6. Карбонаты 6.1 Бикарбонат натрия (NaHCO>3) Бикарбонат натрия + лимонная кислота Карбонат цинка (ZnCO3) Бикарбонат натрия (NaHCO3) представляет собой белый порошок, широко известный как пищевая сода. Температура разложения 1300-1800С, выход углекислого газа составляет 125 мл/г. В процессе разложения также выделяется вода. Бикарбонат натрия гигроскопичен, что следует учитывать при хранении продукта. Цинка карбонат (ZnCO3) - высокотемпературный вспенивающий агент с основным выделяющимся газом - диоксидом углерода. Используется при литье под давлением чувствительных к аммиаку полимеров, таких как поликарбонаты. Реакция разложения карбонатов и бикарбонатов является эндотермической. 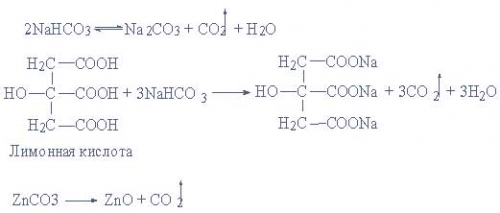 Неорганические вспенивающие агенты на основе карбонатов и бикарбонатов являются одними из самых «старых» и самых дешевых соединений в группе вспенивающих добавок. Однако относительная простота этих соединений компенсируется сложностью работы с ними. Во-первых, выделяющаяся при реакции вода отрицательно влияет как на процесс переработки, так и на свойства готового изделия, поэтому очень часто вспенивающие агенты на основе карбонатов и бикарбонатов используются совместно с поглотителями влаги (десикантами). Во-вторых, из-за высокой скорости диффузии диоксида углерода образуется хрупкая структура с большим количеством крупных и открытых пор, которая не может использоваться для гибких материалов. Получение и переработка вспененных материалов. Наилучшие результаты вспенивания достигаются в аморфных материалах (таких, как полистирол), поскольку макромолекулы таких полимеров образуют большое количество зацеплений, служащих зародышами образования пузырька, что позволяет получать однородные микропористые пены с высокими изоляционными и физико-механическими свойствами.
Высококристаллические полимеры – полипропилен, ПЭТ, ПЭВП, полиамид – намного сложнее для вспенивания из-за плотной укладки макромолекул. Вспенивание таких материалов относительно новый процесс, начавший активно развиваться в последние 10 лет. Для того, чтобы улучшить качество вспененных изделий из высококристаллических термопластов производители сырья разработали специальные марки с большим количеством боковых ответвлений. Получение таких марок стало возможным благодаря изобретению металлоценовых катализаторов. К таким материалам относится полипропилен с высокой упругостью расплава (High Melt Strengths Polypropylene). Несмотря на разнообразие методов и используемых материалов процесс вспенивания состоит из 3 стадий: зарождение газового пузырька, рост и стабилизация пузырьков, фиксирование структуры газосодержащего материала. Зарождение газовой фазы происходит, как правило, на гетерогенных центрах (флуктуации плотности) или на твёрдых высокодисперсных наполнителях, вводимых в качестве зародышеобразователей. Работа расширения газа внутри пузырька затрачивается на образование новой поверхности и на преодоление вязкого сопротивления полимера. Чем больше образуется пузырьков, тем более однородной будет структура. При вспенивании, одновременно с ростом пузырька, приводящего к уменьшению поверхности раздела фаз, происходит слияние пузырьков и утечка газа через стенки. Скорость диффузии определяется химической природой газа и структурой полимера. Неполярные газы (N2) обладают незначительной диффузией и растворимостью в полярных полимерах (ПА, ПС). Газопроницаемость полимеров снижается с увеличением степени кристалличности и полярности. Фиксация структуры при переработке термопластов происходит в момент охлаждения изделия. В связи с тем, что вязкость системы непрерывно возрастает в процессе охлаждения, газовые пузырьки не достигают максимального размера во всём объёме полимера. Параметры структуры материала определяются кинетикой роста газового пузырька и кинетикой нарастания вязкости, что приводит к образованию полидисперсной структуры. Эмпирически доказано, что для получения качественных экструзионных и литьевых изделий рекомендуется использовать высоковязкие марки и проводить процесс с резким изменением температурного профиля, для того чтобы обеспечить гомогенное перемешивание и вспенивание в 3-ей технологической зоне (зоне гомогенизации) экструдера.
|