Экструзия представляет собой простую технологию, при использовании которой гранулы или порошки пластмассы расплавляются в непрерывную форму, которая продавливается через щелевую головку для получения нужной формы. В зависимости от формы щелевой головки, из экструдируемой заготовки можно производить разнообразные готовые продукты, включая гранулы, полосы и листы. Обычно экструдер состоит из бункерного загрузочного устройства, вращающегося шнека, помещенного в цилиндр экструдера, щелевой головки, который создает форму расплава, а также вспомогательных систем охлаждения, обрезания и удаления (см. рисунок 3).
Рис. 3. Схема обычного экструдера. Создание многослойных пленок для автомобильной промышленности требует некоторых дополнений к этой конфигурации для производства высококачественной пленки соответствующей толщины (см. рисунок 4).
Рис. 4. Схема экструдера для изготовления многослойной пленки. Для того чтобы изготовить пленку без гелевых пятен и прочих загрязнений, необходимо использовать распределительную решетку в головке экструдера с сеточным уплотнением. Сеточные уплотнения можно заменять автоматически с помощью устройства для замены сеток, позволяющего производить замену с незначительными остановками или же без остановки, без ущерба для качества пленки. Такие средства фильтрации также позволяют создавать обратное фильтрационное давление, которое облегчает процессы расплавления и смешивания. По всей экструдерной линии используются датчики давления, осуществляющие мониторинг обратного фильтрационного давления. Шестеренчатый насос, который может быть сконфигурирован на выходе экструдера, позволяет создавать постоянную скорость потока за счет обеспечения положительного объемного вытеснения экструдируемого вещества. Для того чтобы отслеживать несоответствия вязкости расплава, которые могут возникать под воздействием влаги, колебаний подачи в экструдере или вариативности подаваемого состава, можно использовать онлайновый реометр. Эта информация может подаваться непосредственно обратно на экструдер для того, чтобы производить автоматическую регулировку параметров температуры, скорости и потока. Каландрирование и полировка горячепрессованных порошковых заготовок позволяют создавать пленку с отличным блеском, необходимую для соответствия стандартам пленок класса A автомобильной промышленности. Воздушный шабер, который вдувает постоянную струю воздуха на каландерные вальцы, предотвращает усадку остывающей пленки. Продольно-резательный станок используется для подравнивания краев пленки так, чтобы она оставалась плоской на протяжении всей длины. Сканирующий датчик позволяет осуществлять мониторинг толщины пленки и обеспечивать сохранение ее вязкости. При использовании вышеуказанных смол можно создавать двухслойные и многослойные пленки. Количество слоев зависит от конфигурации щелевой головки и блока подачи, а также от числа используемых экструдеров. Для того чтобы изготовить двухслойную пленку из двух компонентов (A/B пленка), необходимо наличие двух отдельных экструдеров, а также блок подачи для направления экструдатов в одну щелевую головку. Простая двухслойная пленка обычно состоит из прозрачного слоя из экструдера "A" и окрашенного слоя, содержащего все цвета и красители, предназначенные для создания эффектов, которые необходимы для создания соответствия окраске жидкой краски, из экструдера "B". Можно также создавать трехслойные пленки (A/B/A)с помощью окрашенного слоя, размещенного между двумя прозрачными слоями, с использованием двух экструдеров (см. рисунок 5).
Рис. 5. Формирование трехслойной пленки типа А/В/А. Другой конфигурацией трехслойной пленки является производство с использованием трех различных составов (A/B/C). Для этого необходимы три отдельных экструдера, которые соединены в одну щелевую головку. Такую конфигурацию иногда используют для получения совместимого или клеящегося слоя для присоединения многослойной пленки к детали, изготовленной методом литьевого формования (см. рисунок 6).
