые введена в эксплуатацию в 1976 г., но несколько раз подвергалась модификации. Она представляет собой одиночную фракционирующую ректификационную колонну высотой 50 м с 70 перегонными тарелками, уравнительным резервуаром для сырья, ребойлером с пламенным нагревателем, конденсатором верхнего продукта с лопастным вентилятором, и сборником орошающей фракции, рис. 2. Колонна объемом примерно 590 тыс. л обеспечивает переработку более 7 млн. л/сут. рафината из регенерационной установки ароматических соединений. Примерно из 40% общего количества рафината, поступающего в установку, получается верхний продукт – легкий фракция C5/C6. Остающийся кубовый продукт состоит из тяжелой фракции C7/C8.
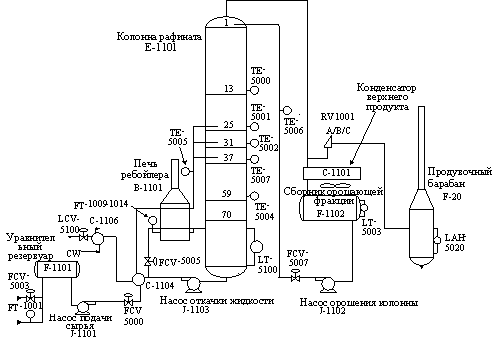 Рис. 2. Блок-схема колонны рафината Горячие пары углеводорода и небольшие количества сопутствующих жидкостей из систем сброса, вентиляции и откачки установки изомеризации во время сбоев или остановок отводятся в систему продувки. Система продувки состоит из коллекторов предохранительных выпускных труб (один из которых отходит от Колонны), продувочного барабана, выпускной трубы (F-20) и откачивающего насоса. Пары выходят через верхнюю часть выпускной трубы и рассеиваются в атмосфере, а жидкости стекают из барабана через S-образное колено трубы в закрытую канализационную систему предприятия. Выпускная труба F-20 была введена в эксплуатацию в 1950-х годах и с тех пор несколько раз подвергалася модификации. Во время запуска установки изомеризации в среду, 23 марта 2005 г., после временного простоя произошел взрыв и возник пожар, вследствие чего погибли пятнадцать и получили ранения свыше 170 человек. Многие из пострадавших или погибших находились внутри либо возле временных вагончиков, используемых для бытовых нужд контрактных рабочих, занятых в капитальном ремонте соседней установки ультракрекинга. Несколько вагончиков располагались между двумя работающими установками – установкой изомеризации и установкой десульфирования нафты. Ближайший сдвоенный вагончик находился в пределах 50 м от основания F-20, во время взрыва именно в нем произошло большинство несчастных случаев с летальным исходом. Вагончики размещались в этом месте и прежде, поскольку ничто не вызывало беспокойства. Место происшествия было огорожено, и группа по расследованию происшедшего на следующий день начала изучение обстоятельств аварии для выявления основных причин и выработки рекомендаций по предотвращению подобных происшествий. Расследование проводилось на протяжении 8 месяцев и включало в себя осмотры места происшествия, опросы свидетелей, анализ документов и материалов, а также химический анализ технологических проб. Жесткий диск компьютера автоматизированной системы управления технологическим процессом был изъят. Для оформления документальных доказательств и моделирования взрыва были привлечены сторонние специализированные компании. Технологическая контрольно-измерительная аппаратура, такая как индикаторы уровня и предохранительные клапаны, были подвергнуты испытаниям, также был проведен осмотр Колонны изнутри.
