Интегрированное решение Пятитонная полностью электрифицированная установка от Battenfeld, названная Microsystem, является одной из первых коммерческих моделей, предназначенных специально для микроформования. Представленная в октябре 1999 г. она на сегодняшний день является единственной моделью на рынке, которая сконструирована как полностью автоматизированная формовочная производственная ячейка с возможностями для осуществления впрыска, замены инструмента и погрузки/разгрузки деталей, интегрированными на одну установку, имеющая свою собственную чистую комнату. Установка дает массу впрыска от 0.25 мг. до 1 г. при массе деталей менее 0.008 г. 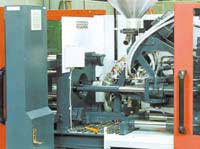
В новой установке Micro Injection от компании Ferromatik Milacron используется двухэтапный шнеково/плунжерный впрыск для формования деталей размером до 1 мг. Необычная трехэтапная инжекционная система (см. схему) начинается со стационарного экструдера с диаметром 14 мм и отношением длины и диаметра 14:1 при наклоне на 45°. Она непрерывно подает материал в вертикальную дозирующую камеру. В камере имеется плунжер 5 мм в диаметре, который отталкивается в момент, когда на него воздействует входящий поток расплава. Датчик давления показывает, когда положение поршня достигает заданного объема впрыска. Как утверждают в Battenfeld, очень точное, сервоприводное дозирование с контролем давления позволяет осуществлять управление размером впрыска с точностью в переделах до 0.001 куб. см. После этого пневматический поршень доставляет расплав в инжекционную камеру. Плунжер литьевой машины, который приводится в действие сочетанием сервопривода и механического автоматизированного модуля, впрыскивает расплав со скоростью 760 мм в сек. Расплав течет через внутренне разогретое литьевое отверстие, которое выступает через стационарную плиту до линии разъема пресс-формы. Наличие вращающегося формовочного стола с двумя половинами формы позволяет осуществлять одновременную инжекцию и извлечение предыдущего впрыска. В пресс-формах имеются взаимозаменяемые вставки гнезд, изготовленные с использованием технологии, разработанной в Германии, и называющейся LIGA (рентгенолитография и электроосаждение). В компании Battenfeld говорят, что точность зажимного устройства без поперечной планки составляет до 0.01 мм. Специальная технология центрирования гнезда обеспечивает точность этих деталей. Выталкивающие шпильки, имеющие всего 0.2 мм в диаметре, выталкивают эти детали. Робототехническое устройство бокового размещения захватывает детали с помощью вакуумных присосок и доставляет их на станцию проверки, у которой имеется до 4 камер. 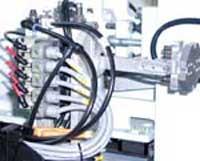
Пневматическое устройство извлечения от Battenfeld перемещает детали, не повреждая их. В компании Boy Machines предпочитают использование шнека возвратно-поступательного действия многоэтапному литью, что позволяет избежать образования мертвого пространства там, где происходит зависание расплава. У микроформовочного шнека от Boy имеется шаровой клапан вместо стандартного стопорного кольца. Для микроформования Boy предлагает полностью гидравлические модели с двумя плитами 12 M и 12 A (14.2 тонны). Как считают в компании, система управления более высокого уровня Procan CT,установленная на 12 A, лучше приспособлена к микроформованию. Возвратно-поступательный шнек с диаметром 14 мм и соотношением длины и диаметра 18:1 обеспечивает получение впрысков от менее 0.1 г до 5 г. Также имеются шнеки с диаметрами 16 или 18 мм. Расплав впрыскивается при 9.4 дюйма в секунду с давлением впрыска до 26,034 фунтов на кв. дюйм. "Мы используем усилитель для предварительной нагрузки насосов. Мы стараемся увеличить давление для изготовления микроформовочных применений", - говорит Шни. В число прочих устройств входит видеосистема для проверки деталей и конвейерная система отрицательного давления для транспортировки деталей. Компания Ferromatik Milacron Europe разработала свою линию установок Micro Injection для производства деталей с массой от 0.001 до 3 г. В ней имеется набор предпластификационного шнека с наклоном в 45° по отношению к плунжеру литьевой машины. Шнек с диаметром 18 мм и отношением длины и диаметра 15:1 работает на гранулах стандартного размера. Он дозирует расплав через перепускной шаровой клапан в плунжер литьевой машины, который выпускается с тремя размерами для массы впрыска от 2.263 до 5.588 г. По словам Планка из Ferromatik, плунжер с диаметром 7 мм дает обратный ход в четыре раза лучше, чем шнек с диаметром 14 мм, поэтому точность массы впрыска выше. "Конструкция плунжера также обеспечивает лучший контроль пиков давления, поэтому мы можем добиваться более низкого пикового давления во время перемещения", - говорит Планк. Конструкция инжекционного устройства таковы, что в ней нет острых краев или углов, чтобы исключить деградацию смолы. Установку можно использовать для двухкомпонентного формования.
|