Рис. 6. Формирование трехслойной пленки типа А/В/С. Когда для того, чтобы обеспечить высокую отражающую способность, используют монослои металлических чешуек, можно включать в пленку дополнительные связывающие слои для того, чтобы удерживать слои вместе. Создание связывающих слоев требует использования третьего экструдера, их можно встраивать в четырехслойную или пятислойную пленки. После того, как пленка изготовлена, ее подвергают вдавливанию горячим формованием в форму, в которую ее будут помещать. Горячее формование С тех пор, как автомобильная промышленность проявила интерес к технологиям формования пленок, горячее формование перестало относиться к области магии, и было возведено в ранг технической науки. Горячее формование это просто технология, при использовании которой лист смолы нагревается до размягченного состояния, а затем быстро вдавливается в специально предназначенную пресс-форму с использованием вакуума или давления. Для горячего формования многослойных автомобильных пленок необходимо несколько специфических аспектов, которые не были необходимы при изготовлении однослойных низкотемпературных пленок. Следы быстрого охлаждения, усадочные раковины преформы и коробление являются распространенными проблемами, с которыми сталкивались производители на протяжении многих лет с переменным успехом. Возникают и другие проблемы, такие как двунаправленное и однонаправленное вытягивание. Причиной возникновения этих проблем иногда являются недостатки конструкции формы, вариативность толщины пленок или же плохое распределение тепла и давления. Для того чтобы получить брызговик или бампер с равномерным распределение окраски и постоянным блеском, необходимо избавиться от таких проблем. В настоящее время существует несколько пакетов программного обеспечения, которые могут помочь производителям пленок избежать появления дефектов и снизить количество брака. Более удачные конструкции форм с более высокими допусками в сочетании с более строгим технологическим контролем значительно повысили качество горячего формования. Реактивное литьевое формование После того, как термоформуемый слой помещен в гнездо для литьевого формования, производится обратное заполнение формы функциональной смолой. Существует большое количество используемых для этой цели армированных смол и сплавов, обеспечивающих надлежащие параметры термической, механической и химической стабильности готового автомобиля, которые необходимы производителям транспортных средств. С использованием данной технологии связано решение некоторых проблем. Первая проблема это выявление метода удержания термоформуемой детали в форме. Это особенно важно, поскольку высокоскоростные циклы и короткое время отверждения могут уменьшить перерыв между потоками, что, в свою очередь, может повлиять на скорость потока. Другой проблемой является создание пленки, которая будет приклеиваться к смоле после обратного заполнения. Этого обычно достигают за счет использования клеящих или других связывающих веществ с нижней стороны пленки. Другой распространенной проблемой является коробление. В зависимости от толщины пленки и ее состава, она может быть изолирующим слоем внутри формы, а это влечет за собой неравномерность распределения температуры в процессе формования. Это влияет на то, как происходит отверждение смолы, и, в результате, может произойти коробление готового продукта. Уникальное воздействие красителей, предназначенных для создания эффектов Разработчики рецептур пластмасс не могут подобрать цвет, соответствующий цвету покрытия жидкой краской, просто за счет получения информации о составе краски и приспосабливания ее к работе для экструдированных пленок. Создание соответствия цветов краски и пластмассы значительно более сложная задача. Соответствие может быть получено с первой попытки, а могут понадобиться и все пятьдесят в зависимости от того, какие смолы используются и каковы компоненты краски. Одной из основных проблем является нестабильность органических красителей, которые хорошо функционируют при использовании в жидких красках, но не выдерживают воздействия высоких температур, которые иногда используются при обработке смол конструкционных марок. Это особенно справедливо в отношении оттенков красного и синего из всей палитры красок. Два предложения могут помочь преодолеть эту проблему: следует использовать для получения оттенков красного чешуйки с покрытием оксидами железа, или же использовать слюдяной краситель с покрытием из органического абсорбированного красителя. У компании Engelhard имеется линия продуктов-красителей, которые называются Dynacolors®. Это продукты на основе слюды, которые имеют дополнительный слой органического красителя, приклеенный к их поверхности. Во время фазы плавления слюдяной субстрат действует как поглотитель тепла, и позволяет термически стабилизировать органический краситель на поверхности. Также имеется целый ряд продуктов, дающих оттенки синего, которые могут работать практически с системами любых смол. Другой проблемой, с которой сталкиваются составители рецептур пластмасс, является использование металлических чешуек. Если металлические чешуйки не стабилизированы растворителем ли добавкой, они могут