ХРОНИКА ПРОИСШЕСТВИЯ В сентябре 2004 г. недалеко от Колонны были установлены вагончики. Люди размещались в них с конца октября 2004 г, не смотря на отсутствие разрешения. В марте и феврале 2005 г. проводились плановые ремонтные работы на установке изомеризации, численность рабочих в смену была удвоена. В ходе этих работ Колонну отключили, очистили и проверили на герметичность. 22 марта отдел производственного планирования потребовал от начальника смены запустить колонну рафината. Техники занимались проверкой контрольно-измерительной аппаратуры Колонны, когда им сообщили, что установка будет запускаться. Из показаний свидетелей следует, что все проверки могли быть не завершены до запуска. 22 марта на регулирующий клапан системы вентиляции, рассчитанный на избыточное давление в 0,2 атм и используемый для удаления азота из Колонны, было подано давление, хотя из заявлений очевидца неясно, работал ли он надлежащим образом. В регистрационном журнале не было никаких записей, и заказ на ремонт не поступал. В ночь с 22 на 23 марта начальник смены отдал распоряжение оператору начать запуск Колонны. Оператор принял на себя управление заполнением колонны насадочным материалом, включил подачу холодного сырья в Колонну, чтобы установить уровни во входном сепараторе и в колонне и заполнить циркуляционный контур ребойлера. Перед запуском контрольно-измерительная аппаратура на колонне не была проверена в соответствии с процедурой. В 02:13 23 марта оператор начал загрузку сырья в Колонну на уровне приблизительно 2,4 млн. л/сут. К 02:38 датчик уровня начал указывать на постепенное его увеличение. В 02:44 оператор открыл клапан-регулятор расхода ребойлера, чтобы создать циркуляцию в ребойлере, и заполнил контур ребойлера жидкостью, вызвав падение уровня на 3% к 02:55 (3% приблизительно эквивалентно высоте 84 см выше касательной). После этого уровень основания Колонны постепенно поднимался, пока не сработала сигнализация верхнего уровня при 72% в 03:05 ч. (высота примерно 175 см выше касательной). Оператор отключил сигнализацию и в 03:08 снизил интенсивность подачи до 1590 тыс. л/сут. Резервная жестко смонтированная сигнализация верхнего уровня (78%) не сработала. Согласно показаниям приборов, уровень основания Колонны к 03:16 достиг 100%, и в 03:20 сырье регенерационной установки ароматических веществ было направлено в резервуар. Оператор перекрыл подачу сырья и циркуляцию ребойлера, чтобы оставить проведение оставшейся части запуска дневной смене. В момент передачи смены колонна имела избыточное давление 0,27 атм и индикацию 100%-го уровня основания (3 м выше касательной). Ночная смена не сообщила о неисправности жестко смонтированной сигнализации верхнего уровня заступающей дневной смене ни устно, ни в журнале передачи смены. Наряд-заказ на ремонт сигнализации не был выписан. После прихода примерно в 06:00 операторы дневной смены выполняли свои рутинные обязанности и проверяли настройки установки. Начальник дневной смены пришел на место в 07:13. Перед началом работ ни проверка безопасности объекта, ни контроль порядка действий не проводились. В 09:21 внешние операторы на короткое время открыли 8-дюймовый выпускной клапан с цепным приводом и сбросили давление до номинального атмосферного давления, но давление к 10:08 вновь поднялось до 0,034 атм. Оператор пульта дневной смены запустил циркуляцию ребойлера в 09:41 и в 09:52 возобновил подачу сырья в Колонну с интенсивностью в 3180 тыс. л/сут. После подачи давления на сливной регулирующий клапан тяжелого рафината в целях проверки оператор закрыл этот регулирующий клапан вручную. Расходомер показывал расход тяжелого рафината в диапазоне от 478 до 747 тыс. л/сут. Предполагается, что это была ошибка установки нуля на приборе, поскольку регулирующий клапан был закрыт и теплообмена между тяжелым рафинатом и сырьем не было. Приблизительно в 10:00 были зажжены две главные горелки в пламенном нагревателе ребойлера. Вскоре после этого начальник дневной смены по установке изомеризации ушел с рабочего места по семейным обстоятельствам. Позже он заявил, что передал полномочия по управлению начальнику смены установки десульфирования нафты, но подтвердить это не было возможности. Еще две главные горелки были зажжены в нагревателе в 11:17, и температура нижней части Колонны продолжала подниматься со скоростью примерно 42°С в час в сравнении с 28°С/час, предписанными процедурой запуска. Точное число главных горелок, которые в конечном итоге были зажжены, неизвестно, поскольку это не зафиксировано в документах, а опрошенные операторы называли разное количество – четыре, пять или шесть горелок. На протяжении этого периода подача сырья в Колонну продолжалась с интенсивностью около 3,2 млн. л/сут., а слив тяжелого рафината оставался закрытым. Отбор жидкостей из Колонны не проводился, несмотря на непрерывную подачу сырья. Внешние операторы, обеспокоенные продолжающимся отсутствием какой-либо индикации уровня жидкости в сборнике орошающей фракции, поздним