Поверхность класса A и продолжительность цикла Для того, чтобы HPPC смогли стать конкурентоспособным продуктом для производства для горизонтальных панелей кузова, он должен продемонстрировать свою способность создавать поверхностное покрытие класса А. Кроме того, для того, чтобы HPPC смог стать экономически привлекательным для годового объема производства до 50,000 единиц, продолжительность цикла для детали с размерами, соответствующими размерам поверхностного слоя капота, должна быть около 2 минут. Одним из методов для достижения этого, который использовали в компании GE Plastics and Azdel, была технология переработки на основе Индуктивного нагрева в форме. 31 марта 2006 г. Azdel получила полную лицензию на использование Каркасной системы (торговая марка RocTool) для транспортных средств с покрытием класса A, изготавливаемых с использованием термопластических материалов при применении технологий термокомпрессии и термоформования. Срок действия этой полной лицензии равен сроку действия патентов. Azdel обладает правом предоставления этой технологии другим производителям для изготовления ими формовок для последующей сборки или готовых деталей. Azdel и GE Plastics работали с RocTool и своей новой технологией формования каркасной системы на протяжении примерно двух лет. На протяжении данного периода начальной разработки компании совместно спроектировали и ввели в эксплуатацию три инструмента для изготовления панелей внешней оснастки кузова с диапазоном размеров от инструмента для изготовления капотов автомобилей с масштабом 1:4 до инструмента для изготовления капота автомобиля в натуральную величину. На рисунке 5 показана деталь, сформованная в масштабе 1:4 , на рисунке 6 показан полноразмерный экспериментальный капот. 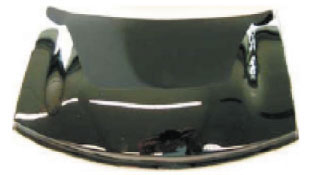 Рисунок 5: Капот 1:4
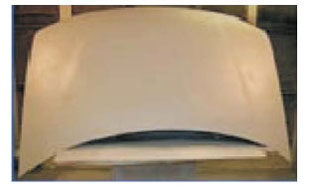 Рисунок 6: Экспериментальный капот в натуральную величину
Каркасная система использует электрическую индукцию для нагревания поверхности инструмента. Используется специальная конструкция инструмента для уменьшения термической массы нагреваемой части инструмента, поэтому можно добиться получения скоростных циклов для нагревания и охлаждения инструмента. Целью экспериментальной деятельности являлось уменьшение продолжительности цикла, которая необходима для производства панели кузова из термопластического композита класса А, примерно в 30 раз. Хотя эта цель пока еще не до конца достигнута, очевидно, что получение такого результата уже не за горами. Помимо использования Каркасной системы, GE Plastics создала сочетание устройств для реализации своей собственной технологии переработки с тем, чтобы приспособить технологию для изготовления крупных панелей кузова автомобиля с высокоскоростными циклами. Это сочетание получило название Индукционного формования. На рисунке 7 дана общая схема реализации данной технологии. 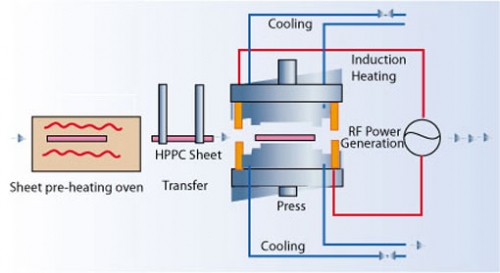 Рисунок 7: Общая схема технологии индукционного формования
Решающее значение для получения покрытия класса A имеет, наряду с технологией переработки, однонаправленный армированный поверхностный слой, используемый в конструкции HPPC. На протяжении второй половины 2005 г. и первого квартала 2006 г. проводилось углубленное сопоставление некоторых имеющихся технологий получения поверхностного покрытия с использованием имеющихся данных. Анализировалось несколько технологий, включая однонаправленные нити, жгуты тканых волокон, а также тканые переплетения волокон, в сочетании с технологиями изготовления на основе использования растворителя, суспензии, порошка, расплава, смешанных волокон и создания многоуровневых пленок. Было установлено, что наилучший результат можно получить при использовании однонаправленных нитей, которые обеспечивают надлежащее соотношение между механическими эксплуатационными характеристиками, эстетическими параметрами и затратами. Удар в область головы пешехода Для того, чтобы оценить эксплуатационные характеристики капота из HPPC, в Технической статье (продолжение страницы 5, рассмотрение законодательных актов о мерах по защите пешеходов) производилась оценка непроводящих HPPC с онлайновым окрашиванием с использованием испытаний для столкновений на большой скорости; было создано множество собственных решений конструкции внутренней структуры капота; эти решения в настоящее время оцениваются СAE с точки зрения эксплуатационных параметров для защиты пешеходов от удара в область головы. После того, как будет выбрана внутренняя конструкция, будет создан полноразмерный базовый (внутренний и внешний) капот, который будет испытан на производстве GE Plastics в Мока, Япония. Ожидается, что проверка эксплуатационных параметров для защиты пешеходов от удара в голову, будут закончены к концу 2006 г. Высокоскоростная характеристика материала дала очень многообещающие результаты, такие как: • Предел прочности на разрыв не изменяется существенно с изменением температуры; • Повторяемые параметры ударопрочности; • Параметры энергопоглощения с необходимыми параметрами жесткости и деформации, а также • Высокоскоростное испытание прочности на разрыв показало, что модуль остается тем же при различных нагрузках. Скорость относительной деформации материала показывает, что он не чувствителен к скорости нагрузки. «Зеленый» полиэфир PBT Стремясь существенно уменьшить выбросы газов, способствующих созданию парникового эффекта, во время производства пластмассовых смол, компания GE Plastics разработала свою собственную химическую технологию по переработке отходов из бутылок из PET в чистую смолу полиэфирного PBT . Можно будет использовать эту смолу PBT при производстве смеси Xenoy*, которая применяется при изготовлении вариантов HPPC с онлайновым окрашиванием. Это предоставит производителям автомобилей возможность изготавливать крупные панели кузова с существенным содержанием продукта, утилизированного после истечения срока эксплуатации. Заключение / Продолжение работы В области описанных разработок работа продолжается в нескольких направлениях, включающих: оптимизацию непроводящих HPPC с онлайновым окрашиванием; наращивание проводимости; разработка HPPC с автономным окрашиванием; оптимизация Индукционного формования для получения поверхности лучшего качества и уменьшения продолжительности цикла; оптимизация поверхностного слоя для получения лучшего качества поверхности; разработка конструкции деталей, моделирование и создание экспериментальных моделей для получения характеристик, необходимых для защиты пешеходов от удара в голову. Полученные на сегодняшний день первоначальные данные показывают, что HPPC могут стать очень конкурентоспособным и привлекательным решением для внедрения использования термопластов при производстве горизонтальных панелей кузова автомобиля. www.newchemistry.ru |