быть взрывоопасными. Это становится проблемой для технологов, которые сталкиваются с образованием статического электричества в процессе экструзии. Одним из выходов является использование увлажняемых марок металлов. Поскольку металлические чешуйки часто увлажняются летучими веществами, которые способны смешиваться с системами жидкой покраски, эти растворители могут вызывать вспышки и даже взрывы при контакте с расплавленной пластмассой. Некоторых их этих проблем можно избежать за счет использования вентилируемого цилиндра экструдера, или за счет использования металлических чешуек, которые увлажняются нелетучими маслами. Масла по своей природе гигроскопичны, и им свойственно притягивать влагу. При использовании некоторых систем смол дополнительная влажность может создавать проблему. К сожалению, использование металлических чешуек или металлоподобных красителей имеет большое значение для подбора соответствия цветов жидких красок и пластмасс. Без использования этих продуктов практически невозможно получить надлежащую непрозрачность, отражающую способность и яркость при различных углах зрения. Другое предложение сводится к использованию металлоподобных красителей вместо металлических чешуек. Эти продукты широко представлены на рынке целым рядом производителей, они состоят из полупрозрачного субстрата диоксида кремния или слюды, который покрывает один или два слоя оксидов различных металлов, таких как железо, титан или драгоценные металлы. У этих продуктов нет компонентов, связанных с взрывоопасностью в сухом состоянии, и им также не нужно увлажнение с помощью летучих растворителей. Другим препятствием, которое встречается на пути составителей рецептур, как при создании красок, так и при создании пластмасс, является чистота цвета, но здесь составители рецептур пластмасс имеют преимущество. При изготовлении некоторых машин класса «люкс» эффект светящегося покрытия достигается за счет технологии нанесения трех слоев покрытия. Это процесс, требующий больших затрат времени и средств, поскольку необходимо трижды покрасить поверхность. Первый слой это основной цвет, второй слой наносится красителем, предназначенным для создания эффектов (обычно белый перламутр или иной интерферированный пигмент), а третий слой прозрачный. У готового продукта покрытие превосходного качества, красители, предназначенные для создания эффектов, переливаются и придают покрытию различные оптические свойства в зависимости от угла наблюдения. К счастью, в этой области экструдированные пленки прекрасно себя проявили. Здесь тот же эффект может быть получен с использованием трехслойной пленки, изготовленной в один этап, в отличие от технологий с использованием жидкой краски, при применении которой необходимы три этапа. У составителя рецептуры пластмассы есть также дополнительное преимущество изменения толщины между слоями, а также введения дополнительных прозрачных слоев между этими слоями для того, чтобы обеспечить увеличение глубины и богатства цвета, превосходящих по своему внешнему виду получаемые при нанесении трехслойного покрытия жидкой краской. В слой, содержащий красители для создания эффектов, могут быть добавлены оптические спейсеры, или же их можно добавить в прозрачный слой для того, чтобы еще более усилить эффект. Другим преимуществом, которое дает использование экструдированных пленок по сравнению с жидкими красками, является отсутствие необходимости в скрытии грунтовки. Создателям рецептур жидких красок необходимо уделять большое внимание добавлению нужных продуктов, которые смогут скрыть цвет грунтовки, нанесенной на стальную панель. Грунтовки необходимы для защиты стали от коррозии. Поскольку эти пленки формуются на пластмассовые детали, в использовании грунтовок нет необходимости, и они не смогут повлиять на окончательный внешний вид готового продукта. При изготовлении пленок с красителями, предназначенными для создания эффектов, следует обратить внимание на несколько моментов. Когда такие красители добавляют в смолу, меняется реология расплава. Это также повлияет и на пропускную способность обработки экструдируемого вещества. Другим аспектом является влажность. Красителям, предназначенным для создания эффектов, свойственно привлекать поверхностную влагу, поэтому необходимо тщательное высушивание. Еще одним аспектом является повреждение красителя в процессе обработки. Ниже будет подробно рассмотрен каждый из этих аспектов, и будут предложены рекомендации и пояснения. Добавление красителей, предназначенных для создания эффектов, оказывает влияние на реологию, перенос тепла и пропускную способность. Небольшой на 2 см одношнековый лабораторный экструдер со шнеком 24:1 L/D может экструдировать 20% окрашенный концентрат со скоростью 2,5 кг в минуту. Когда в концентрат добавляют красители, создающие эффекты, такие как оптические спейсеры, скорость прохождения через агрегат может увеличиваться на 30%. При экструзии в тех же условиях обработки, маточные смеси с оптическими спейсерами гранулируются по-иному. Гранулированные маточные смеси с оптическими спейсерами (рисунок 7a) тоньше и имеют относительно размытые концы по сравнению с маточной смесью, не содержащей оптических спейсеров (рисунок 7b).