утром проверили спускное отверстие в нижней части уровнемера, при этом вышел только пар. Датчик уровня сборника орошающей фракции продолжал показывать 0% до 13:20. Исполняющий обязанности мастера, начальник смены установки десульфирования нафты, внешний оператор и оператор-стажер ушли с рабочего места на обед и вернулись к 12:05. Исполняющий обязанности мастера заявил, что он потратил 75% своего рабочего времени в тот день, оказывая помощь в капитальном ремонте регенерационной установки ароматических веществ. К 12:20 в основании Колонны была достигнута запланированная температура в 135°С, указанная в процедуре запуска, при этом температура подаваемого в Колонну сырья составляла всего 49°С вместо требуемой 96°С. Интенсивность подачи оставалась неизменной на уровне 3,2 млн. л/сут. К 12:40 давление в Колонне, неуклонно возрастая, поднялось выше 2,2 атм, хотя нормальное рабочее давление составляет около 1,4 атм. Оператор-стажер заметил высокое давление на экранном индикаторе вспомогательной операторной и привлек к этому внимание других операторов. В этот момент внешние операторы второй раз открыли 8-дюймовый выпускной клапан с цепным приводом, чтобы уменьшить повышенное давление. Стажер сообщил о том, что видит испарения выходящие из верхней части выпускной трубы «похожие на пар», но другой оператор сказал ему, что не стоит беспокоиться, так как в этом нет ничего необычного. Примерно через 10-15 минут клапан с цепным приводом был закрыт, и к давление упало до 1,5 атм. К 12:40 температура в основании Колонны достигла 150°С, в то время как нормальной температурой считается 135°С. Подача сырья в Колонну продолжалась на уровне 3,2 млн. л/сут. без какого-либо оттока, и по расчетам уровень в колонне превысил 40 м. При такой температуре, согласно результатам моделирования, должно происходить некоторое парообразование в нижней части Колонны, несмотря на «шапку» более холодной жидкости сверху. Это подняло бы уровень жидкости выше тарелки 13, но ниже, чем потолочный трубопровод в верхней части колонны. Холодная жидкость, находящаяся выше в колонне, охладила эти пары и не дала им выйти через верх колонны. Проанализировав состояние установки на вспомогательном пульте управления, оператор позвонил оператору пульта дневной смены и сказал, что ему необходимо произвести отвод тяжелого рафината из колонны. В 12:41 оператор пульта дневной смены открыл регулирующий клапан отвода тяжелого рафината. Индикации потока отводимого тяжелого рафината не было примерно до 13:00, а к 13:09 поток стабилизировался на уровне примерно 5 млн. л/сут. Подача сырья в Колонну продолжалась на уровне 3,2 млн. л/сут., и таким образом за время с 09:52 до 13:00 ч. в колонну поступило приблизительно 400 тыс. л. На основании упрощенного расчета, без учета влияния парообразования в основании колонны, можно сделать вывод, что уровень в колонне достиг 42 м. При таком уровне 57 из 70 тарелок в колонне были затоплены, и входное отверстие для сырья на тарелке 31 было ниже уровня жидкости. Все это время датчик уровня был полностью затоплен и выдавал на экран системы индикации и управления сигнал, медленно смещающийся вниз к 80%, сигнализация верхнего уровня не работала. Проведение совещания по вопросам ремонта установки ультракрекинга было назначено в сдвоенном вагончике, и участники начали собираться около 13:00. В 13:01 предварительный нагрев сырья составлял 52°С и увеличился до 127°С к 13:10 Такое аномально быстрое повышение температуры привело к быстрому началу испарения сырья в точке входа в колонну (тарелка 31). Это должно было бы поднять уровень жидкости над питательной тарелкой, и даже выше, так что жидкость быстро бы достигла верха Колонны и перелилась в 24-дюймовый потолочный трубопровод. В 13:09 оператор позвонил домой начальнику дневной смены, который, услышав о динамике изменения давления, предложил открыть 1½-дюймовый выпускной клапан возле предохранительного клапана сборника орошающей фракции, чтобы выпустить азот, что и было сделано. К 13:13 давление на входе в конденсатор верхнего продукта упало с 1,54 до 1,4 атм. Сырье за счет теплообмена с отводимым тяжелым рафинатом быстро нагревалось, и как следствие стало испаряться на входе в колонну. К тому же добавилось парообразование в нижней части колонны. Все эти факторы способствовали быстрому росту давления, что привело к чрезмерно высокому подъему уровня жидкости и ее переливу через верх колонны в потолочный трубопровод. Жидкость заполнила 24-дюймовый потолочный трубопровод выше уровня датчика давления и предохранительных клапанов, расположенных примерно на 46 м ниже верха колонны. Примерно в это время оператор попросил уменьшить горение в печи ребойлера, так как температура основании Колонны превышала 150°С. В 13:14 оператор пульта подрегулировал расход на регулирующем клапане топливного газа, чтобы уменьшить температуру на выходе ребойлера. К 13:15 давление на входе в конденсатор верхнего продукта достигло 4,3 атм, и предохранительные клапаны на