Рис.5: Конструкция системы фильтрации типа SFXmagnus 1 -защитный кожух, 2-привод, 3-диск фильтра, 4-дверца для замены сеток, 5-углубление для сеток, 6-канал расплава, 7-блок фильтра Пошаговый поворот диска позволяет ввести в область канала расплава небольшую, очень узкую чистую зону фильтрующей сетки и одновременно вывести из канала равную ей загрязненную часть. Благодаря этому, активная фильтрующая площадь всегда остается неизменной. При этом гарантируется автоматическая замена загрязненных фильтрующих элементов без отрицательного влияния на текущий технологический процесс. Использованные фильтрующие элементы затем удаляются вручную через легкодоступную зону, расположенную в левой части входного блока системы. Преимущества системы фильтрации SFXmagnus Постоянные активные площади фильтрации отсутствие скачков давления, вызванных уменьшением площади фильтрации при замене сеток; постоянные параметры конечного продукта и производственных допусков Возможность контроля давления при общем его низком уровне снижение термической нагрузки на расплав материала и уменьшение давления на привод экструдера; улучшение качеств расплава и конечного продукта, а также достижение их стабильности; увеличение срока службы экструдера. Использование всех фильтрующих элементов на диске (в зависимости от размера фильтра от 10 до 13 ) при автоматизированном режиме работы одновременная замена всех фильтрующих элементов; снижение частоты замены фильтрующих элементов и времени на обслуживание фильтра; отсутствие нарушений производственного процесса при замене фильтрующих элементов. Механизм автоматического заполнения фильтра полимером исключение попадания воздуха в расплав; непрерывное пошаговое перемещение диска; предоставление в распоряжение больших активных площадей фильтрации в течение короткого периода времени, например, при увеличении объёма загрязнений; возможность увеличения доли вторичных материалов. Отсутствие «мертвых зон» исключается термическая деструкция полимера. 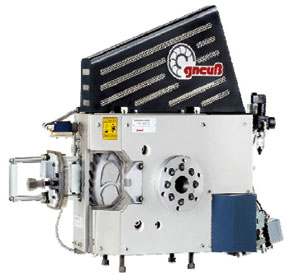
Рис. 6: Работающая в непрерывном и полностью автоматизированном режиме система фильтрации SFXmagnus (запатентована) Преимущества обеих ротационных (Rotary) систем фильтрации ощутимы. Наряду с длительной чистотой расплава гарантируются минимальные колебания давления благодаря постоянству активных площадей фильтрации. Таким образом, на протяжении длительного времени гарантируется неизменно высокое качество продукции. Скачки давления в других ситопеременных системамах фильтрации ведут к неравномерной толщине изготавливаемой пленки, осложняя процесс переработки пленочного полотна. Равномерность толщины является существенным показателем качества хорошо изготовленной пленки. Кроме того, работающий с постоянным давлением ротационный фильтр существенно снижает производственные допуски на толщину пленки. Примеры из практики ПЭТ - пленка для дальнейшего термоформования Одна из североамериканских фирм, производящая ПЭТ - пленку методом глубокой вытяжки для дальнейшего термоформования, использует на линии производительностью 1000 кг/ч фильтр типа RSFgenius 150. При этом перерабатывается смешанное сырьё в виде 25% первичного сырья и 75% собственного рециклята . Для прозрачной пленки тонкость фильтрации составляет 75 μm. Несмотря на высокую долю рециклята, смена комплекта сеток, благодаря эффективному интегрированному механизму очистки, проводится лишь через 4 мес. При этом автоматически происходит 250 - кратное их повторное использование. 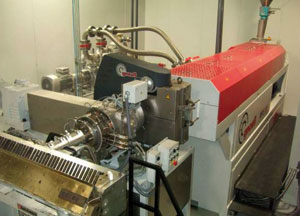
Рис. 7: RSFgenius 150 на линии по производству ПЭТ - пленки Перепад давления неизменен и составляет 50 (±2) бар, что способствует равномерности толщины пленки и уменьшению расхода сырья. Отпадает необходимость в последующей настройке толщины. Полистирольная плёнка глубокой вытяжки Один из клиентов - производитель термоформовочной пленки из ударопрочного полистирола (HIPS) - установил на линии производительностью 900 кг/ч в час систему фильтрации SFXmagnus 75 с фильтрующими элементами 200 μm. Изготовленная методом глубокой вытяжки пленка перерабатывается на том же предприятии на термоформовочных машинах. Отрезки краев пленки и отходы термоформовочной высечки используются повторно при