Рис. 7. a) Поликарбонатная маточная смесь с оптическими спейсерами, b) Поликарбонатная маточная смесь без оптических спейсеров. Как уже говорилось ранее, субстраты из слюды и боросиликатов действуют как изоляторы во время обработки пластмассы. Хотя это явление может помочь защитить абсорбирующий слой на поверхности красителей, они обладают свойством удерживать тепло и делать поток расплава более горячим на протяжении длительных периодов времени. Это изменяет поток расплава смолы, а также влияет на время прохождения через агрегат и отверждения. Можно продемонстрировать количественный показатель изменения реологии на значениях индекса текучести расплава смол по сравнению с окрашенными смолами. Индекс текучести расплава поликарбоната: | 10,9 вязкость по Гарднеру-Хольдту. при 300°C | Индекс текучести расплава поликарбонатной маточной смеси с оптическими спейсерами: | 25,3 вязкость по Гарднеру-Хольдту при 245°C | Индекс текучести расплава поликарбонатной маточной смеси без оптических спейсеров: | 14,7 вязкость по Гарднеру-Хольдту при 300°C |
Проблемой для некоторых чувствительных к влажности смол, таких как поликарбонаты и иономеры, является удержание влаги. На прочие смолы, такие как олефины, не влияет гигроскопическая природа красителей, создающих эффекты. В соответствии с рекомендациями производителя предлагается, что до экструзии эти красители будут высушиваться отдельно или же в смеси сухих материалов. При обработке красителей, создающих эффекты, может стать проблемой повреждение самих красителей. Эти продукты обычно тонкие и хрупкие, они могут раскалываться на небольшие фрагменты, когда они подвергаются излишнему перемалыванию или подрезанию. При повреждении красители с покрытием из оксидов металлов они могут потерять свои свойства цвета и блеска, чешуйки металла могут погнуться и утратить свою отражающую способность, а оптические спейсеры могут раздробиться на части и утратить свою способность создавать глубину изображения. Имеется несколько способов, чтобы свести к минимуму такие повреждения. Самым простым способом является непосредственная экструзия сухой смеси смол и красителей вместо создания маточной смеси. Если этот вариант не рассматривается, красители, создающие эффекты, должны добавляться в отдельный питатель после технологического процесса, где смола находится уже в стадии частичного расплава, для того, чтобы снизить нагрузку на красители. Результаты и сопоставление с жидкими покрытиями При подборе соответствия цвета пластмассовой пленки и жидкого покрытия, лучше использовать смолу, указанную для готового пленочного продукта. Это не тот подход, который обычно используется для подбора соответствия исходного цвета при литьевом формовании, где составитель рецептуры должен выбрать, что изначально формовать в полистироле, затем как подобрать наиболее близкое соответствие, и как завершить процесс при разработке рецептуры поликарбоната. Это логичный подход, поскольку полистирол это относительно бесцветная смола, значительно менее дорогая, и она не нуждается в высушивании перед формованием. Когда же делается попытка использовать этот подход при работе с экструдированными пленками, цветовое пространство существенно сдвигается при переходе с одной смолы на другую, и возникает необходимость полного изменения рецептуры соответствия. Для получения исходного соответствия можно экструдировать однослойную пленку. Можно отдельно экструдировать прозрачный слой и окрашенный слой, а затем штамповать вне линии для изменения цвета. Можно также работать с прессованными деталями, но это даст только очень грубое приближение к нужному цвету, поскольку красители, создающие эффекты, не будут присоединяться так, как они это делают при использовании технологии экструзии. Практические примеры из мировой практики На рисунке 8 дана фотография стальной панели из Детройта с покрытием жидкой краской в сопоставлении с подобранной по цвету трехслойной поликарбонатной пленкой.