колонне открылись для выпуска верхнего продукта непосредственно в продувочный барабан и выпускную трубу F-20. На этом этапе сжигание топливного газа, подаваемого на подогреватель, было остановлено, и внешние операторы блокировали главные горелки. В 13:16 исчезла сигнализация аварийно низкого уровня в сборнике орошающей фракции, впервые появилась индикация наличия жидкости в резервуаре, и в 13:17 внешние операторы запустили насос для орошения колонны. Согласно показаниям прибора, интенсивность орошения зашкалила и превысила 5,6 млн. л/сут. В 13:19 исчезла сигнализация нижнего уровня в сборнике орошающей фракции, это указывало на то, что резервуар был заполнен жидкостью, сборник обычно работает в переполненном состоянии. В это время также был запущен второй насос орошения колонны, хотя никто из операторов в ходе опроса после аварии не вспомнил о том, чтобы сделал это. Примерно в это же время поступили радиосообщения минимум от двух очевидцев, которые видели, как пары и жидкость"как гейзер" выбрасывались примерно на 6 м выше верха выпускной трубы, стекали вниз и образовывали лужи вокруг основания продувочного барабана и выпускной трубы. Было видно, как испарения поднимались от этих луж. Сигнализация верхнего уровня F-20 сработала в первый раз в 13:20. Предупрежденные радиосообщениями и криками, несколько человек персонала в зоне установки изомеризации удалились на безопасное расстояние до того, как пары воспламенились. Аварийные звуковые сигналы не сработали. Один из свидетелей видел автомобиль-пикап, припаркованный несколько севернее продувочного барабана и выпускной трубы, с набирающим обороты двигателем и светящимися выхлопными газами. Однако неизвестно, являлся ли он источником возгорания. В 13:20 произошел мощный взрыв, в результате которого была повреждена установка изомеризации, что явилось причиной ряда вторичных выбросов углеводородов и пожаров, рис. 3. Из-за взрыва погибли 15 человек и свыше 70 человек получили ранения.
Рис. 3. Продувочный барабан и установка изомеризации после аварии Местная группа по ликвидации чрезвычайных ситуаций отреагировала незамедлительно и развернула поисково-спасательные операции. Были запрошены и к 13:45 мобилизованы дополнительные ресурсы и спасательная авиация. Подача сырья в Колонну не была перекрыта и прекратилась только в 14:45, когда отключилась электроэнергия. Пожары были локализованы через 2 часа после взрыва, а пострадавшим оказана помощь. К 16:44 кареты скорой помощи и самолеты санитарной авиации покинули место происшествия. Примерно в 23:00 под обломками было найдено последнее тело.
АНАЛИЗ ПРИЧИН С использованием собранной информации был проведен анализ непосредственных и системных причин взрыва. Информация была разложена на отдельные элементы событий или условий, из которых выделены ключевые факторы, то есть те события или условия, устранение которых могло бы предотвратить или уменьшить вероятность взрыва либо снизить степень его тяжести. Для каждого ключевого фактора были определены возможные непосредственные причины и возможные причины системы управления.
Утечка Действия, предпринятые либо не предпринятые, привели к переполнению колонны рафината, последующему превышению допустимого давления и сбросу давления. Поток углеводородов устремился к продувочному барабану и выпускной трубе, что привело к переливу жидкостей через вытяжную трубу, вследствие чего образовалось облако пара, которое воспламенилось от неизвестного источника. Основными причинами утечки были: недальновидность решений и неудовлетворительное выполнение процедур.
Применение знаний и навыков при запуске отгонной колонны рафината Неправильное выполнение процедур запуска способствовало потере контроля над процессом. Главные действующие лица (руководство и операторы) не применили свой уровень навыков и знаний, во время запуска не было на месте достаточного числа проверяющих и контролирующих лиц. Причинами этого послужили: неправильная модель контроля, противоречивость ролей и обязанностей, усталость персонала.
Контроль места проведения работ и размещения вагончиков Многочисленный персонал, работающий на остальных объектах НПЗ, находился слишком близко к продувочному барабану и выпускной трубе, которые являлись источником опасности во время операций запуска. Люди были скучены внутри или вокруг временных вагончиков и не были ни эвакуированы, ни предупреждены. Основными причинами стали: неудовлетворительное руководство и обмен информацией между рабочими группами, неверное определение опасностей на рабочем месте.
Конструкция продувочного барабана и выпускной трубы Использование продувочного барабана и выпускной трубы как части системы сброса и вентиляции колонны рафината после неоднократного внесения изменений в конструкцию и режим эксплуатации близкий к зоне неконтролируемых ситуаций. Непосредственными причинами были: не отвечающая требованиям конструкция, неудовлетворительное устранение опасностей на рабочем месте, неадекватная оценка параметров работы.