экструзии пленки. Фильтр SFXmagnus эксплуатируется в полностью автоматизированном процессе. Это означает, что все вложенные в диск десять сеток используются равномерно и будут одновременно заменены. Активные площади фильтрации остаются неизменно большими. Благодаря одновременной смене всех вложенных в углубления диска сеток, максимально снижаются трудозатраты по обслуживанию фильтра. Несмотря на значительную долю вторичного сырья и отсутствию системы обратной промывки, замена сеток производится лишь через каждые три дня. Естественно, процесс смены сит ни в коей мере не нарушает технологический процесс производства. ПЭТ - пленка из PET Bottle Flakes 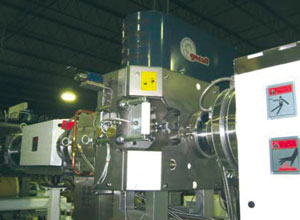
Рис. 8: Система фильтрации SFXmagnus 75 на линии по производству термоформовочной пленки Южноамериканский производитель и поставщик ПЭТ - пленки применяет на линии производительностью 500 кг/ч систему фильтрации RSFgenius 90. Смешанное сырье состоит из 20 % отходов пленки и 80 % ПЭТ - хлопьев (PET Bottle Flakes). Тонкость фильтрации для производства прозрачной пленки установлена от 75 до 125 μm. Благодаря встроенной системе обратной промывки, фильтрующие элементы в полностью автоматизированном режиме 180 раз очищаются и повторно используются. Несмотря на значительную долю используемых ПЭТ - хлопьев, а также их сильную загрязнённость, замена комплекта фильтрующих элементов проводится не чаще, чем каждые 15 - 25 дней. Непрерывный процесс производства, значительное улучшение уровня равномерности толщины плёнки (при малой толщине плёнки в среднем) и уменьшение отходов производства, которым способствовала модернизация линии путем внедрения системы фильтрации RSFgenius, повысили производительность линии в целом на 25 %. Более того, уменьшился объем рекламаций от потребителей. Термоформовочная полипропиленовая пленка Изготовитель термоформовочной плёнки из ПП использует на коэкструзионной линии на одном 5“ экструдере фильтр SFXmagnus 90 с производительностью 850 кг/ч и на одном 4.5“ экструдере фильтр SFXmagnus 75 - 630 кг/ч. При этом перерабатывается смешанное сырьё из первичного и вторичного материалов с тонкостью фильтрации 200 μm. В прошлом, при каждом процессе замены сит происходили нарушения процесса производства или же выпускалась бракованная пленка. С внедрением обоих фильтров типа SFXmagnus было достигнуто непрерывное, стабильное производство и в ходе смены фильтрующих элементов. Это позволило ко всему прочему увеличить долю используемого рециклята и повысить общую производительность линии на 10 %. Заключение Благодаря внедрению ротационных систем фильтрации типов SFXmagnus и RSFgenius, возможно улучшить как качество конечной продукции, так и повысить эффективность производства в целом. Высокий уровень качества изготавливаемой пленки обеспечивается посредством использования систем фильтрации, работающих с постоянным давлением расплава и обеспечивающих равномерность толщины пленки и молекулярной массы полимера. Помимо этого они позволяют осуществлять более тонкую качественную фильтрацию без нарушения процесса производства и при смене сит. Благодаря непрерывному и бесперебойному процессу производства, возможно повышение коээфициента использования оборудования в среднем на 10 %. Эти результаты с рациональной точки зрения ведут к короткому сроку амортизации фильтрационных систем, срок их окупаемости при производстве плёнок составляет в основном не более одного года. Это достигается как при установке ротационных систем на новую линию, так и при перевооружении ими действующего оборудования. Тип фильтра RSFgenius с интегрированной системой обратной очистки фильтрующих элементов в отличие от типа фильтра SFXmagnus эффективна на тех видах производства, при которых используется сильно загрязнённое сырьё или/ высокий уровень автоматизации процесса, например, при производстве очень тонкой плёнки или при поточно-линейной Inline–технологии термоформования. Возрастающее в последнее время использование PET Bottle Flakes с целью снижения материальных затрат, нуждается в высокотехнологичной передовой фильтрации, безусловно реализуемой при внедрении системы RSFgenius. Д-р Моника Гнойсс, Gneuss Kunststofftechnik GmbH
Gneuß Kunststofftechnik GmbH Источник: Пласткурьер
|