Рис. 8. Панель, с покрытием жидкой краской и экструдированная пленка. Поликарбонатная пленка состоит из конфигурации A/B/A бесцветного слоя/окрашенного слоя/бесцветного слоя. Каждый бесцветный слой имеет толщину 0,25 мм, а окрашенный слой 0,5 мм. Слой красителя состоит из пяти различных красителей, создающих эффекты, плюс углеродная сажа для оттенка. Общая концентрация красителей, создающих эффекты, и окрашивающих веществ составляет 1,75%. Эти панели были сфотографированы аппаратом Mac Beth Skylight при 15 градусах с использованием дневного света, источника D65, и, хотя соответствие цветов не полное, результаты очень близкие. Интересно отметить, что блеск сильнее у экструдированной пленки, а не у панели, окрашенной жидкой краской. На рисунке 9 дан цветовой график, сопоставляющий краску и пленку по параметрам CIE (Международной комиссии по освещению). 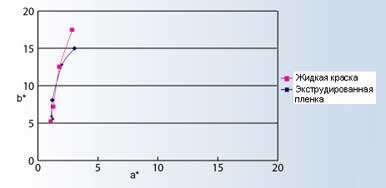 Рис. 9. Смещение цветов для жидких красок по сравнению с экструдированной пленкой. Готовая продукция На рисунках 10-12 даны некоторые из прототипов, которые в настоящее время рассматриваются для применения при отделке внешних деталей автомобилей. На рисунке 10 показан небольшой сформованный с введением окраски брызговик, который получен литьевым формованием со сплавами PC/ABS. Обратите внимание на следы течения пластика на поверхности. 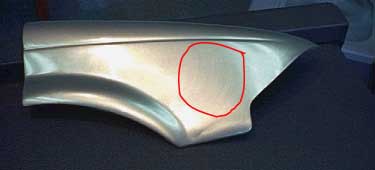 Рис. 10. Изготовленный литьевым формованием брызговик с окраской в процессе формования. Рисунок 11 представляет собой фотоснимок трехслойного поликарбонатного листа до горячего формования, а на рисунке 12 показан фрагмент этой же пленки, обработанной горячим формованием для получения формы коробки передач.
Рис. 11. Ролик многослойной поликарбонатной пленки.
Рис. 12. Изготовленная горячим формованием форма коробки передач из многослойной поликарбонатной пленки. Благодаря усилиям многих составителей рецептур пластмасс, производителей смол и красителей, а также компаний-производителей технологического оборудования, в наши дни стало возможным создание автомобиля из пластмассы или сплавов пластмасс, которые выглядят так же, как и транспортные средства из металла, окрашенные жидкой краской. Стало возможным также создание окончательного покрытия, которое превосходит по своим параметрам покрытие из жидких красок, как по износостойкости, так и по внешнему виду. Более того, использование обработанных литьевым формованием смол позволяет производителю создавать автомобили обтекаемых форм, которые до сих пор было невозможно получить со сварными стальными деталями. При относительно небольшом переоснащении можно быстро менять формы и цвета автомобилей, что позволяет осуществлять массовое производство автомобилей по индивидуальным заказам потребителей. Еще имеются вопросы относительно развития технологии, которые хотелось бы задать. Во-первых, вопрос о безопасности. Насколько безопасен автомобиль, изготовленный из пластмассы? Хотя пластмассовые пленки и могут быть более износостойкими, чем покрытия из жидкой краски, в какой мере пассажир внутри автомобиля находится в безопасности? Имеются новые смолы и сплавы, разрабатываемые в настоящее время, которые обладают теми же свойствами, что и сталь, но это все же не дает полного ответа на вопрос. Другим вопросом является вопрос о причине, по которой мы хотим создать такой пластмассовый автомобиль, который бы выглядел как покрашенный металлический. Почему бы не создать транспортное средство с уникальной обработкой поверхности или формой, создание которого возможно только при использовании этой новой технологии? Постановка этих вопросов затрагивает важные проблемы, стоящие перед производителями автомобилей, и к решениям, в наибольшей степени совместимым с запросами потребителей, придут компании, которые имеют в своем распоряжении лучшие творческие силы и которые получат большую часть рынка. Дорин Беккер, http://www.omnexus.com |