УРОКИ, ИЗВЛЕЧЕННЫЕ ИЗ ПРОИСШЕСТВИЯ Значительное число возможных причин системы управления, приведенных выше, указывает на существование комплексных вопросов, требующих дальнейшей оценки. Чтобы понять, какие рекомендации могли бы предотвратить повторение происшествия, было решено более глубоко рассмотреть основные вопросы культуры производства.
Производственный контекст В случае аварии в г. Техас на предприятии не были четко расставлены приоритеты безопасности производственного процесса. Внимание было сосредоточено на экологической безопасности и безопасности персонала, а не на безопасности производственного процесса. В линейной структуре организации имелась малая возможность обеспечения безопасности производственного процесса. Профессиональное развитие сотрудников не являлось приоритетным, обучение персонала было недостаточным. Вследствие этого сотрудники не видели для себя перспективы. Со временем рабочая обстановка разрушилась, что привело к сопротивлению изменениям, отсутствию доверия, мотивации и понимания цели. В сочетании с нечетким пониманием действий управленцев это означало, что не было последовательного выполнения правил, отсутствовала дисциплина, и сотрудники не чувствовали за собой полномочий, чтобы предложить улучшения или взять на себя инициативу в их осуществлении. Это привело к слабой мотивации сотрудников, которые знали, что не в их силах что-либо изменить. Можно назвать несколько причин, приведших к такой ситуации:- отсутствие требовательности в отношении соблюдения процедур и т.д.; - отсутствие образцов для подражания на уровне начальника смены и мастера; - невысокий уровень ожиданий в отношении поведения и результатов работы; - отсутствие последствий при хороших либо плохих результатах работы; - структура заработной платы привела к непреднамеренным обстоятельствам; - внутренняя направленность взглядов на уровне завода и участка; - отсутствие завершения работ, доведения их до конца; - отсутствие контроля действий; - боязнь возразить и сказать "нет"; - отсутствие взаимодействия, командной работы. В ходе нескольких предыдущих проверок было выявлено, что инструкции не выполняются, но ни на уровне начальника смены или руководства, ни на уровне оператора не было никаких последствий за такие действия. Отсутствовало конкретное и четко сформулированное описание действий, требуемых от руководящего персонала всех уровней, что подтверждалось отсутствием начальника смены во время ключевых событий, таких как ответственные моменты передачи смены во время процедуры запуска. Руководители низшего и среднего звена не закрепили понимание важности соблюдения инструкций. Во время последнего осмотра в оборудовании, которое является критичным для обеспечения безопасности, была обнаружена заметная коррозия и внутренние повреждения. Однако ремонт не был выполнен, а заявка на проведение ремонта впоследствии не была выписана. Также сиграла свою роль система заработной платы, которая поощряла руководителей низшего и среднего звена и операторов работать в течение более длительного времени, без учета фактора усталости. Сотрудники чувствовали, что предложения по улучшению дел не ценятся, и со временем они перешли к простому, бездумному выполнению указаний. Подход типа "проверь ящик", такой как регламентная проверка в процессе технического обслуживания, указывал на слабую мотивацию и нежелание выходить за рамки минимально необходимого выполнения требований, а иногда сотрудники пренебрегали даже этим минимумом. Направленность "в себя", замкнутая среда привели к тому, что корпоративным инициативам уделялось недостаточное внимание, поскольку руководством была допущена и распространилась позиция персонала "не нами придумано". Уроками, извлеченными из происшествий на других предприятиях, на данном заводе пренебрегали.
