Для того, чтобы избавиться от необходимости каждый раз создавать электрод нужной длины, электродные пластинки разрезаются на части и устанавливаются на стержень так, что при изменении ширины полотна, эти части могут отодвигаться от заземленного ролика, подгоняя длину электрода под ширину полотна (см. рисунок 13). В настоящее время используется множество таких электродов. У такой конфигурации электродов целый ряд и преимуществ, и недостатков. 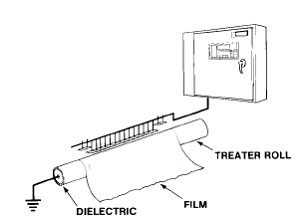 Рисунок 13. Сегментированный металлический электрод
При установке секционированного электрода непосредственно над заземленным роликом, сегменты будут отодвигаться в сторону, если при прохождении над заземленным роликом будет образовываться складка или соединение шире искрового промежутка, а затем они возвращаются на место, после того, как складка или соединение продвинуться мимо. Еще одним преимуществом секционированного электрода является его способность приподнимать центральные сегменты и обеспечивать обработку полосами. При использовании более ранних моделей электродов толстое соединение, ударившее электрод, могло вызвать его повреждение. Еще одним недостатком является то, что озон, образовывавшийся при коронном разряде, вскоре создавал отложения оксида алюминия между сегментами, из-за чего они оставались в положении, не производящем обработки. Этой проблемы можно до некоторой степени избежать, если нанести твердое покрытие или анодирование на сегменты. Еще больше улучшить процесс поможет использование нержавеющей стали в качестве материала для электродов. Это может практически исключить прилипание сегментов или коробление электрода. Последним недостатком этой конфигурации является возможность неоднородной обработки полотна. Подложка, которая подверглась неравномерной обработке, может создать проблемы при склеивании или термогерметизации при нанесении печати, нанесении экструзионных покрытий, иных покрытий и при ламинировании. Неравномерность обработки была значительно уменьшена с помощью нарезания сегментов по диагонали для предотвращения обработки полосами между сегментами. Система с использованием закрытых роликов, в которой используется диэлектрический закрытый ролик либо с пластиночным, либо с секционированным электродом, также создает проблемы с размерностью. Для того чтобы осуществлять надлежащую обработку всей ширины полотна и рассеивать тепло, вырабатываемое в ходе процесса обработки, диаметр закрытого ролика должен увеличиваться пропорционально увеличению общего объема прикладываемой энергии. Накопление тепла на закрытых роликах может нанести большой ущерб, его можно уменьшить только за счет увеличения диаметра ролика для того, чтобы обеспечить период охлаждения между циклическим размещением под электродом. Кроме того, для обеспечения удаления озона и безопасности оператора, сама станция в целом должна увеличиваться в размере по мере увеличения диаметра ролика. На рисунке 14 даны требования к диаметру ролика в зависимости от прилагаемой энергии (кВт). 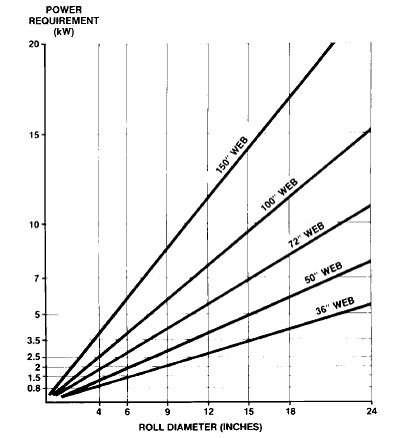 Рисунок 14. Прилагаемая энергия (кВт) и диаметр ролика (дюйм).
|