Безопасность в качестве приоритета Приоритеты безопасности производственного процесса, производственных показателей и систематического снижения риска не были обозначены и последовательно не закреплялись руководством. Надежная безопасность обеспечивается оптимальной линейной организацией производства, подкрепляемой должной культурой производства и ценностями безопасности. Качество основных производственных операций упало до уровня, когда реально требовалось вмешательство по вопросам безопасности, с тем чтобы обеспечить выполнение правильных действий. Подтверждение тому: пересмены бригад проводились неадекватно, процедуры не соблюдались, а линейные руководители не были в курсе проводимых операций. Отсутствовали какие-либо доказательства наличия комплексных и последовательно реализуемых бизнес-планов по уменьшению производственных рисков на объектах. Существующие планы делали упор на сокращение травм среди персонала и соблюдение экологических норм, но не предусматривали мероприятий по систематическому уменьшению производственных рисков или улучшению основных производственных операций. Например, не предусматривалось ограничение или отказ от использования вытяжных труб, выпускающих продукты вентиляции в атмосферу. Рассматривался проект модификации F-20, чтобы произвести подводку к факельному хозяйству, но он развития не получил, так как упор делался на решение проблем защиты окружающей среды. Ряд опрошенных работников отмечают, что вопросы безопасности не были приоритетными, особенно в сравнении с управлением затратами. Хотя руководство заявляло, что “безопасность превыше всего”, это ничем не подтверждалось и в это не верили многие работники. Отсутствие видения со стороны руководства и плохая связь внутри сложной разобщенной организации не способствовали доведению нужной информации. Пример тому - отсутствие докладов (в некоторых случаях) и расследования (в большинстве случаев) происшествий с утечками и нарушений технологии производства. Не было четких планов по укреплению организационного потенциала на предприятии. Требуемое обучение соблюдению норм проводилось, но не хватало подготовки и обеспечения роста в полном объеме руководителей низшего звена и подразделений. Больше всего это проявлялось в случае с руководителями подразделений по активизации процессов, чья программа обучения и развития была слабой или вообще отсутствовала. Низкий уровень подготовки руководящих кадров, видимо, отрицательно сказался на связи руководства с персоналом и его поведении. В целом, чем ниже уровень организационной структуры, тем меньше ясности в понимании приоритета безопасности и перспектив нефтеперерабатывающего предприятия. В результате у многих служащих бытовало мнение о том, что бесполезно затрагивать вопросы безопасности или думать о дальнейших действиях, а это, в конечном счете, отрицательно сказывалось на моральном климате и не вызывало чувства гордости за предприятие.
Организационная сложность и потенциал Многочисленные изменения в сложной организации привели к отсутствию строго разграниченной подотчетности и слабому обмену информацией. Все вместе вызвало путаницу персонала относительно распределения ролей и ответственности. Предприятие в Техасе является крупным и комплексным объектом с многоуровневой организацией, очевидно, предназначенной для обеспечения широкодиапазонного управления. Эта организация имеет много степеней взаимодействия, требующих четкой подотчетности и связи, как по горизонтали, так и по вертикали. В реальности были обнаружены примеры отсутствия подотчетности, нечеткого понимания ролей и ответственности, а также плохой связи со служащими, работающими в изолированных условиях. Это, в свою очередь, создавало неразбериху в некоторых линиях взаимодействия. В итоге рабочая среда была перегружена множеством процессов, работой разных комитетов и т.п., где было относительно легко упустить из вида основные требования к безопасности производства. Имелось множество примеров нечеткой подотчетности среди рабочих групп; например, относительно того, кто отвечал за участок между установкой изомеризации и установкой десульфации нафты, где располагались поврежденные вагончики. Таким же образом на вопрос, кто отвечает за размещение вагончиков на этом участке, звучали различные ответы. Нет доказательств того, что о пуске отгонной колонны рафината сообщили соседним производственным подразделениям. Один работник заявил, что подрядчики, работавшие внутри батареи кубов установки изомеризации, были уведомлены и предупреждены о необходимости покинуть участок, но на территории складирования катализаторов, прилегающей непосредственно к этому участку, никто не позаботился о том, чтобы оповестить или эвакуировать людей из вагончиков. Организация осуществляла производственную деятельность и как бы состояла из изолированных бункеров, отделенных стенами друг от друга. Взаимодействие между производственным и инженерно-конструкторским персоналом было непоследовательным и непостоянным. Об этом свидетельствует тот факт, что инженерных работников не вызвали для решения проблем с пуском; не было также повседневных обходов участков производства инженерными работниками. Кроме того, “независимые” функции, такие как обучение и безопасность производственного процесса, не получали должного обеспечения и не обладали влиянием, необходимым для соблюдения требований соответствующих стандартов. Совещание у руководителя смены должно было быть ключевым средством взаимодействия между подразделениями, но присутствие на нем не было обязательным, а обсуждение круга вопросов, касающихся всего предприятия, сокращалось примерно до 15 минут, что недостаточно для настоящего общения. Обмен информацией интенсивнее всего проходил в пределах рабочих групп, но не распространялся по горизонтали и вертикали. Недостаточная работа с руководителями низшего звена способствовала отсутствию ясности и плохой связи из-за низкого качества руководства со стороны задействованных лиц. Положение осложнялось тем, что не получали вознаграждения и признания те, кто выходил за привычные границы и осуществлял персональное руководство. Такая сложная обстановка привела к возникновению организации, где требовалось преодоление разобщенности между разными группами и компаниями.
Неспособность видеть риски Низкий уровень информированности о возможных опасностях и недостаточное понимания безопасности производственного процесса приводил к тому, что персонал допускал более высокую степень рисков, чем в других сопоставимых производственных условиях. Хотя были предприняты некоторые попытки повысить уровень информированности и понимания безопасности производственного процесса в начале 90-х гг., когда Управление США по охране труда и производственной гигиене ввело правила обеспечения безопасности производственного процесса, базовая система обучения в этой области не обновлялась на протяжении всех прошедших лет. Не было постоянно действующей программы обучения опасным факторам и рискам производства и их определению для операторов, руководителей и менеджеров; отсутствовал план снижения рисков. На нефтеперерабатывающем предприятии не было действенных и цельных планов систематического снижения рисков. Примером этого является отсутствие плана окончательной замены или перекомпоновки системы вытяжных труб на объекте. Последняя оценка вероятности крупной аварии на объекте не коснулась риска, связанного с вытяжными трубами. Установка изомеризации и связанная с ней вытяжная труба не вошли в список 80-ти отмеченных максимальных рисков. Таким же образом в ходе регламентной проверки размещения вагончиков не был учтен опасный фактор вытяжной трубы, находившейся на расстоянии 46 м. Следствием этого стало размещение временных вагончиков на удалении 46 м от вытяжной трубы, через которую проходила вентиляция углеводородов, более тяжелых, чем воздух, – без учета нормальной отраслевой практики. На объекте наблюдалось много примеров повышенной степени риска. Главное, что допускалось присутствие значительного числа автомашин в непосредственной близости от установок переработки углеводородов, а также широкое применение вагончиков для размещения людей. Это стало нормальной практикой. Во время расследования на НПЗ произошли еще несколько возгораний и серьезное происшествие на одной из установок. Общей реакцией персонала на них было отсутствие беспокойства, словно пожары являлись неотъемлемой частью жизни предприятия. Конечно, этому способствовало отсутствие расследования предыдущих случаев возникновения пожаров. В журналах ПАСС (Пожарной аварийно-спасательной службы) отмечались случаи пожаров, но к ним не прилагались документально оформленные отчеты о расследовании. К другим примерам толерантности в отношении высокой степени риска относятся: отсутствие анализа процедуры пуска ректификационной колонны с членами бригады, как это рекомендуется регламентом; отсутствие контроля в ходе пуска, хотя всем известно, что подобная операция сопряжена с высокой степенью риска; отсутствие докладов о серьезных нарушениях производственного процесса, как, например, подъем предохранительных клапанов во время предыдущих пусков. Все эти наблюдения свидетельствуют о высоком уровне рисков, ставшем привычным явлением, и о неспособности видеть основные риски технологического процесса.
Отсутствие оповещения на раннем этапе При плохой связи и управлении эффективностью производственной деятельности по вертикали не существовало ни должной системы раннего оповещения о возникших проблемах, ни каких-либо независимых механизмов, чтобы увидеть снижение стандартов. Пятый и последний вопрос культуры производства касался целостной системы раннего оповещения для случаев возникновения проблем в безопасности производственного процесса. Предприятие предпринимало многочисленные меры для отслеживания результатов производственной деятельности, соблюдения экологических норм, но не было четкого акцента на основные признаки возможных серьезных или крупных происшествий. Проводились многочисленные проверки в соответствии с требованиями нормативных и законодательных актов и корпоративными требованиями. Но при существующем стиле работы не удалось определить системные проблемы: - плохая связь по вертикали; - наличие многих ключевых показателей эффективности, не обладающих прозрачностью или полезных для обнаружения утечек, показывающих улучшение в плане снижения численности регистрируемых травм; - проверки были ориентированы на производственный процесс и не были подтверждены ответными действиями. Меры безопасности были в основном ориентированы на охрану труда в плане регистрируемых травм. Складывалось представление, что положение дел с промышленной безопасностью на предприятии улучшается. Не было четкой ориентации на принятие мер в отношении безопасности производственного процесса, таких, которые касаются запаздывающих показателей утечек, воспламенения углеводородов и нарушения производственного процесса. Руководство предприятия не делало упор на анализ тенденций, которые могли бы точно отразить ситуацию с безопасностью на предприятии. Происшествия с утечками и происшествия, вызванные нарушением производственного процесса, не привлекали должного внимания. О многих случаях даже формально не докладывалось, не проводились расследования, а стало быть, не были определены и предприняты необходимые корректирующие мероприятия. Группой расследования было просмотрено множество аудиторских отчетов, показавших, что проверки проводились формально. Отчеты подтверждали, что проверки сосредотачивались в основном на анализе процессов и документации. За исключением проверки правил техники безопасности “Большой четверки”, ни один из них не делал упор на проверку и не оценивал, например, соблюдались ли установленные методики, соответствовал ли производственный режим этим методикам.
«РАБОТА НАД ОШИБКАМИ» В отчете о расследовании было определено большое количество рекомендаций специально для НПЗ в Техасе, и особенно в отношении установки изомеризации. Руководство предприятия разработало приоритетные планы по выполнению всех рекомендаций, часть наиболее срочных задач уже решена.
Меры по совершенствованию навыков и поведения персонала: - назначен новый управляющий предприятия и создана новая должность в руководстве для обозначения приоритетов и отслеживания основных инициатив на объекте; - упрощена организационная структура с тем, чтобы каждый человек, занятый в обслуживании и производстве знал, за что и перед кем он отчитывается; - разъяснены и закреплены роли, ответственность и ожидаемые результаты касательно процедур пуска, эксплуатации, обслуживания и эвакуации; - начали осуществляться действия по обеспечению обучения и обмену информацией, направленные на соблюдение правил персоналом в рамках всего предприятия; - начата программа по разработке и осуществлению интенсивного обучения операторов и руководителей низшего звена; - нанята консалтинговая фирма для оказания помощи руководству в разработке и создании благоприятного климата на рабочих местах; - осуществлено совмещенное расположение руководства в одном офисе для обеспечения лучшего обмена информацией; - назначен вице-президент группы по безопасности и производственному процессу для совершенствования в сфере управления охраной труда, охраной окружающей среды и промышленной безопасности.
Меры по обеспечению безопасной эксплуатации оборудования: - начата непрерывная проверка и оценка нефтеперерабатывающего предприятия сверху вниз; - выведены из производственного цикла установки высокого давления (свыше 68 атм.) и проводится их основательный анализ. Установки не будут запущены, пока не признаются безопасными для эксплуатации; - предъявлены требования к руководителям: присутствовать на всех пусках и выводах из эксплуатации, а также при других важных операциях, включая письменную передачу смены ее начальником; - усилен контроль над процессом утверждения работ, чтобы гарантировать прекращение работы в случае наличия отклонений; - арендованы офисные помещения общей площадью 9300 м2 в Техас-Сити для служащих, чьи функции не требуют их присутствия на предприятии; - проведена проверка предохранительных клапанов на всех технологических установках, а также анализ предохранительной и факельной систем; - начат процесс по замене вытяжных труб факелами;- по договору подряда нанята фирма для оказания помощи в оценке и улучшении процессов текущего технического обслуживания; - проводится анализ норм управления с акцентом на роли важнейших руководящих должностей.
Меры по совершенствованию политики безопасности: - ликвидированны временные офисы в вагончиках с территории объекта; - сокращено количество автомашин, пропускаемых на территорию НПЗ; - назначено проведение проверки правильности процедур пуска, остановок и соблюдения безопасности;- нанят консультант для оказания помощи по управленческой информации для безопасности производственного процесса; - проводится обучение служащих интенсивному обмену информацией о действиях в нестандартных ситуациях и применению звуковых сигналов оповещения.
ВЫВОДЫ Происшествие представляло собой взрыв, вызванный накоплением паров углеводородов тяжелее воздуха, воспламенившихся в результате контакта с источником возгорания, возможно от работающего двигателя автомашины. Углеводороды образовались от перелива жидкости из вытяжной трубы после срабатывания системы защиты от избыточного давления, вызванного переполнением и перегревом содержимого колонны отгона рафината. Невозможность обеспечения слива жидкости из колонны и неспособность предпринять эффективные аварийные меры привели к утечке, предшествовавшей взрыву. Все это свидетельствовало о несоблюдении установленных правил и инструкций. Руководство установки не присутствовало при этом и не смогло обеспечить соблюдение необходимой процедуры, что уже стало правилом и обычной практикой в повседневной деятельности на данном предприятии. Серьезность происшествия усугублялась присутствием множества людей, находившихся около и внутри вагончиков, не к месту расположенных вблизи от вытяжного устройства. Вероятность данного происшествия была бы меньшей, если бы было прекращено использование вытяжной трубы для легкой фракции углеводородов и вместо нее было установлено гораздо более безопасное устройство.
Причины, лежащие в основе поведения и действий, наблюдавшихся в ходе происшествия, были сложными. Очевидно, что они накапливались в течение многих лет, и для их устранения потребуются согласованные меры. Настоящая статья первоначально была представлена на Мировом конгрессе безопасности производственного процесса (Орландо, Флорида, США, апрель 2006 г.) и опубликована в журнале "Химия и бизнес" |